Structures for burning sawmill waste originated in the 1880ās and were common in the west coast lumber producing regions until the Clean Air Act of 1970. By the mid 1970ās literally all sawmill waste burners were shut down but thankfully not all were torn down. If you care to look you can find some 150 plus of these structures scattered through the Pacific Northwest still standing sentinel over abandoned mill yards and now open fields.
When I say common I mean like gas stations on every corner back in the day. This picture of a region in Northern California will give you some idea of what I am talking about.

They were called; Burners, Slash Burners, Wigwam Burners or Teepee Burners depending on where you were located. In my region of Northern California in the Redwood country they were known only as Teepee burners and they were everywhere.
One of my best childhood memories was playing inside the burner on a rainy Saturday or Sunday while a small maintenance fire kept everything toasty warm and dry. I was first introduced to this activity by other kids while living in various sawmill camps in the mountains. We moved to near town for a while when I was about 6-7 years old and just down the road was a mill with a nice burner so I quickly introduced the local kids to this great fun. Unfortunately we only lived there a few months then off to another mill camp in the mountains.
Years later in a collection of photos I acquired there was/is a picture of that very mill and burner taken 2-3 years before our fun there. The place we lived is just out of site along the road that runs to the left. This is the G.L. Spires mill near Arcata, California. Circa 1950
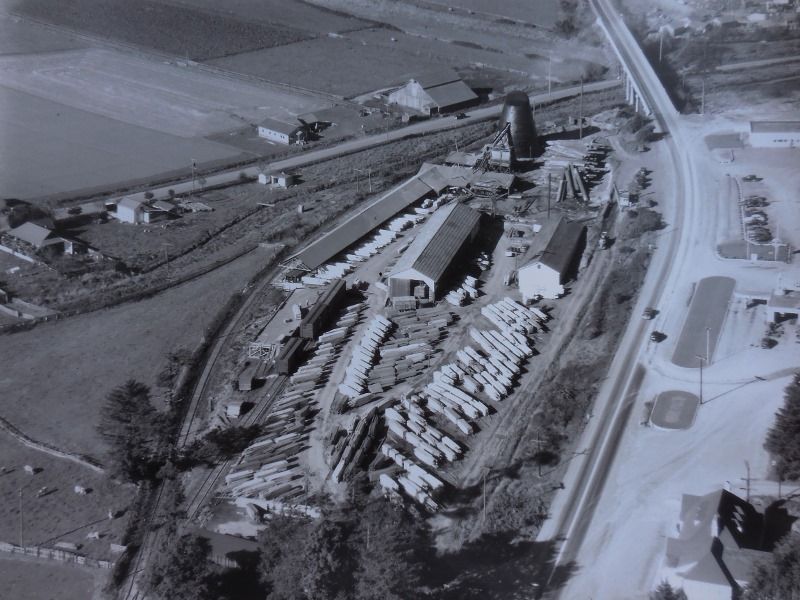
A brief history of burner development.
The first patent issued for a structure specifically designed for burning sawmill waste was to a Michigan company in 1888, and this basic cylindrical design dominated the industry until about 1915.
The concept of the waste burner was an immediate success. This is because the huge amounts of wood waste that accumulated around a mill site created an extreme fire hazard making fire insurance for mill owners almost impossible to acquire.
As an example of waste accumulation; Even by the 1950ās only about 30-40 percent of every logged tree was utilized, and this included the use of waste in the manufacture of paper, plastics, rayon, turpentine, broom handles, pressed fire logs, and particle board. In earlier years the percentages of usable wood was even lower.
Colby Engineering of Portland, Oregon introduced in 1916 a new type burner with a patented āair cooledā design. This introduced the teepee shape but used an inner and outer skin with air induced at the bottom between the skins and drafted upward to help cool the skins.
This design was effective and far less expensive to build and install than the old methods that used refractory brick liners or water jackets to cool the outer skin.
Of course nothing stays un-improved. In 1917 the Seattle Boiler Works applied for a patent for the first truly light weight wood burner design. āIt relied on a single layer of thin-gauge plate steel cladding arranged in a simple conical form with spot footings at each vertical support. Air was introduced into the burner by means of adjustable dampers on the lower circumference of the shelled surface. Practical and affordableāalmost crudeāthis design proved enormously popular with mill owners throughout the Pacific Northwest.ā*
The only major improvement to this design was in the air intake system. Instead of just a hole with a damper, the holes were provided with horizontal scoops on the outside, this caused the air all the way around the burner to enter in the same direction creating a cyclone effect that kept a hotter fire burning and sped the rise of the smoke and gases out the top.
Probably way more than anybody wants to read but couldnāt help sharing a little information on these iconic structures that once dominated the skylines of most western towns.
*Quote from; Wood Burners by Daniel Mihalyo, Princeton Architectural Press, 1997
If interested in further information here are a couple of web sites to visit.
https://www.flickr.com/groups/wigwam-teepee/
http://www.livinggoldpress.com/teepeetopiclist.htm
Thanks for taking a look