By popular demand, I have revived this old thread to document new work and my attempt to finish this project.
At the time, I failed to finish because I wanted to custom mill the doors and windows from acrylic using the CNC router at work. When I was unable to get router time before the contest close, I pretty much gave up. The flat has sat with it’s pencil sketch layout since early in 2017.
Early this spring I purchased a good supply of Fn3 scale cut cedar lumber and just last week picked up a well loved MicroMark mini table saw. Needing a project to utilize these purchases on, the first thing I thought of was this building. Rather than mill the windows and doors, I’ll build them up from wood, acrylic and and maybe a bit of styrene.
The first step was to remember exactly what I had planned, then consider some new options, like a shadow box interior similar to Cliff’s recent town fronts. So first, I went back and read every post in this thread. There were some relaly good suggestions offered that I passed on due to time constraints. Now that the deadline is gone by nearly 4 years, I no longer have that excuse! One thing I will seriously look at is operating doors in addition to the shadow box interior that will feature some vintage black and white interior photos lit by RGBW LED strips that I can control with my phone or tablet.
In order calculate maximum building depth, I needed to run clearance tests. That was today’s project using my 45 Ton loco and a few cars. The following photos illustrate that process and some decisions that were made based on testing. In this picture, the blue corner mark on the wall was the original planned position. I determined that by shifting the building 4 inches to the right, I could gain almost an inch of depth and not loose any of the car spots…
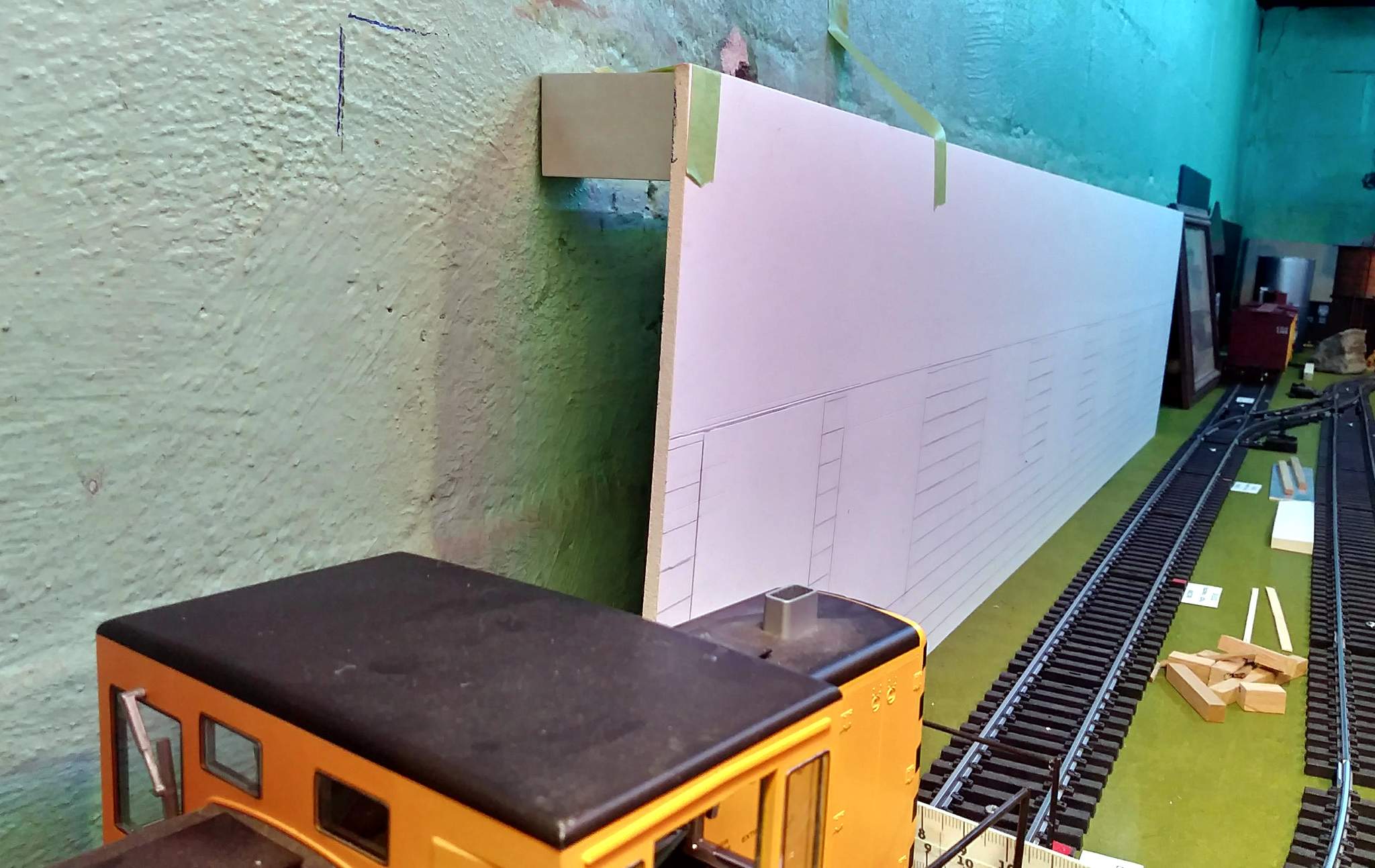
From the other side…
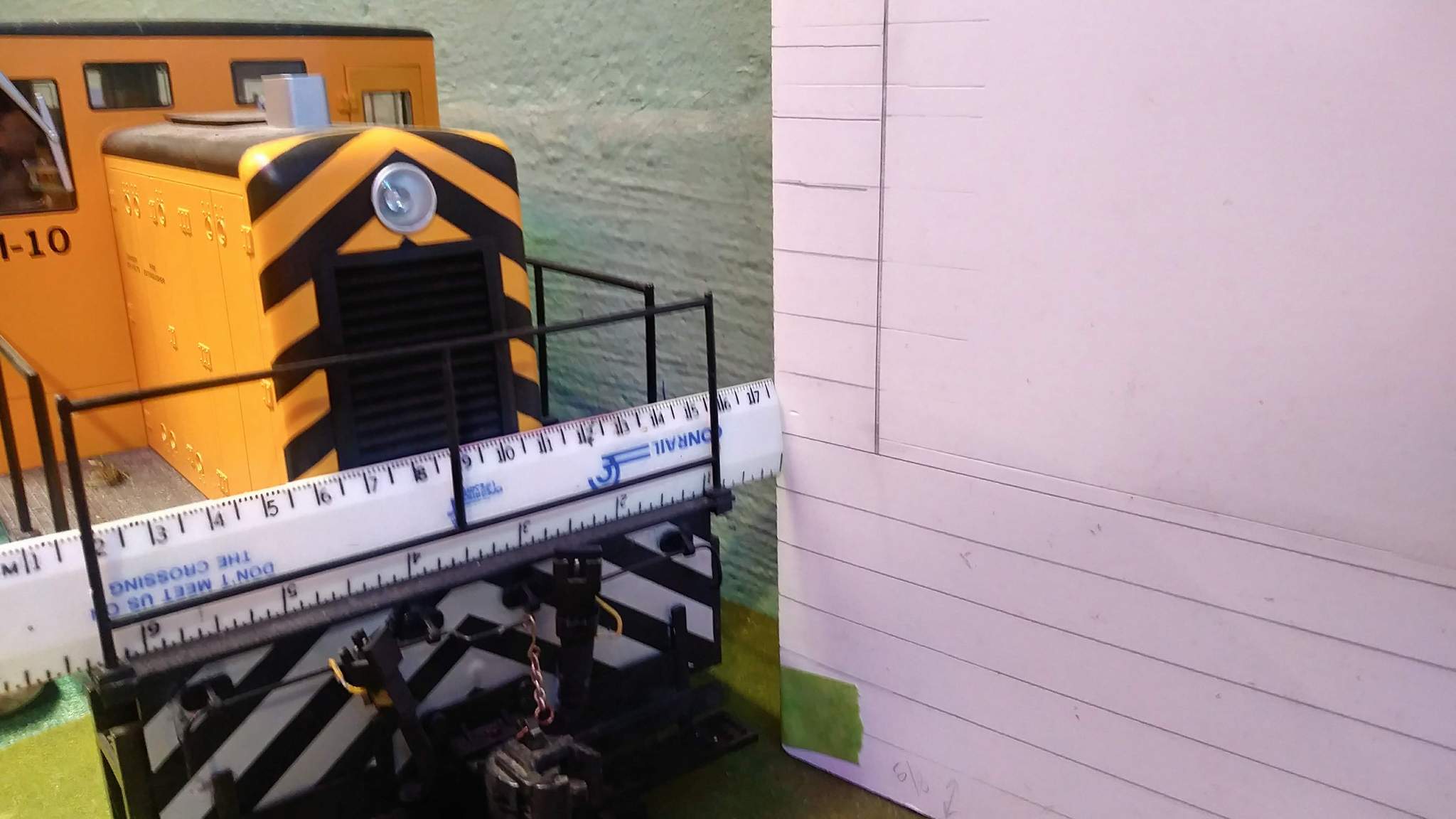
The result of this position shift and test was a gain of 7/8" more space for the interior leaving plenty of room. Next, I pushed this a bit further by adding a 3mm piece of coroplast as the back wall and positioning some verticals to mark the proposed front location. Once this was in place I ran extensive tests with the 45 ton and cars. I still need to check with my C19 to be sure the shift doesn’t cause a problem with the pilot overhang entering from the switch…
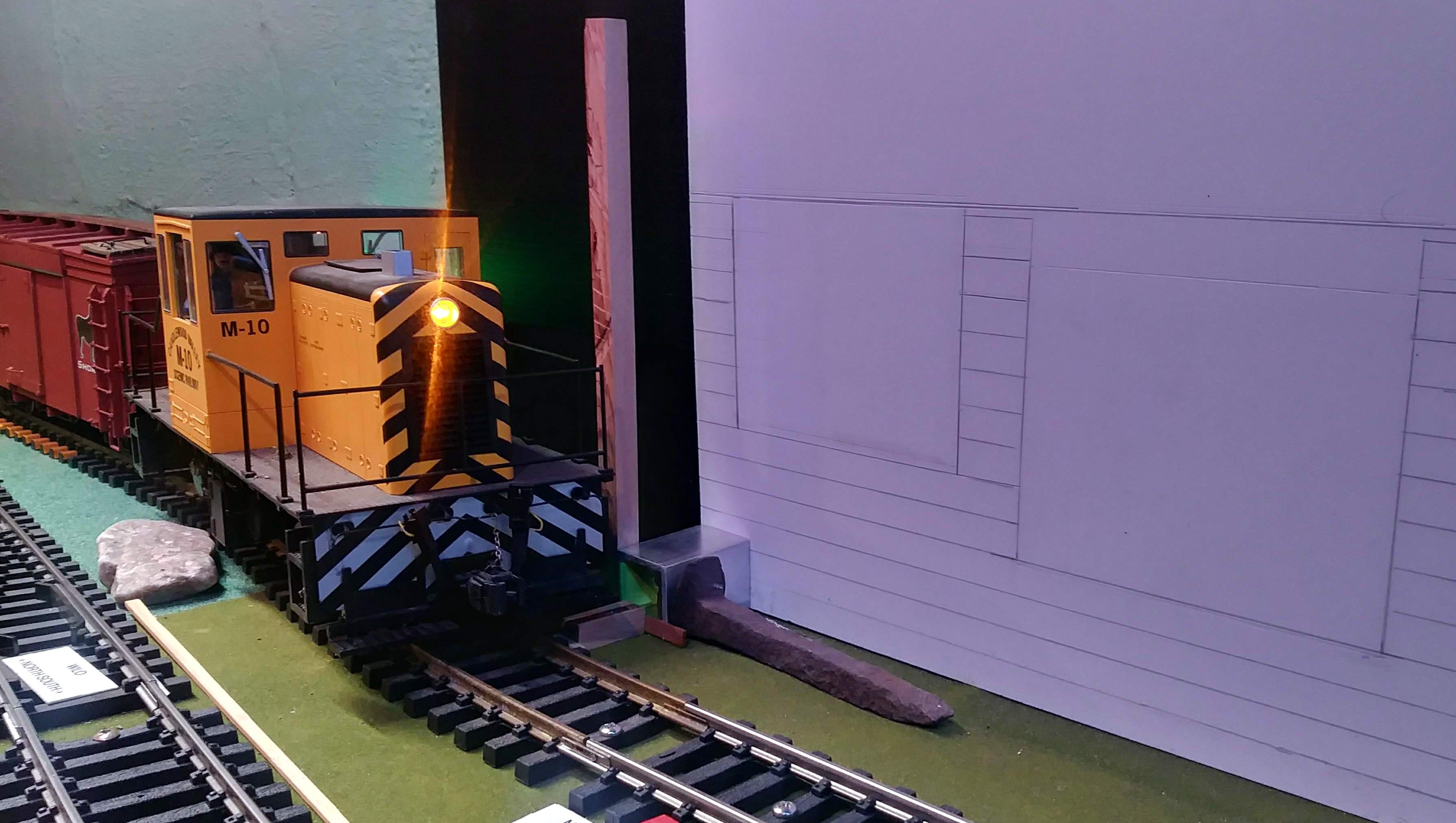
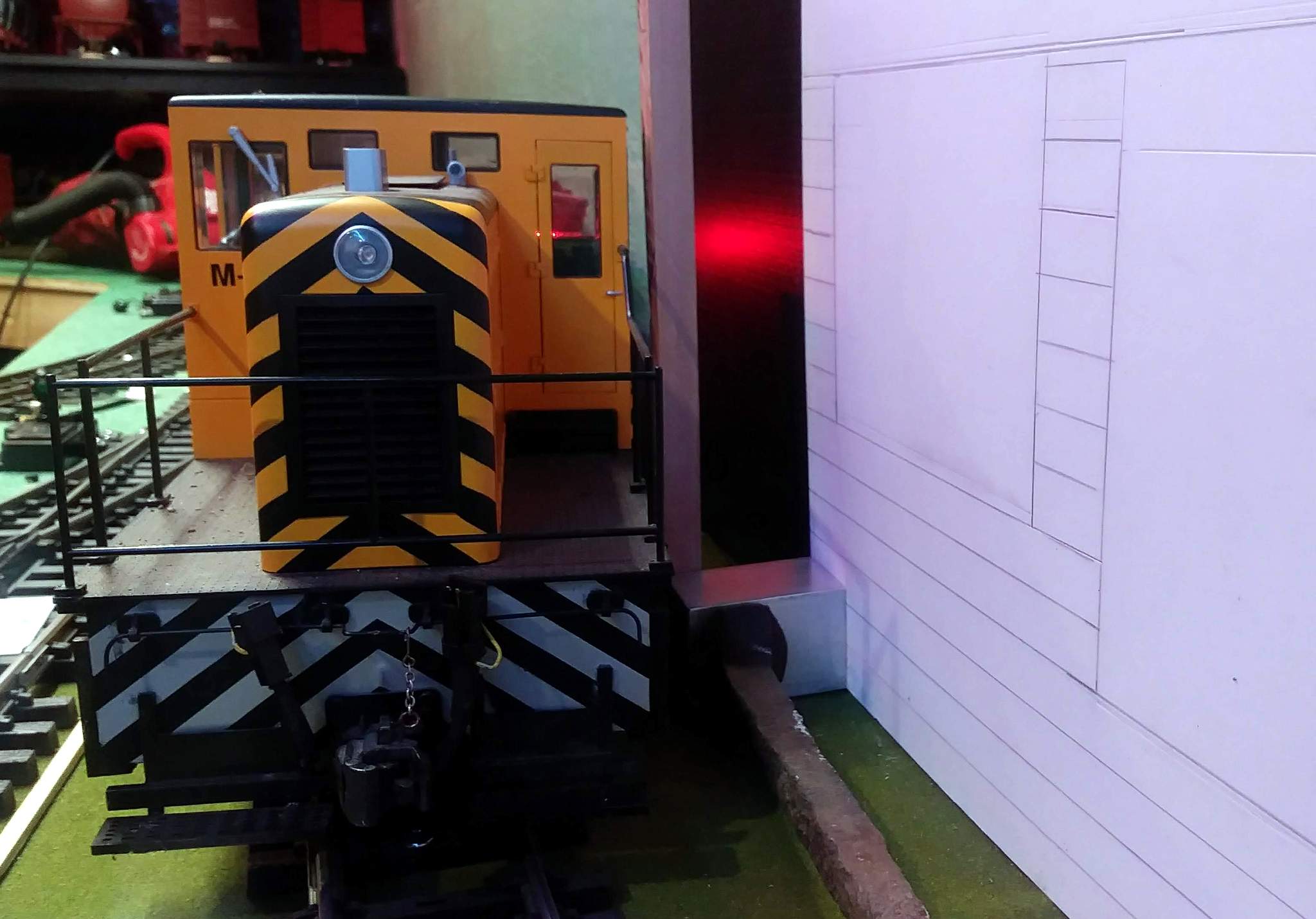
This picture illustrates how the shift to the right changes the car spots. This reefer is spotted where the old Door 3 Spot was…
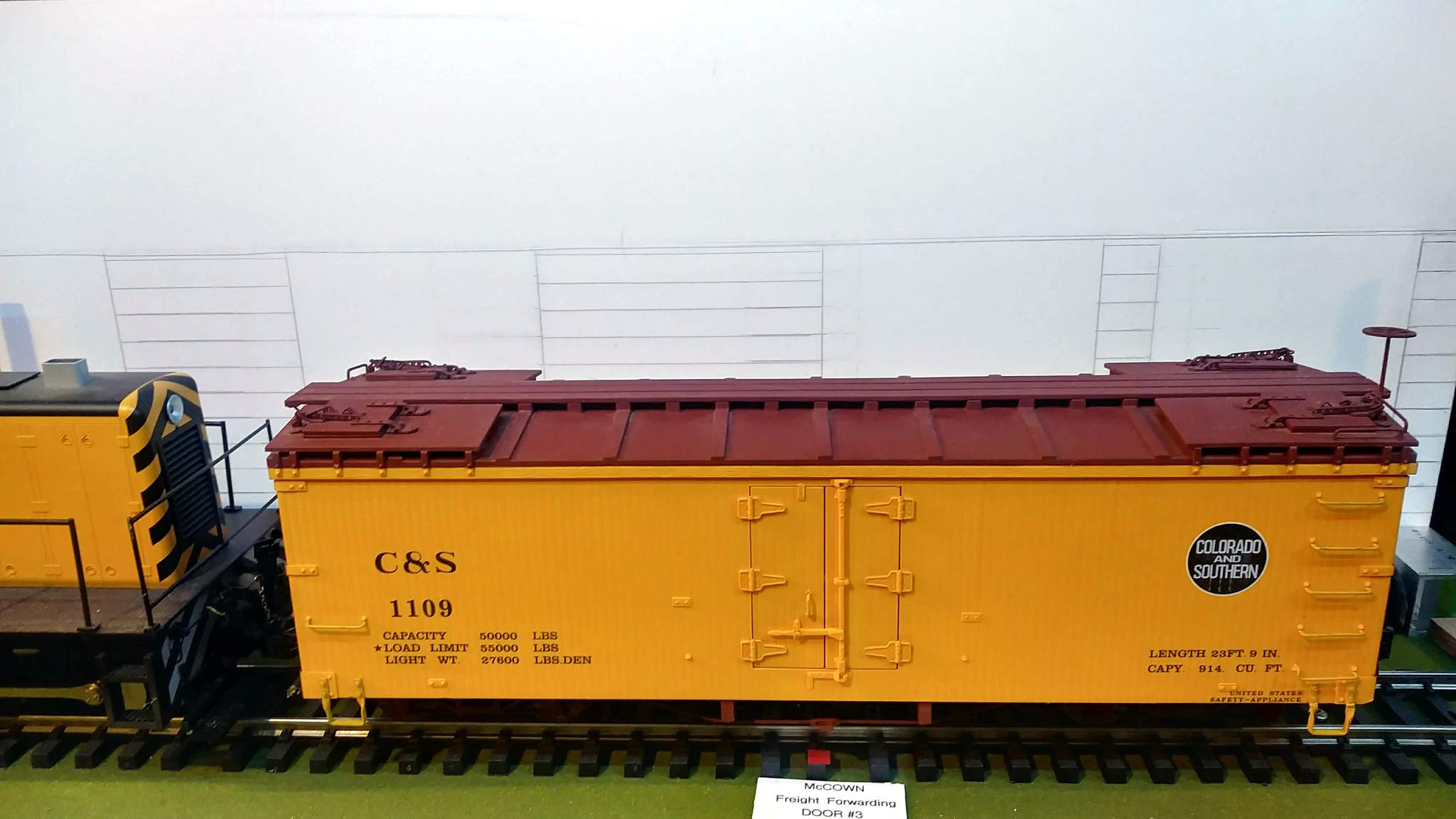
And then pushed into the new spot…
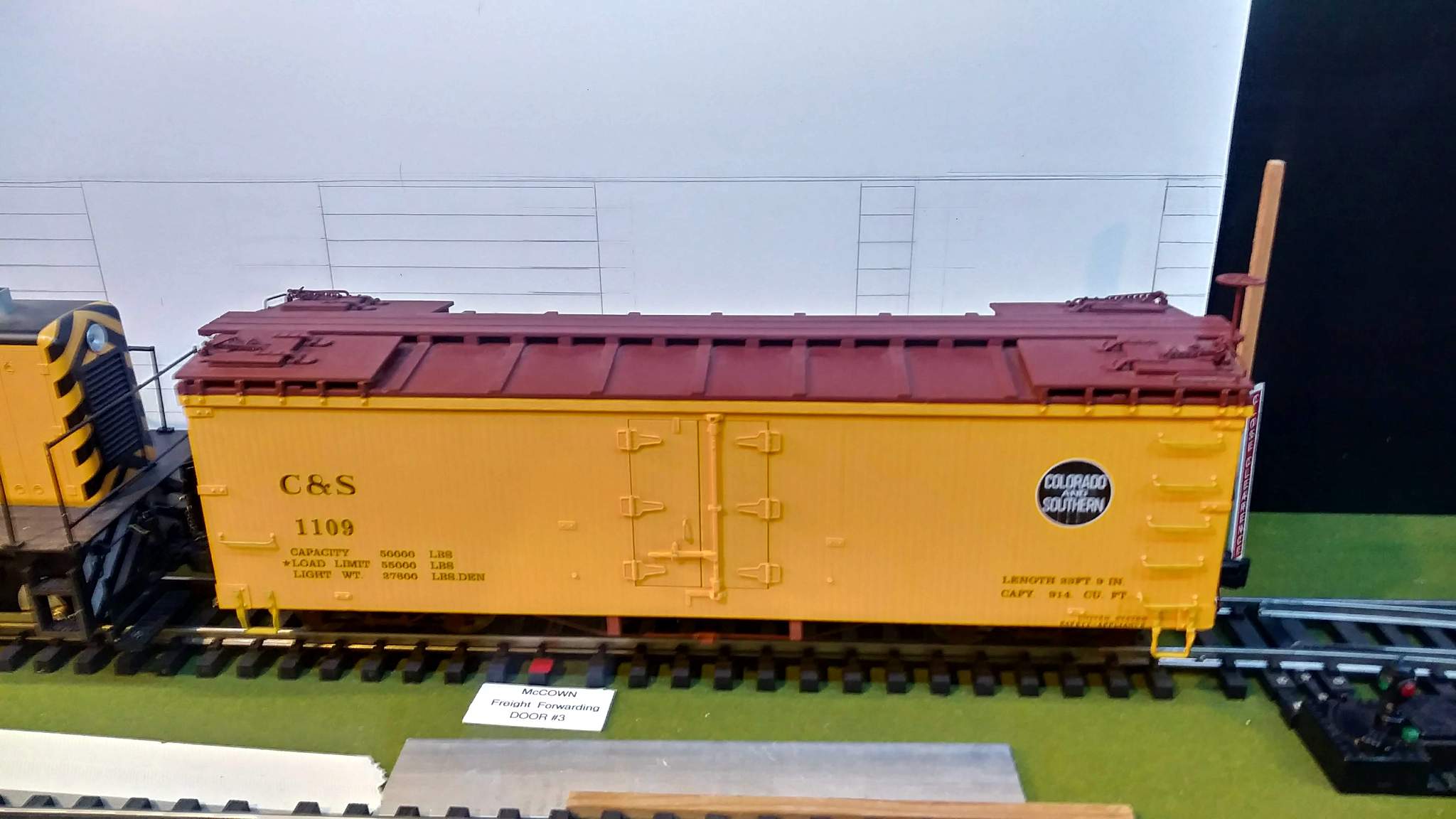
The new spot pushes the car end pretty close to the switch…
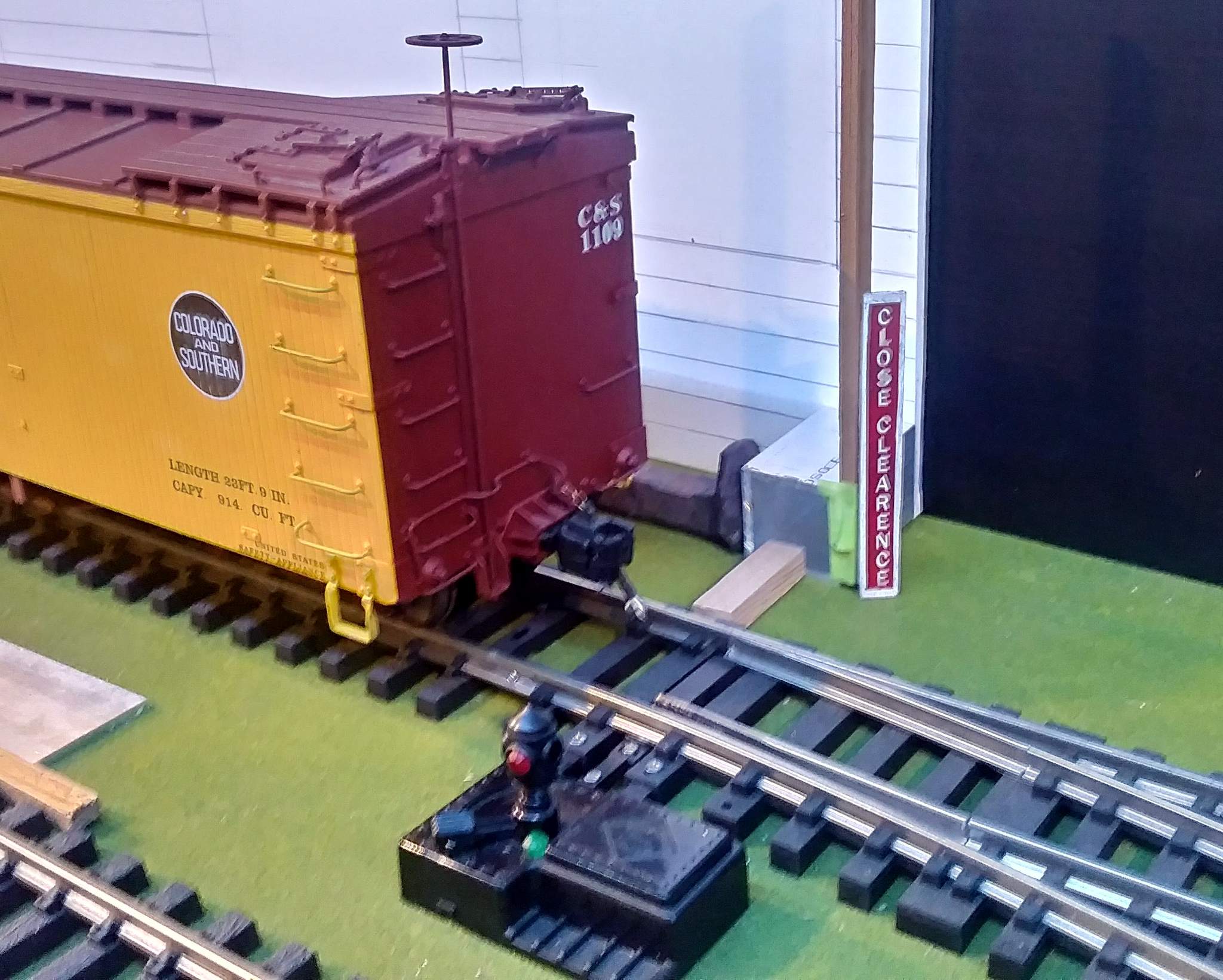
Which results in a minor coupler alignment problem when approaching from the switch…
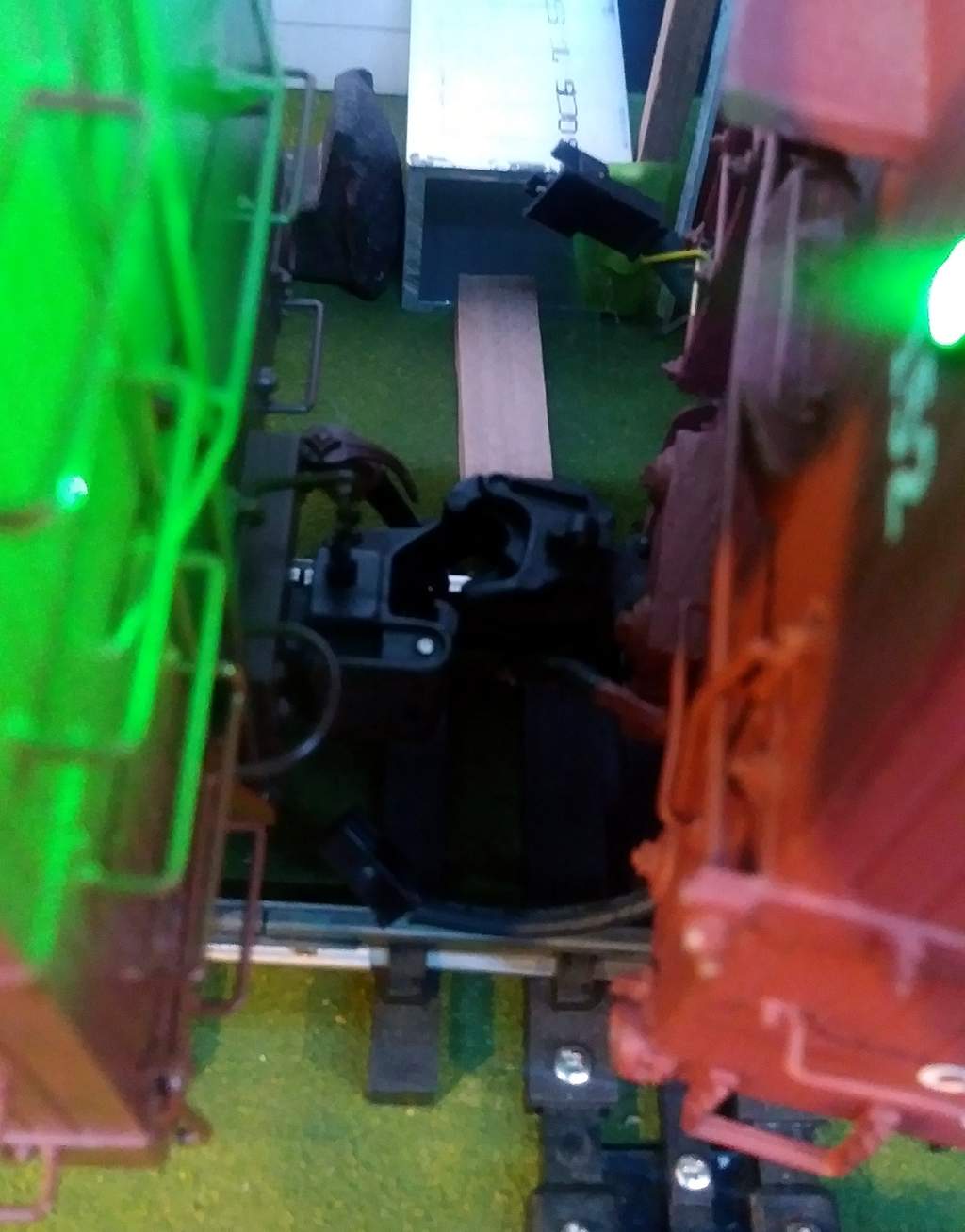
I’m willing to deal with that small inconvenience in order to gain enough room for a reasonable shadow box depth of 2.25".
This will be an on and off project based on weather. I have lots of things on my get ready for winter to-do list, but most of them requre at least dry weather, which has been scarce of late. I’ll work on this rainy days and evenings. It may take me until spring to finish, but I’ll update this thread when there is something to report.