And now, for some shingle talk! I know this is obscure, but I’m excited to learn some stuff today. Following in the footsteps of Dennis Rayon, who is using a similar material & approach, I think this shingling method is pretty neat, and deserves a little more description than I tend to produce. So here goes.
I received the material a couple days ago for this, .03 pine green ABS “Rowmark” from Johnson Plastics. It’s intended to be laser-cut, and is even marked with direction of grain for applications caring about that.
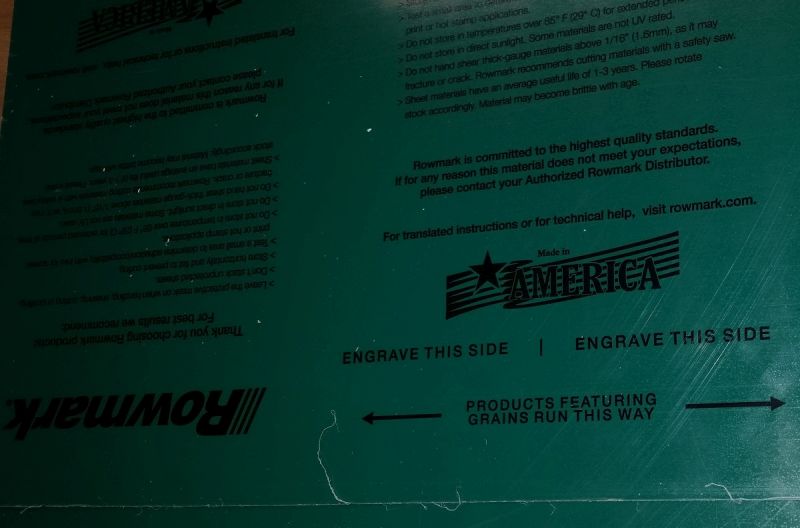
The “engrave this side” side has a matte finish, vs. gloss on the other.
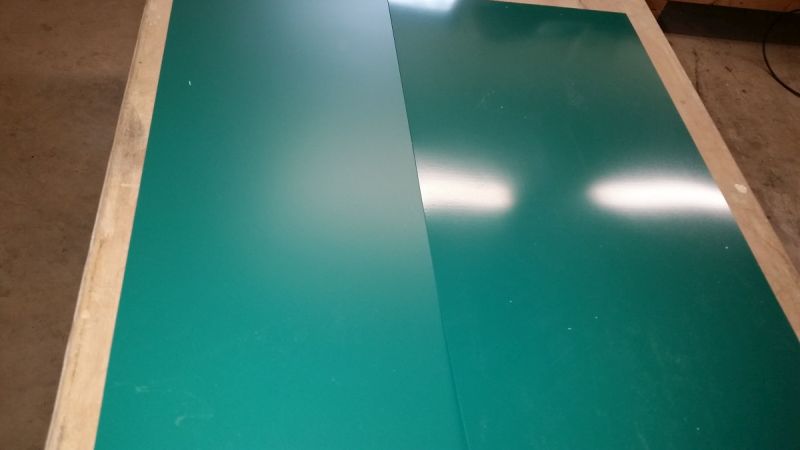
Though full 4x8 sheets are available, I purchased 2 1’x2’ sheets. Cheaper shipping, and my cutter can’t handle very much more. I started today by belt sanding (on the left, below) and then wire-wheeling the sheets (shown on the right):
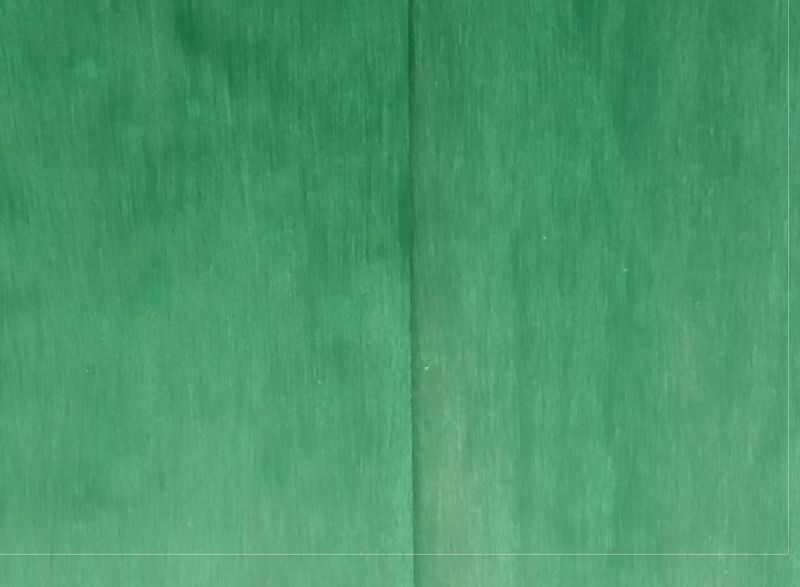
Not a huge difference, but the wire-wheeling (brush on a drill) helped to even out the oddities left by the belt sander. I found the brushing was better done with very low RPM on the drill.
Then came the lasering. For a set of strips, I set up the parameters to do all the engraving first, internal shingle cuts second, and final / outer cuts last. This is because the material tended to warp with all this, and the last bits of connecting material helped keep things registered. BTW, once a strip got fully cut, it laid down. Before then, things looked like this. You can see things curling near the cutting action.
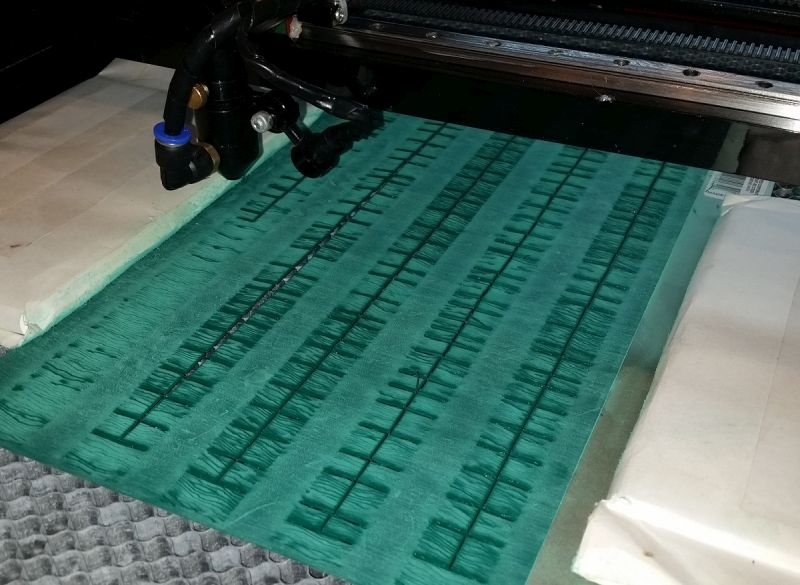
Here’s how the strips began to come out.
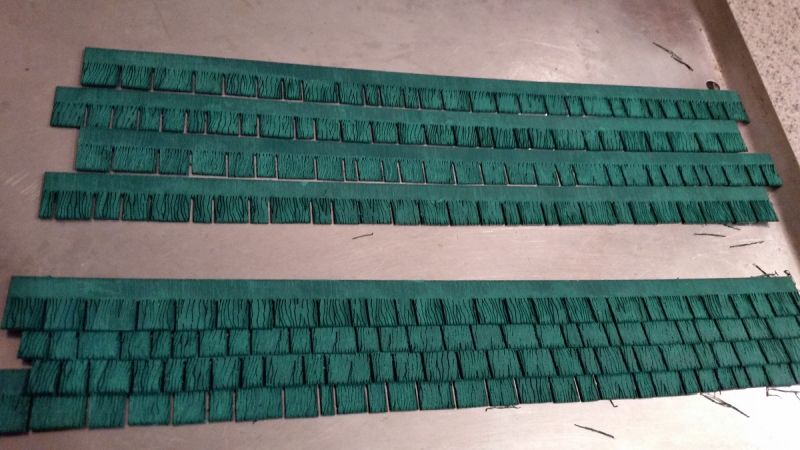
I messed with settings with each batch, trying to get the speed up and power down, yet produce the needed graining and cutting. I also wanted the engraving to NOT produce raised ridges. Again, this is .03 ABS, and settings will differ for other materials of course. But in case anyone wants to know, here’s my settings (for power reference, I’m using a 60w laser):
By the time I finally arrived at these settings, I was cutting batches of 10 strips in 25 minutes, or 2.5 min/strip. I needed 50 strips (at 12" long), so here’s what 50’ of shingle strip looks like.
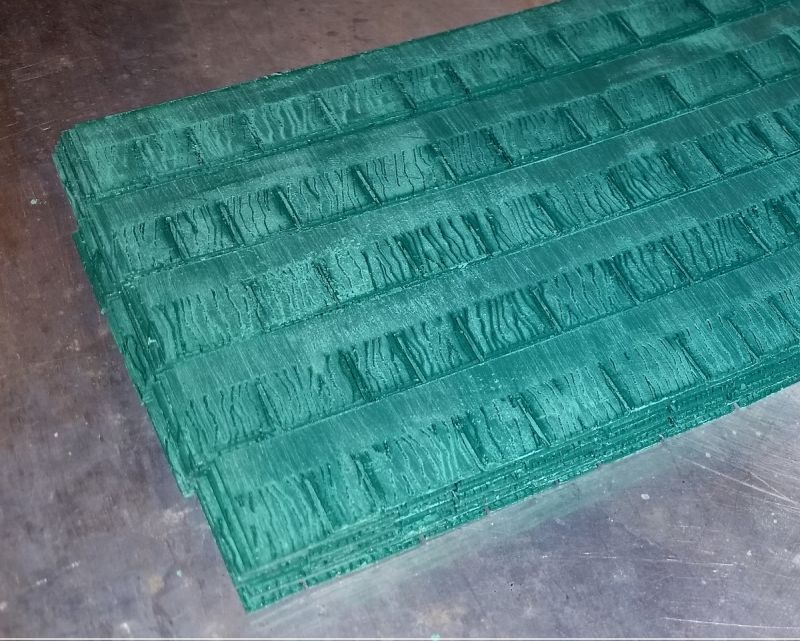
It’s sort of powdery still from the sanding, but that should go away with the next steps of cleaning / staining. Then comes installation! Anyone remember those Campbell shingle strip rolls (for HO)? I used those as a kid, and had a blast. Maybe that’s why I’m going off the deep end on this phase of the project! 
Thanks for your interest,
Cliff
PS, someone please ask me why I’m using green shingles… 