So I had to help family the last couple days, and wasn’t able to post. First thing is to make a correction, I realize that I said we use Fir strips for the ties…Jenn informs me that I was wrong, and we use Ceder for the ties. Larry buys tongue and groove Cedar for walls and we rip those into strips for the tie making machine.
We’re leaving back to Portland tomorrow since my sister has evacuated to my dads. I have put together some pictures of the final building of the middle yard loop, but won’t have time to post for a couple days.
I mentioned in an earlier thread that we changed the way we make frogs during this project. The old method was manual and used jigs and keyway cutters, and only allowed for a few frogs, #5,7,10, and 14. As seen in the March 14, 2018 post in the fourth picture, I described cutting our old frogs down in length, and this got me thinking about a new method. We had already been thinking about making them using cnc, and I had laser cut some custom mill vise parallels to facilitate the process. However, by the nature of trying to fit all these curved turnouts in the allocated space, we were going to need many different angles of frogs, and each size would need its own parallels and fixtures.
The new cut down design made Larry and I realize, that we could profile the frogs instead, reduce the number of operations to produce them, and allow for any angle to be produced. So Larry created a model in Solidworks of the frog using drawing relations, to allow the model to regenerate a frog simply by changing one dimension of the frog…the angle. In the mean time, I set about teaching myself the CAM system that comes with Solidworks nowadays, so we could generate cnc g-code. The beauty of this, is that if we design a turnout to fit a tight location, or an intricate turnout such as the tandems, we can create any frog needed, even if the angle was non standard such as 8.175 degrees or whatever, and the toolpaths and g-code would be automatically created and ready for production.
The first thing we did was 3D print a couple to prove out the concept…here is a picture of one I found on my phone.
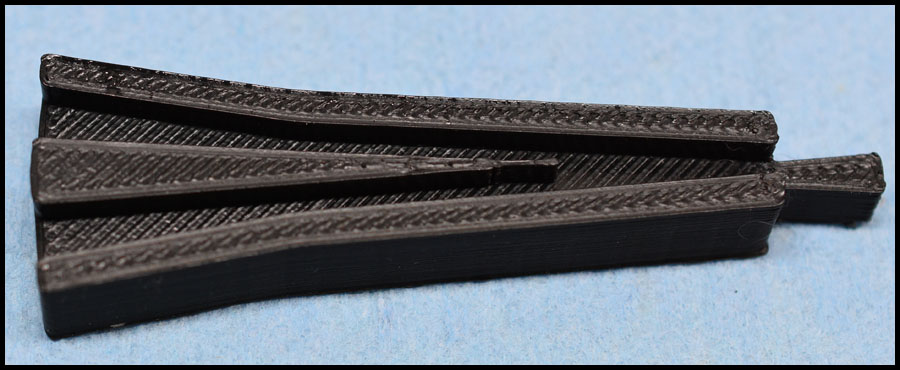
Next was to try it on the mill. We made the first couple out of aluminum to test our toolpath strategy and such. We can now make the frogs in only four operations instead of nine, and of course, the cnc is much faster than manual.
I found one picture on my phone of the first operation in aluminum…
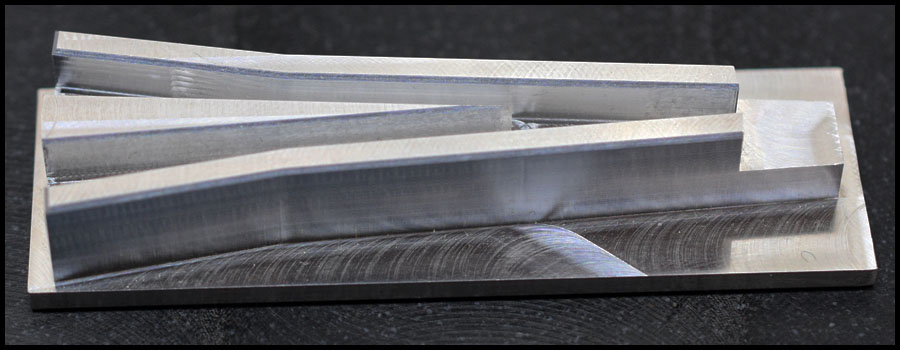
The second operation is to turn them upside down and mill the extra material off. Even though the angle of the frog creates a substantial difference in lengths between say #3 and #14 frogs, the dimensions at each end of the frog are consistent enough that I was able to mill a shape into a set of steel vise jaws that allow me to clamp two frogs at a time, spanning from one vise jaw to the other, and remove the excess material and set the thickness of the frog.
I don’t have any other pictures of these operations on this computer so I can’t provide much more detail until later, however, the third operation involves milling away the area where the rails get welded on the small end of the frog. This is two simple and fast operations that don’t take long at all.
Once we made some out of steel, and fine tuned speeds and feeds, I went ahead and created programs for #3 through #14 frogs and ran production runs of each size so now we have lots of frogs. If we need a special size, I can make them easily as needed.
One fly in the ointment, however, is that Larry got annoyed when Solidworks changed policy this year, and won’t let him have a copy on his laptop as well as the shop computer, so he cancelled it. So next time we need frogs, I have to redo everything in Fusion 360…oh well, just another learning curve. Fortunately, I have already learned to create models in Fusion, I just need to learn the CAM system.
That’s it until I’m settled back in at home in a couple days.
Happy steaming
Karl
Edited to correct some punctuation and missed capitalization of some names.