Its not 11:00 on Tuesday but its close enough, so as promised I have an update on an alternate method to glue all the 3D printed parts together, or in this case, weld all the parts together. Back story, the other day while wondering around the internet, yes, I do that from time to time, go figure, I stumbled across an ad for a 3D pen. Now I was aware that 3D pens existed but never had a use for one. For those not familiar with 3D pens they are merely a hand held 3D printer used for drawing, writing, art, etc out of plastic just like a 3D printer. Below is a video example.
SEE THE NEXT POST FOR THE VIDEO
Why do videos disappear if you edit a post containing one?
Anyway, as I looked at the pen I asked myself … “Dan, could you use the pen to weld the parts together” … Self said … “why not” … and I replied … “Self, it just seems to logical and easy, that’s why” … sorry, I’m rambling. So I turned to u-tube and did a search on welding PLA with a 3D pen and low and behold there were many videos of folks doing just that. Now why didn’t I think of that, hmmmmm.
Well, I ordered me self a 3D pen and gave it a shot and it works like a charm.
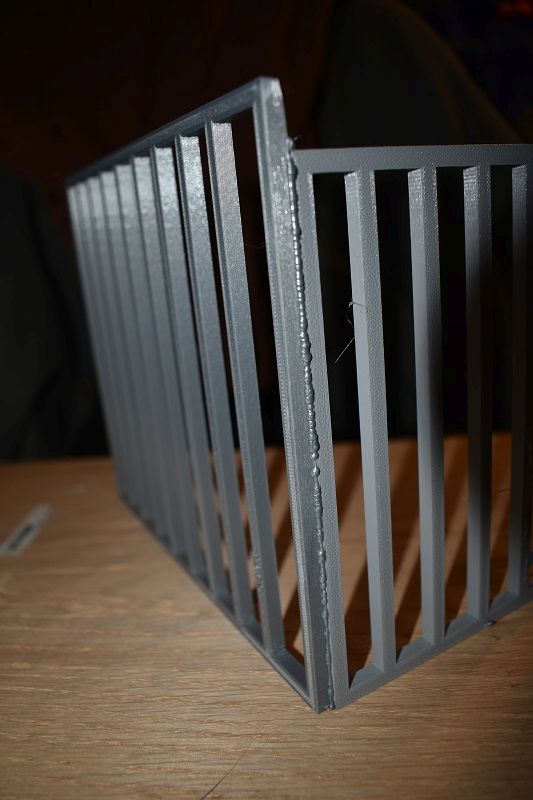
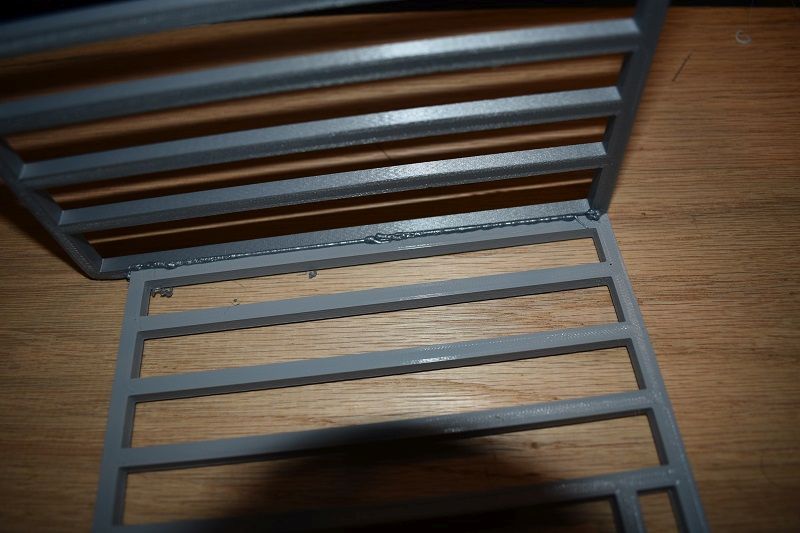
Yeah, I know it looks like a bull’s a$$ tied up with a barbed wire fence, but the strength is exceptional. Like any good weld or glue for that matter, the parent material breaks before the weld. I think with a little practice … the welds above were done about 2 minutes after unboxing the pen with no practice … one could make the welds look like real welds. Also, it would help if the designer of this project would have taken the welding into account and beveled all the mating surfaces to provide a place to build up the weld and still have a flat surface (http://www.largescalecentral.com/externals/tinymce/plugins/emoticons/img/smiley-yell.gif)Wonder if I can talk him into starting over (http://www.largescalecentral.com/externals/tinymce/plugins/emoticons/img/smiley-undecided.gif)
EDIT: The pen uses the same filament as the printer so no additional supplies needed.