Ok, so here is the finished mold after I had cleaned all the residual flashing that had gotten under the master stones.
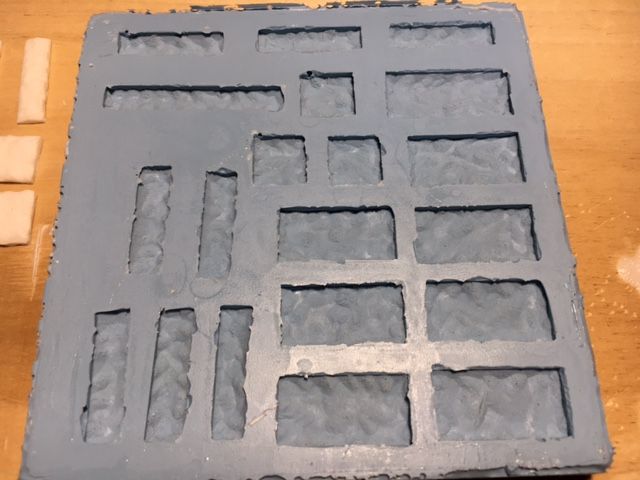
As stated earlier, leaving a gap, ever so small as it was, under some of the stones allowed the mold material to run under them and leave a thin film of silicone rubber. In this case it simply presented a cleanup issue and a pain in my rear. Lesson learned.
So, next I sprayed the mold with mold release and let that dry per the instructions and then mixed the resin and poured it into the mold. Second mistake. While pouring the resin, I got in a hurry and poured too much and it went everywhere. Luckily, I had prepared for a spill so the mess was limited to just the mold. But now I had a film of resin all over the top of the mold. I took a straightedge and removed what I could but I couldn’t get it all. Oh well, nothing else I could do at that point but wait and let it cure. I left the resin overnight and pulled the stones this morning. To my complete astonishment, they actually came out and looked like stones. I did have a lot of flashing around most of the stones due to my incompetence, but that simply took some time and a razor knife to cleanup. Here they are.
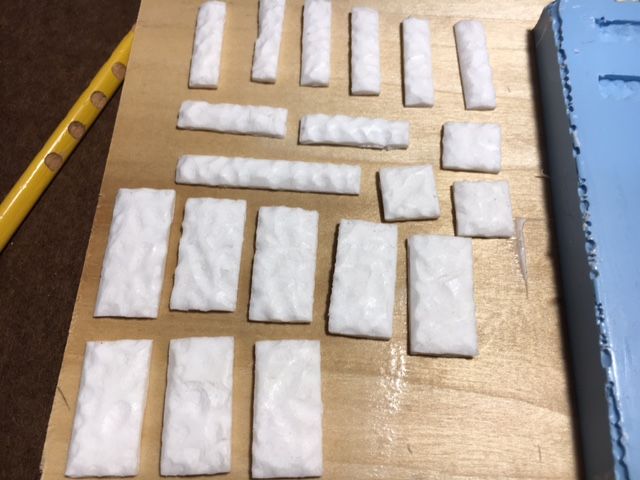
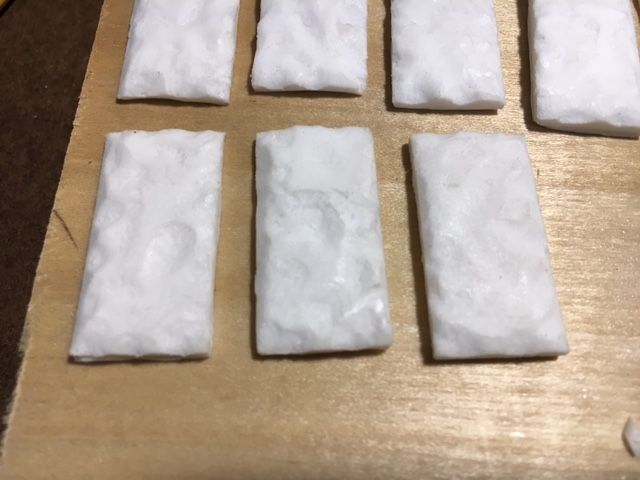
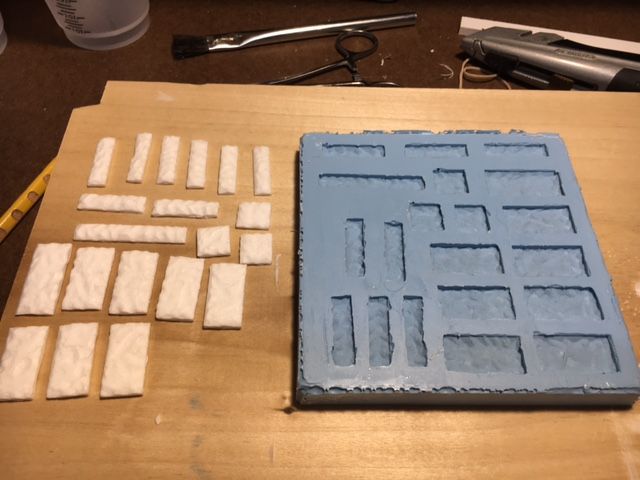
All in all, I am pleased with the outcome. I still have to make quite a few more stones to have enough, but that is just a matter of time now. I am already thinking of other ways to utilize this new found skill. Again, thanks to all of you who have posted information here on the resin casting process. It has helped immensely.