Not sure where I was going with my last post, but it was a work travel half-week and those always leave me in a half la-la state. Which would be a full “la,” come to think of it. Anyway, yay, back home now, and I got a half day yesterday and most of today to work on this.
The big deal yesterday was getting the brake line piping in, which involved bending, soldering and epoxying. After that I was able to bolt up the underside mast base. This pic gives an idea of how many screws were needed.
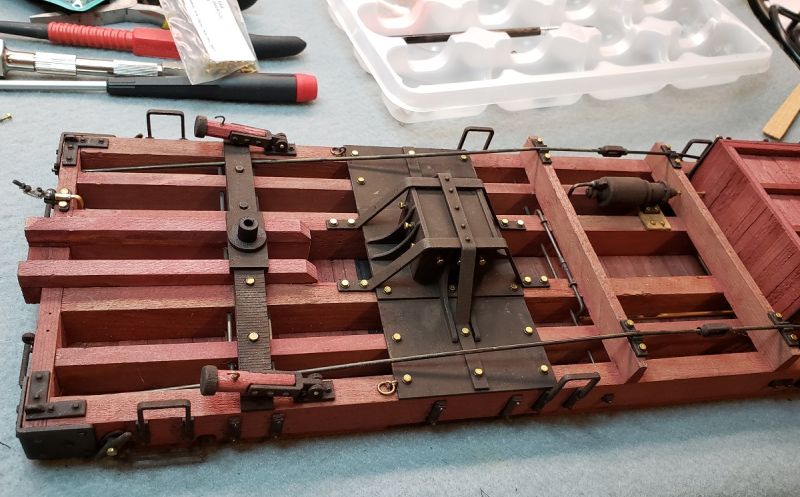
I wanted to post the above pic before it all got blackened. I like the shiny bits, so it’s always a bit of a downer when blackening. Whatever; that’s what therapy’s for. And here’s the underside, all finished.

BTW, I had a nice bit of success with the u-bolts that secure the transverse piping as it crosses the sills. First, I held the pipe against the beam and pin-vise-drilled a 1/32" hole on either side. Then I bent a bit of #22 solid copper wire (without insulation) around a piece of 1/16" rod, with legs ~1/4" long. I tapped this into the holes with a jeweler’s hammer, and it’s nice and secure.
The below pic also shows the mast’s jacking bolts, 3 on each side.
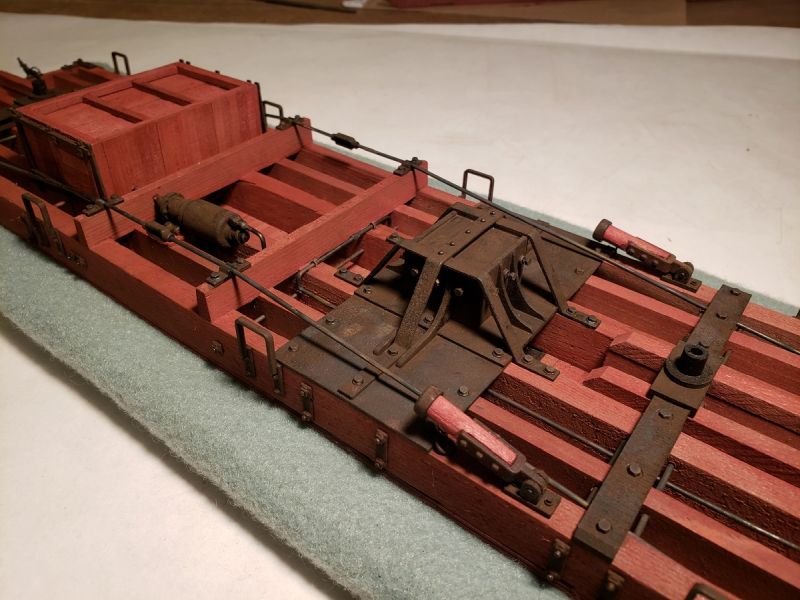
This derrick had 4 rigging rings at each end, and here they are. Lots of cleanup to do, man, these hi-res shots are far better than my eyesight! I’m reminded why I complained about my CA skills last week… I’m considering fixing the gloobers with a scalpel and more stain. Or by just not including closeups in my October presentation. (https://www.largescalecentral.com/externals/tinymce/plugins/emoticons/img/smiley-foot-in-mouth.gif)
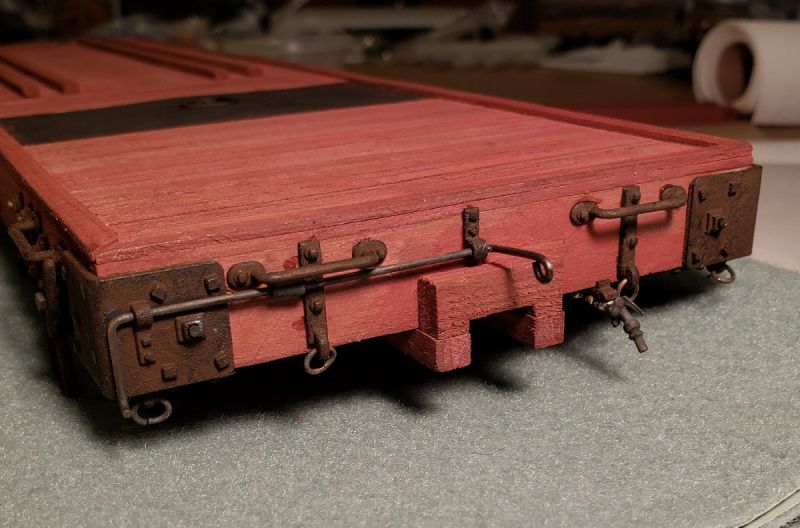
So the car body assembly is done, and now I’m moving into the derrick itself. With the boom’s wood being assembled (via jig) already, I began with installing the 3d printed base yoke casting. And I was pleased & surprised to see that the fit was perfect, in spite of the compound angle. The jig-drilled holes lined up with the 3dp holes on the base yoke and the head casting, and the winch frames fitted up with minimal filing. So after being ready for catastrophe, I was really thrilled.
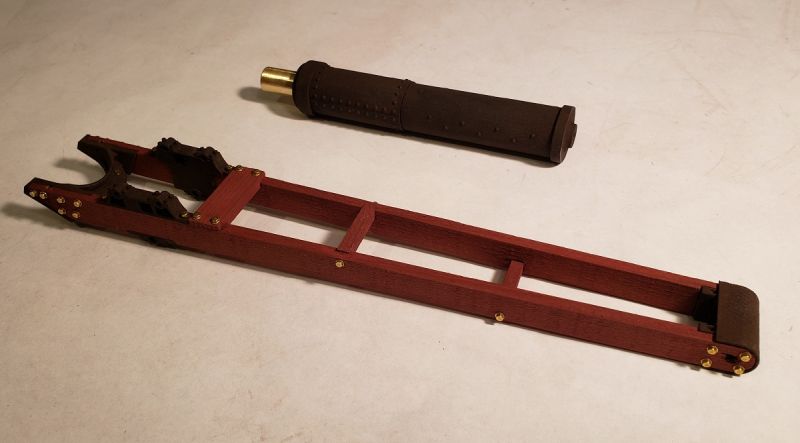
Lots more to do on the winch and rigging, and then come the five trucks.
Thanks for hanging with me on this,
===>Cliffy