Forgive me for hijacking my own thread; but I love to learn and Jim asked about the fiddly bits on these boilers/hoists. Admittedly I am only somewhat familiar with these iron beasts and how they function. As I do in all my modeling I use it as a lesson on understanding what it is I am trying to replicate. I could simply glue the fiddly bits in the area that I see them and call it good. But what the fun in that, I would rather know what the fiddly bits do. So to that end and to help myself, Jim, and anyone else i am going to use my MIK build as a tutorial on not only building one but understanding what it is we are building. So for those who already know, feel free to correct me, add to it, or simply ignore it. So here it goes, the heart of the beast, the boiler.
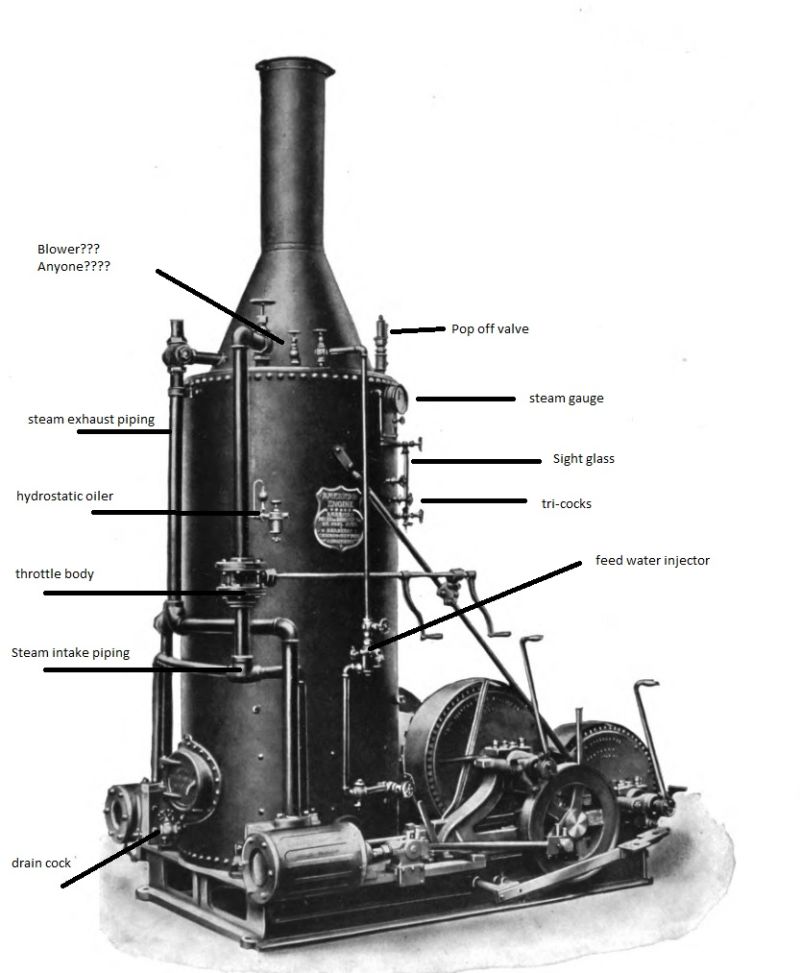
A boiler is a relatively simple thing and it makes no difference if it is a locomotive, a tractor, a ship, a crane, or a steam donkey; the boiler is a boiler. It consists of a fire box, a water/steam tank, and a smoke box. In our example here the fire box sits on the bottom and as the name implies is where the fire is built to heat the boiler. The boiler itself is a tank that holds the water and steam. It has a series of tubes running through it that heat and gas/smoke move through on their way to the smoke box and eventually out the stack/chimney. As the heated gas/smoke moves through these tubes it heats the surrounding water to the boiling point creating steam. There are a great many tubes as this increases surface area and contact with the surrounding water. That’s boiler basics 101. The steam produced is then used for various things, the main one in our case is to drive a piston to create motion. In this little post I will do my best to explain what each of the pieces on the boiler are so that we can know what we are modeling.
Starting at the top. The thing I have labeled blower, I am not actually sure if this is what it is or not, acts like a turbo charger. If this is what I think it is, and they do use them extensively on locomotives, the fire is increased with draft. On a fire place we open and close dampers to create draft. In a boiler this is accomplished by air entering the fire box and then being sucked out the stack. To give this a little (well a lot actually) boost exhaust steam is ejected through the smoke box and out the stack. As the steam rushes out the stack it acts like a venturi sucking air/smoke through the fire box, through the fire tubes and out the stack. This really increases the draft and fans the fire. Under operation this is done with the exhaust from the steam chests being dumped into the smoke box instead of just out to atmosphere. When the engine is not being used, i.e. when the throttle is closed and no steam is going to the chest, there is a blower that takes steam of the top of the boiler and injects it into the stack thus doing the same thing, turbo charging the draft. Now in this drawing I can only guess that is what that fiddly bit is I am pointing too.
Pop off valve- a valve set at a predetermined pressure setting that opens automatically at the set pressure allowing steam to escape so as to prevent over pressurization and an explosion. Locomotives a lot of times have two set at different pressures as a double safety. If you want a real example go look at your hot water tank and at the top there is a brass cylinder plumbed in. Guess what that is. BTW when that thing is leaking, please don’t be an idiot and take it off and plug it, yes people really do do this.
Steam gauge- tells you the boiler pressure.
Tri-cocks/sight glass- we discussed that above already.
Feed water injector (my name not the technical name)/ lifting injector- This is used to put water from a tank into the boiler while the boiler is under pressure. Water in the tank/tender is non pressurized. The water in a boiler under operation is under pressure. Physics dictates that substances under pressure seek to be under lower pressure. So if we were to just open a feed water valve the steam/water under pressure would head to the lower pressure of the tank/tender. So how do you overcome the pressure differential and defy physics and put lower pressure water into a higher pressure vessel. Some dude way smarter than me created the lifting injector. High pressure steam is passed through a venturi to the smoke box creating an even higher pressure zone by the accelerated steam. This venturi creates a suction, that suction is then attached to a hose/pipe that is attached to our tank. The pressure at the venturi is greater than that of the operating pressure of the boiler. So the water in the tank (well only at the point of the venturi) is greater than that of the boiler and therefore the new water wants to go to the point of lower pressure which is the boiler. Its rather simple really until you actually try and understand the physics of a venturi. But I have no intention of tackling that one. For modeling purposes you have a pipe from the lower boiler area to the injector and through the injector to the top (empty part) of the boiler. another pipe/hose is connected to the side of the injector that runs to the tank. Valves are located at the intake and the outlet for isolating the thing and another valve is located at the high pressure side which is used to turn the injector on and off and controls the feed rate.
Intake plumbing to the steam chests- steam is taken off the boiler and is fed to the steam chest providing the steam to drive the cylinder piston.
Exhaust plumbing- takes steam off the cylinder on the exhaust stroke and send it to the smoke box to drive the turbo effect mentioned earlier.
In modeling both the above pay attention to where each pipe is going. The intake is coming of the top of the boiler and goes to the steam chest. The exhaust comes off the cylinder and goes to the smoke box.
Throttle body/valve- a valve is placed on the intake plumbing to regulate the amount of steam allowed to be delivered to the steam chest. On a locomotive this is done inside the steam dome and has a rod that passes, in general, to the backhead where there is a lever that the engineer operates. On our derrick engine it is a valve operated by a handle that somewhere in the middle of the intake pipe. Turning the handle opens and closes the valve. Some have two handles as shown in this picture and I don’t understand why, anyone?
Hydro-static oiler- Also in this picture you see a hydro-static oiler. Not a 100% sure why this is there other than it has to be an added feature used for oiling various pieces of machinery automatically through connected lines. The picture shows no such lines. But they maybe passing through the boiler to heat up the oil to make it flow easier and is thus out of sight. This is how it is done on many locomotives. Steam is used to pressurize the oiler. Again by venturi, oil is sucked out of a reservoir (teardrop looking globe on top) and pushed to where it needs to go. Somehow though the oil and steam are not mixed. I can’t say as I know exactly how the steam creates a pressure and then transfers the pressure to the oil without the two mixing. I am guessing some sort of diaphragm. On a loco this was a gigantic help. Do you know why on the sides of locos you have walkways, well there are many reasons, but in the first days one of the reasons was so the brakeman could walk out and put oil in the oil cups on the steam chests while the locomotive was moving. The Hydro static oiler , took thick oil and ran it between the boiler and the boiler jacket to heat up the oil making it flow better and then dumped it into the oilers on the steam chest. No more need to manually oil the cylinders. I have always said “necessity is the mother of invention, but laziness is the father of efficiency.”
Finally the drain cock- at the bottom is a pretty self-explanatory piece of plumbing. It is simply a drain to drain the water when not under pressure for maintenance on the boiler.
So there you have it. The anatomy of a boiler inbthe most simplistic fashion as I could make it.