Some work on reefer 39.
When it was sold off, almost all the fixings under the car were removed so that it could be sat on some pilings to be used for storage. We have been scrounging parts to put it all back together. We got some off the Mountain, and others we are having to make.
Nothing much left under the car. This shows where the Needle Beam should be. There are scars that show its exact location.

Note that the thru bolts that hold it to the 6 beams, have been touched off. we will have to get these out to make way for the new ones.

After measuring from a set point, back and forth, and a good dose of SWAG, Dennis D. Drills an 1 1/2 hole thru the floor from the inside hoping to expose the top of the thru bolts that hold the Needle beam on. Some holes we are luckier then others.
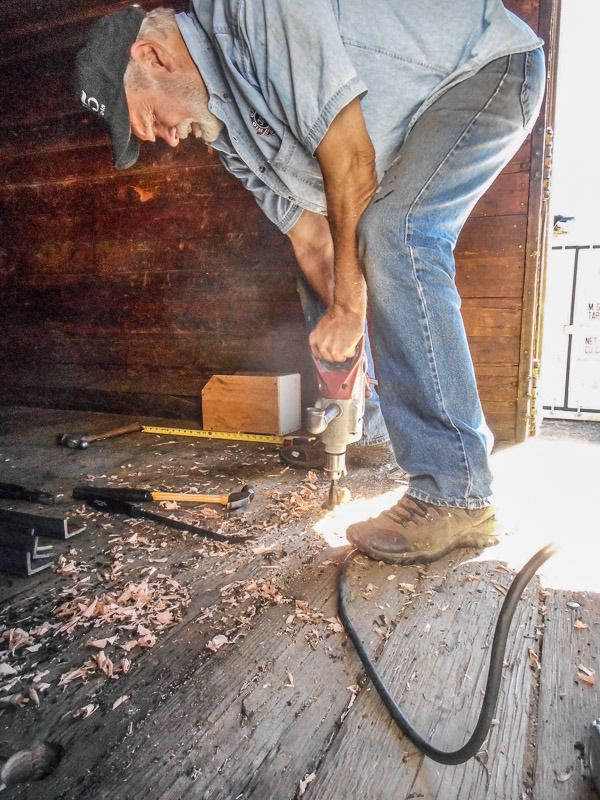

The floor is made up of 2 inch thick ship lapped fir, with a water barrier ( tar paper ) under that, on top of about 1 1/2 inches of cork insulation. This car as originally built had the angled Needle beams, and as such, the thru bolts were angled to match the beam, when it went thru it’s shopping, the angled Needle beams were replaced with the conventional vertical beams. This proved to finding the exact location of the thru bolts difficult. Some holes needed a good work over with a chisel to get the cut off bolt driven out.
One of the new Needle beams jacked up in place.
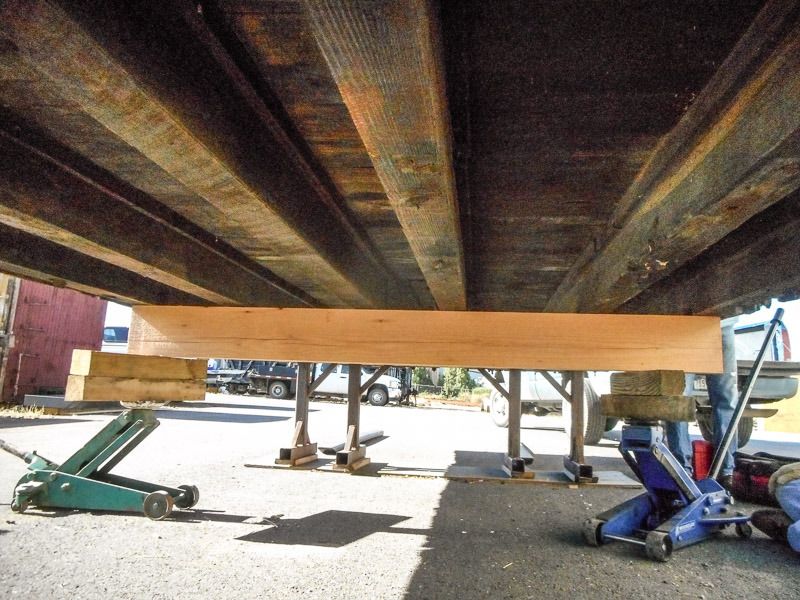
They were carefully aligned and put in registration where the originals showed that they belonged.
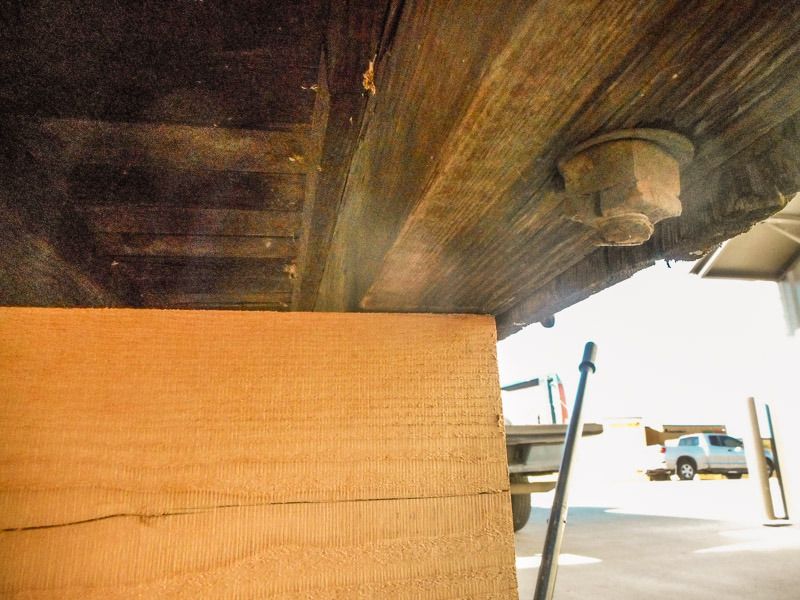
Each contact point to the main beams were marked, and referenced so that each beam went in only one orientation.
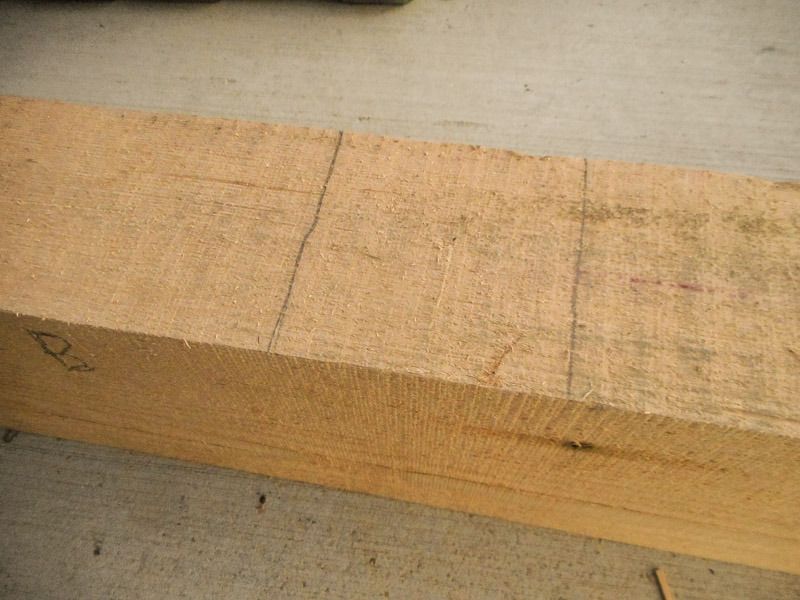
I then set out to notch where each beam contacted the Needle. 3/8 deep notches were used to help stabilize the sills in the center of the cars, and also to prevent twisting and warping. First off, using blue tape as a depth guide on a hand saw, I cut both sides of the notch to match the sill locations.
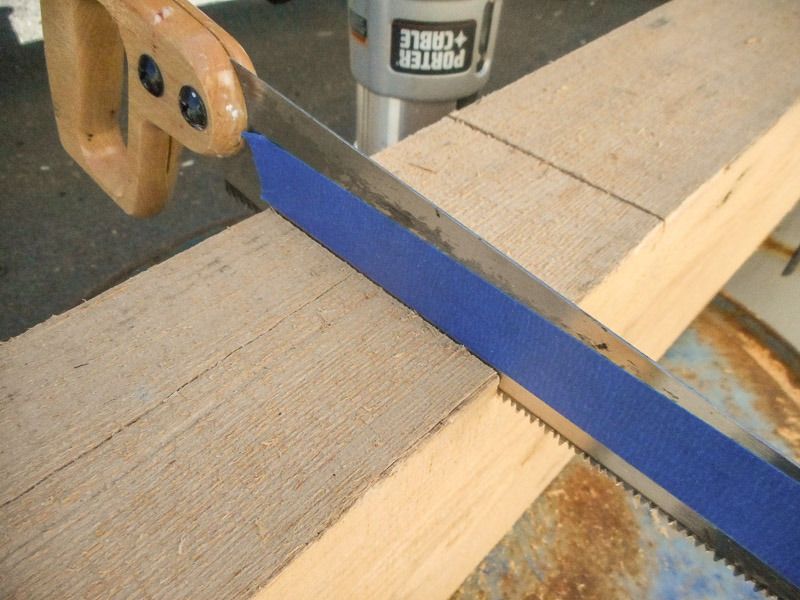
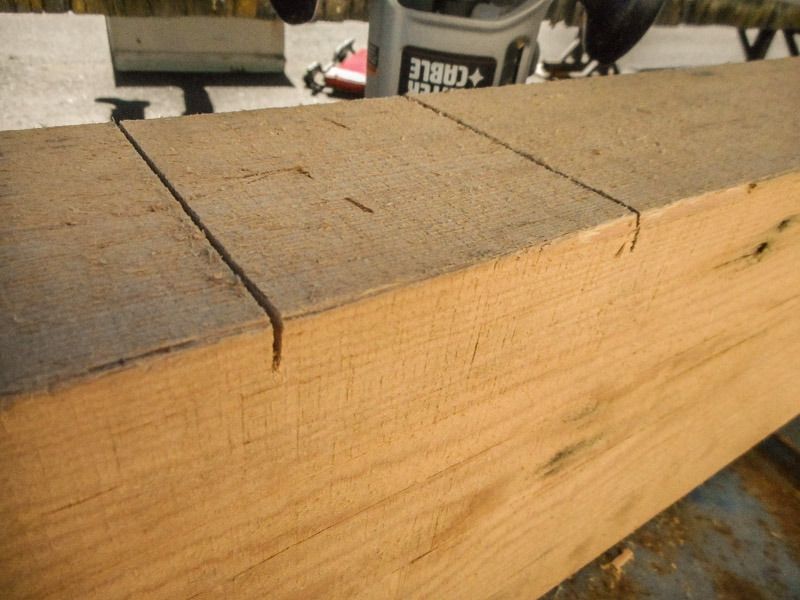
Then a guide board was placed to aid in using the router to remove the waste.

With the router and a straight bit set to 3/8 deep the waste was removed between the cuts.
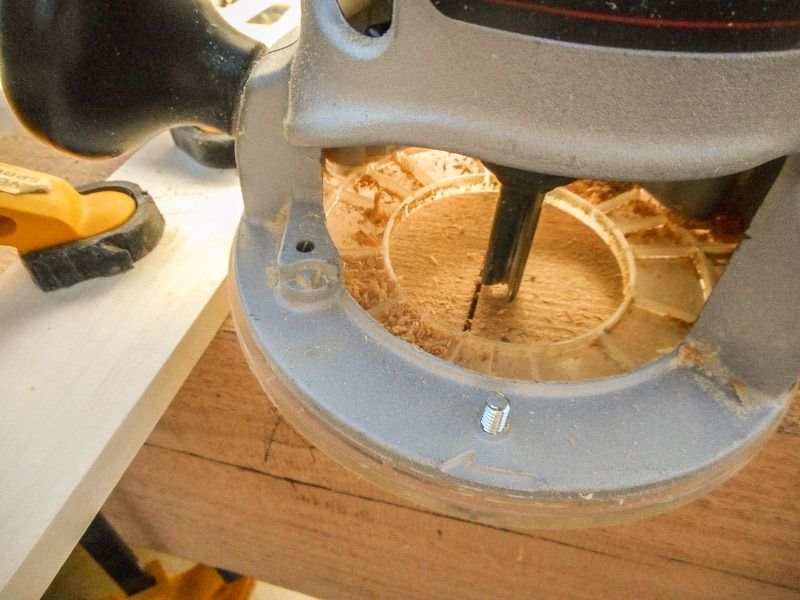
All that was left to do then was to clean up the notch with a sharp hand chisel.
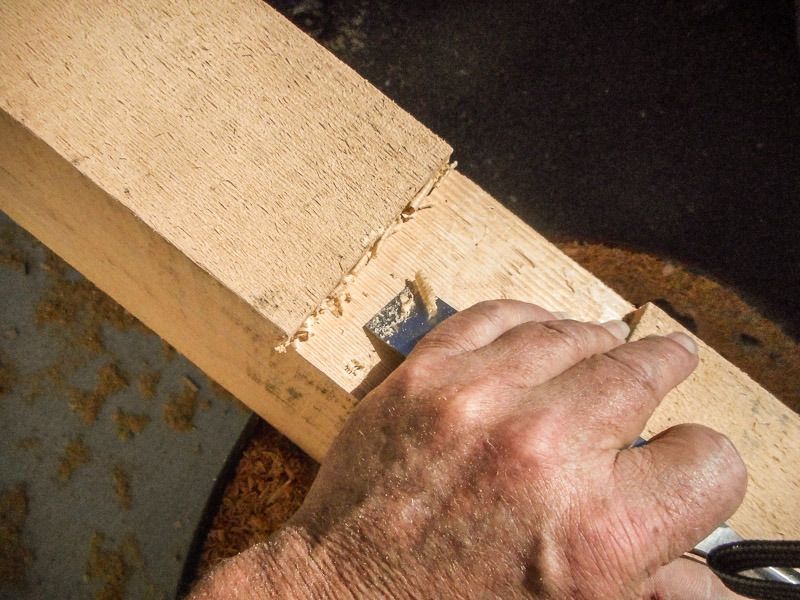
The beam fit perfectly. The bolt holes were marked from above, and will be drilled thru with a drill press for accuracy, at Dennis D. shop.
And thats how we make a new Needle Beam. Stay tuned, more to come.