Well thanks to a friend in our local club who is an excellent resource for turn of the century RR and logging in our area, he is an author and has written several books on the subject, I am taking several steps back on this steam donkey. I admittedly didn’t really understand how they operate. And I was more or less winging it to make something that looked plausible. But I never really was comfortable with that as I usually like to understand what it is I am trying to make.
Right off, Mike printed a few of the parts to start doing test fits. And the thing is gigantic. Without anything to scale against I really had no idea how large of a donkey I was making. So we have shifted gears and this will become a cable yarder (highline/skyline skidder) with a big boom off the front that could double as a loader. Something like this
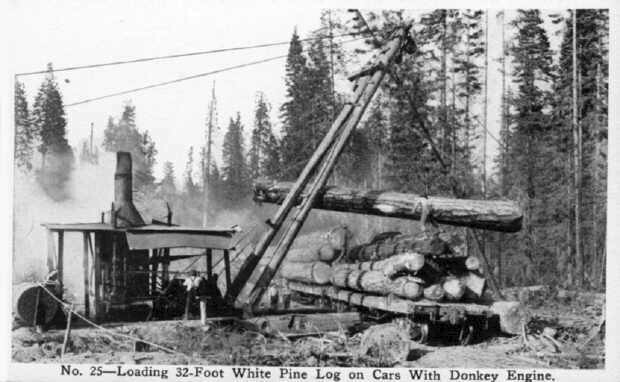
Image Courtesy of Trainweb.org
My friend Dennis provided me some nice line drawings of a double and triple drum version of a similar size donkey. I am going to keep it a double drum for the main drums but add what the drawing calls a “straw” drum or what I call a capstan winch of the side of the lower drum. According to him among other things the straw winch was used to move the steam donkey around. Also the top drum and lower drum in the drawings are not the same size diameter. I needed to extend the drive shaft clear across and add the pinion gear so by making the upper drum smaller I will be able to add that detail.