It’s been a couple of weeks since I posted some photos of my 7.5 inch gauge turnout build and it took me a while to catch up on the photos I’ve taken of the build since the middle of April. One thing I discovered as I started to do the assembly of the various components was that each piece has to be EXACTLY and precisely machined and fitted, otherwise the switch just plain won’t go together :)! I actually had to tweak both the radius on the main curved stock rail and the curved closure rail. I found I had the radius fairly close, but not close enough for all the geometry to work and fall into place. The outside main curved stock rail is called out on the print to be 384 inches or 32 feet. The arc height on a 36 inch long chord is 0.422 inches. The first time I put the bend in this rail, it came out to about 0.460 inches. A little sharo, but when I started to assemble the straight and curved stock rails, then the point position of the intersecting lines on the frog were wrong> Print calls for 76 inches from the point ends to the points on the frog. By re-bending to a bigger radius (0.422 in 36 inches, all of a sudden the points were exactly 76 inches and the entire remainder of the turnout all fell into place! I also discovered that as large as this code 1000 rail is, it DOES flex quite a bit. So when I checked the chord, I wanted the rail to bve in a “relaxed state” and no flexing to get the correct dimension :)!
The series of photos below, show the various “fitting templates” and gages I machined, to check track gauge, chord length and arc height. These are positioned in “station points” or positions along the turnout. All the dimensions are based on the distance from the end of the switch points. Also the fitting templates establish the relationships between the curved closure rail and the straight closure rail and their relationship to the main stock rails.
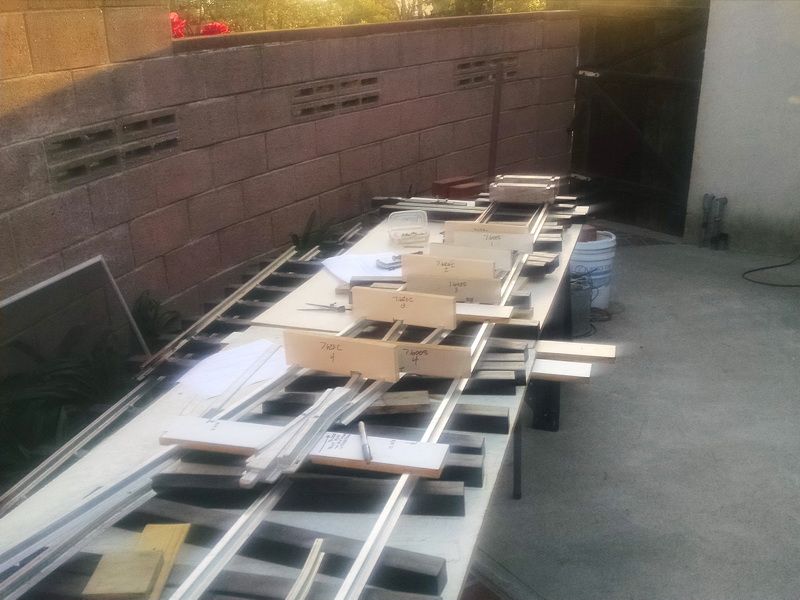
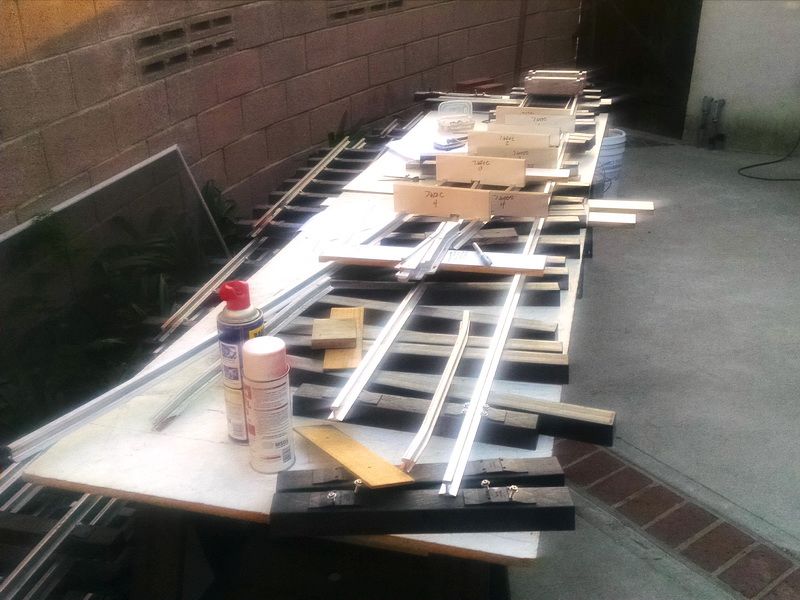
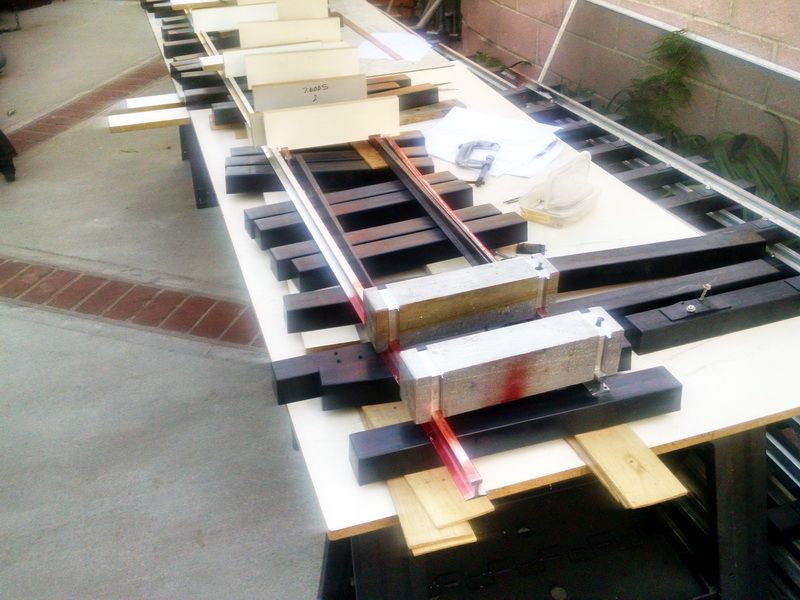
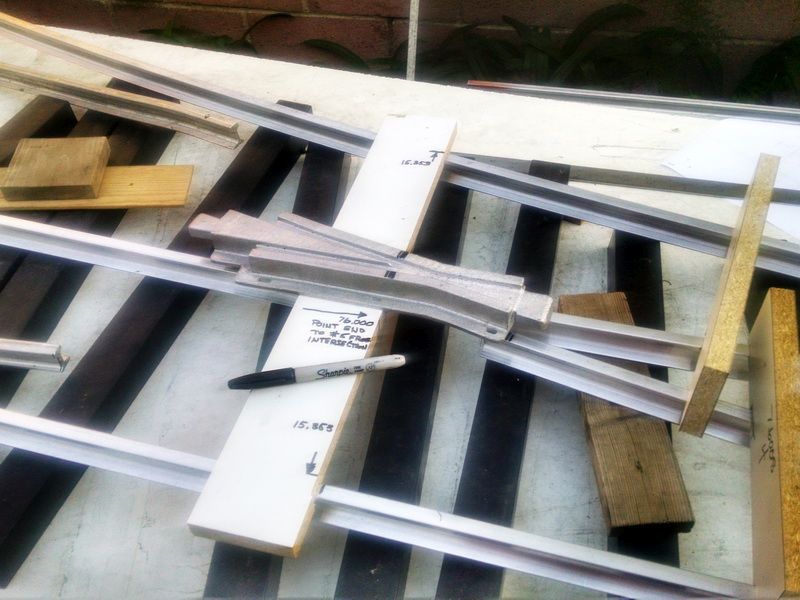
As you can see in this photo, the edge of the fitting template establishes the relationship of the main straight stock rail and the main curved stock rail AND the position of the cast aluminum frog and the ends of the curved and straight closure rails. Everything checks :).
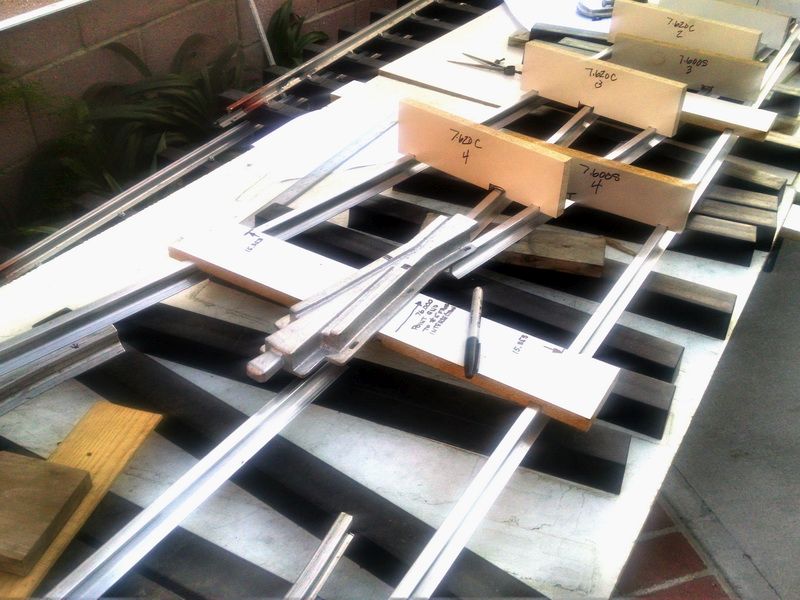
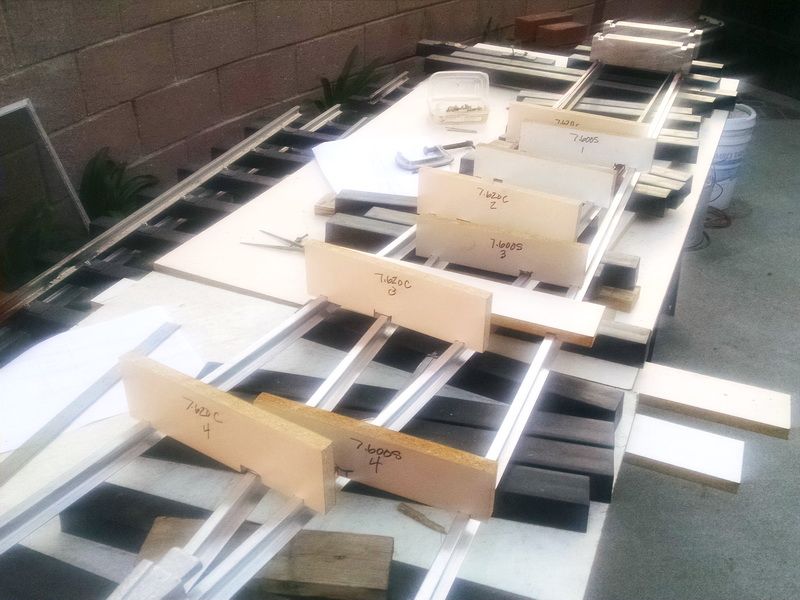
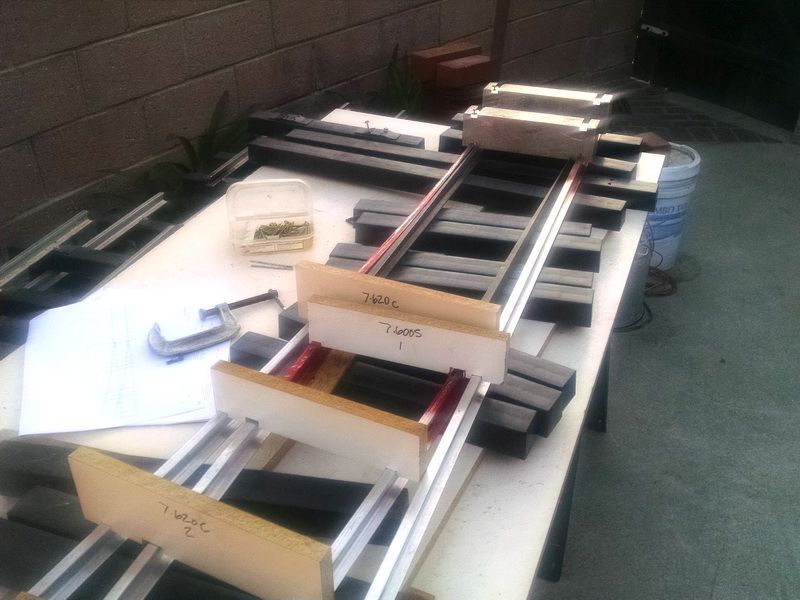
You can see in this last photo that the assemled switch points fit the notch in the curved stock rail very nice.