This thread is just about caught up to “today’s build”…
For the past couple of months, my son and I have been experimenting on various ways to rivet these cabs together. Many years ago, I hand riveted the tender for my 1-1/2 inch live steam ten wheeler. That tender had about 1100 3/32 diameter copper rivets. This was back in the middle 1980’s. I was a lot younger and had a little more energy that I have today. Tender took about a week or two to complete and that was the first rivet job I had done.
We asked around the hobby and got as many opinions as there are people in the hobby! Hand rivet…rivet with a pneumatic riveter…use steel rivets, less damage to the rivet head…copper rivets, easier to mash the backside stem…
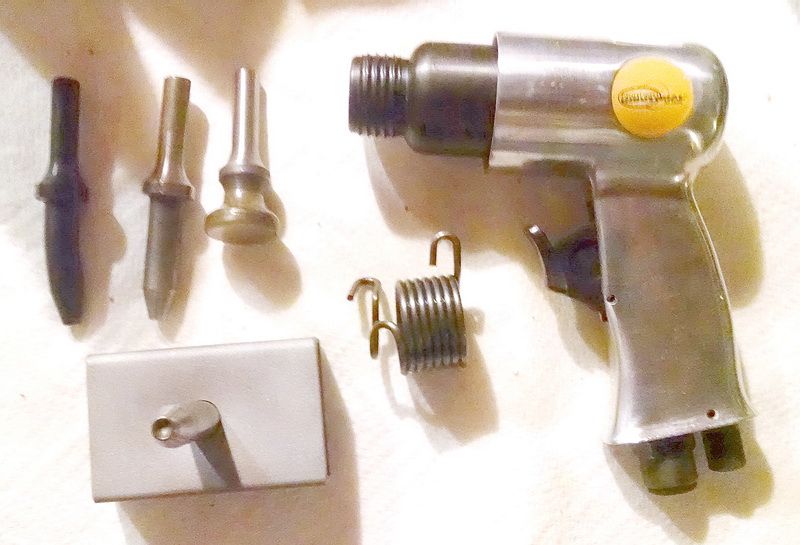
We purchased this rivet gun and punches and the rivet “buck” (tool at the lower left hand corner of this photo with the dimple for the rivet head) from a vendor who does rivet tenders for the hobby as his business. He recommended using steel rivets and using the “buck” on the head of the rivet rather than the “usual” way of using the buck on the tail of the rivet. We tried this on some sample steel rivets he sent. To mash the tail of these rivets, we had to set the pressure on the gun at a fairly high point. We DID mark the heads of the rivets and the mashing of the tail wasn’t consistent. We went to Hanson Rivet Company (well-known name in aircraft riveting) here in Pacoima, CA and talked to the guys in tech support on how best to do this job. Their recommendation was to use copper rivets only and get the proper lengths of rivets. 1/16th inch longer than the total of the pieces being riveted together. This was the best tip we got out of this discussion. Made all the difference in the world! Next they recommended we use a simple hand riveter to do the job. Easier to set the rivet and greater control over the mashing of the tail of the rivet.
This is the rivet set we used…my old one from back in the eighties!
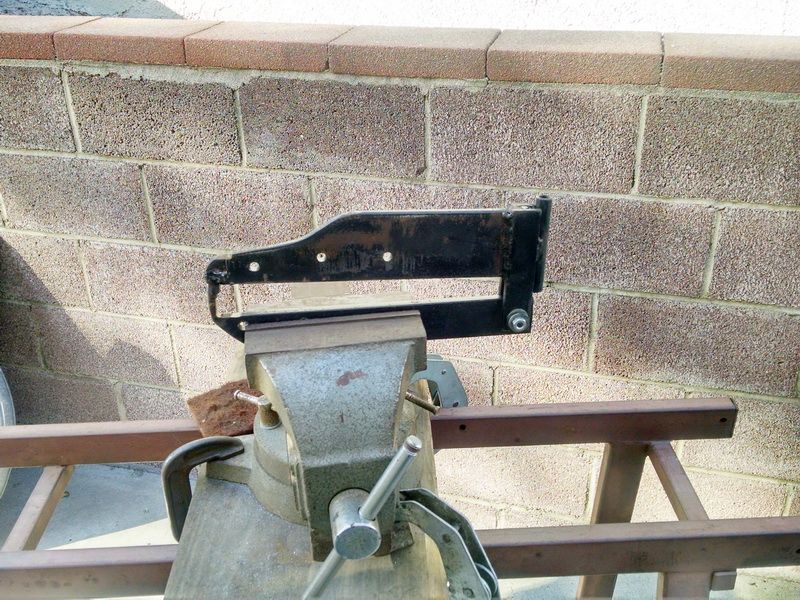
Pretty simple actually. The buck side for the head of the rivet is on the bottom. The top arm does the mashing of the tail of the rivet.
This is the tender I did the rivets on using this device.
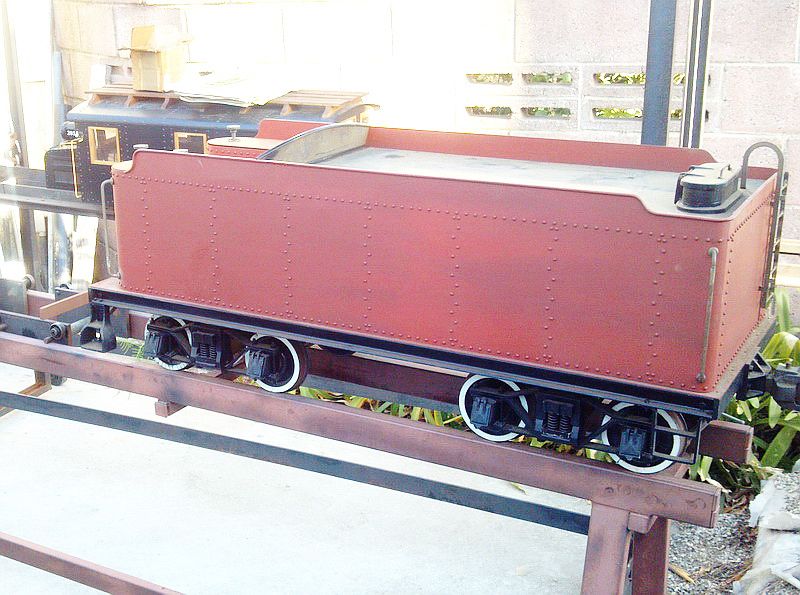
Riveting the hoods.
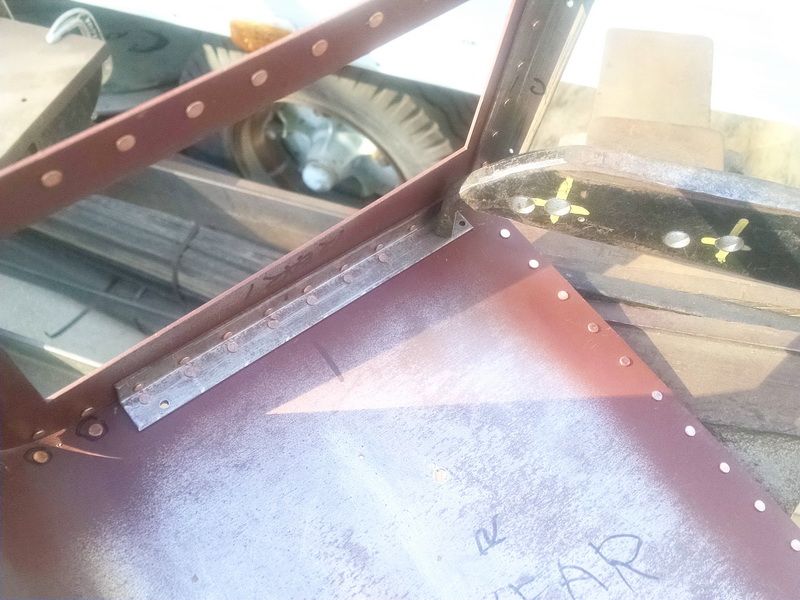
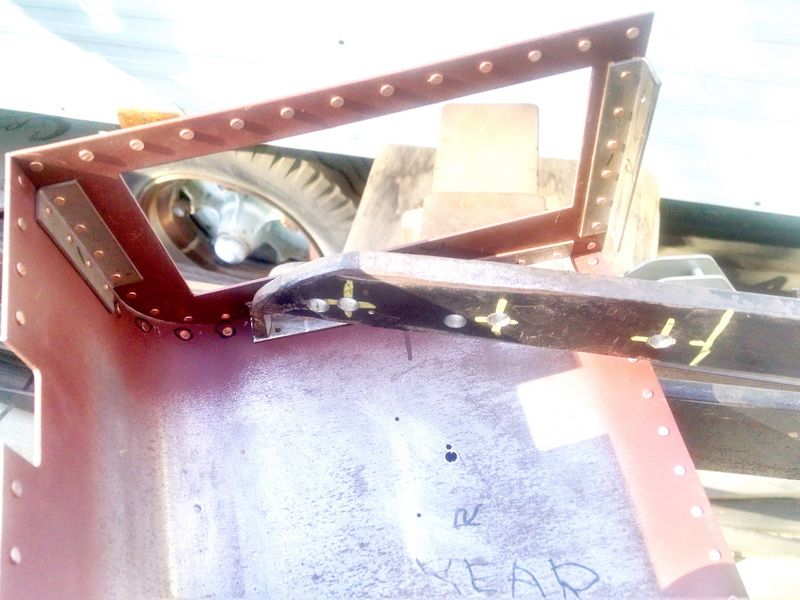
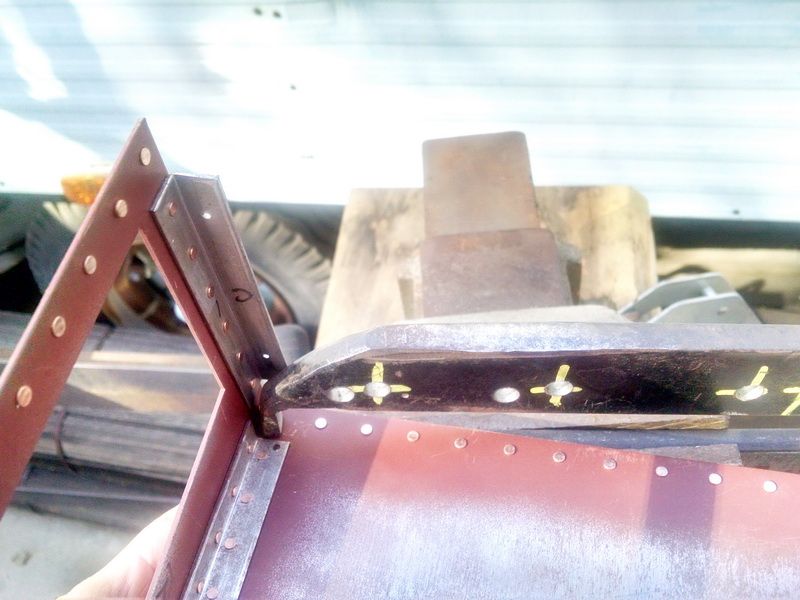
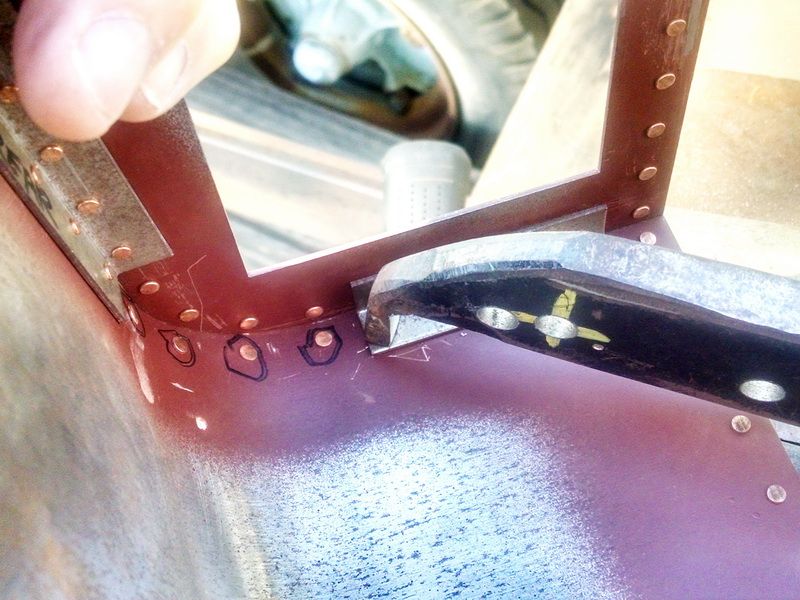
Before we could rivet the hoods together, we had to do the single thickness rivets on the radius of the hood first…we would not be able to rivet these in place once it was assembled. You always have to think ahead so you don’t “paint yourself into a corner”.
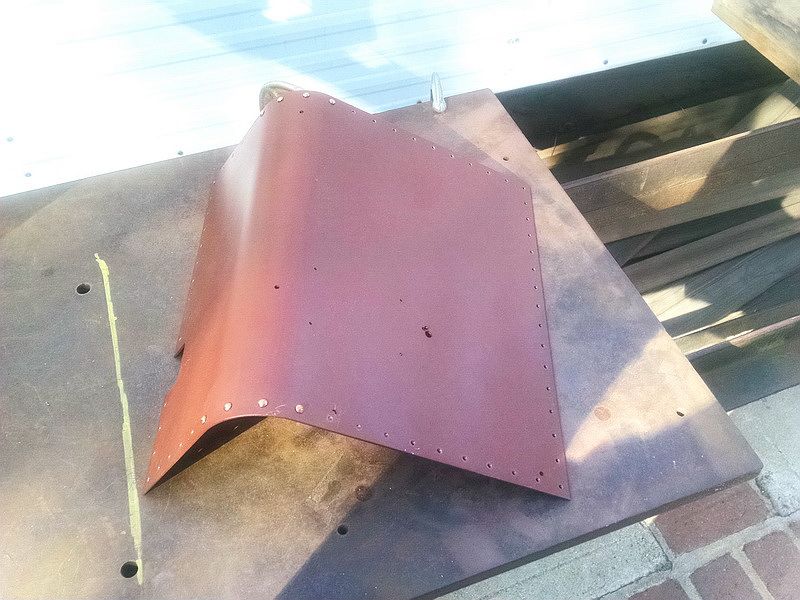
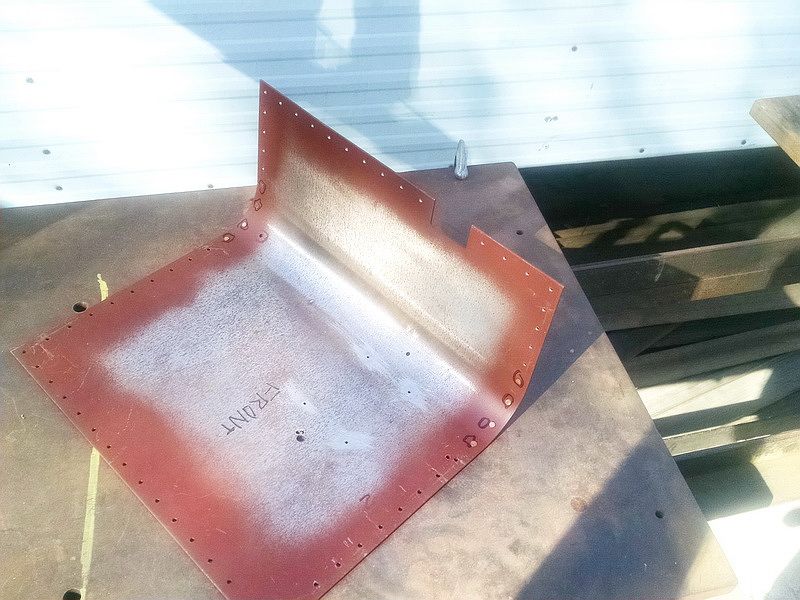
We primered the areas that had rivets in place to prevent rust forming between joints.
Completed hood. Ready for sanding and prep for finish paint.
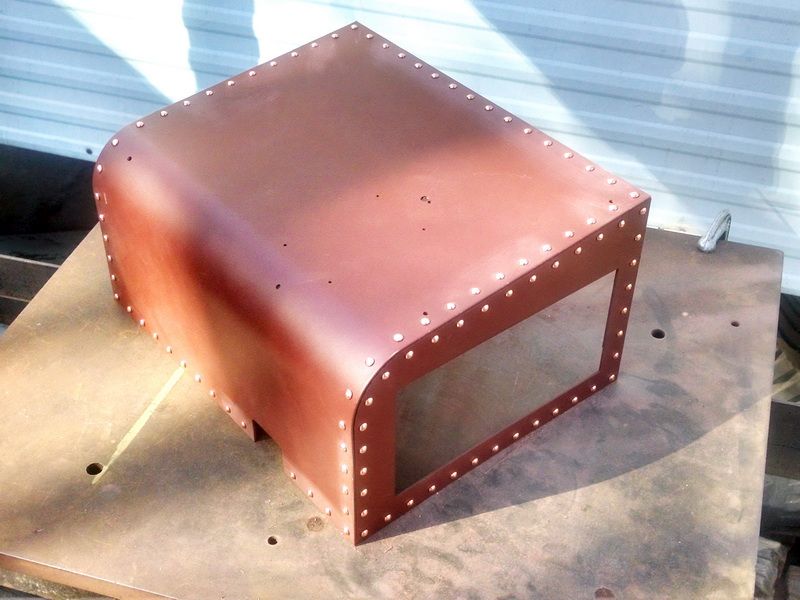
Finish riveted cab end.
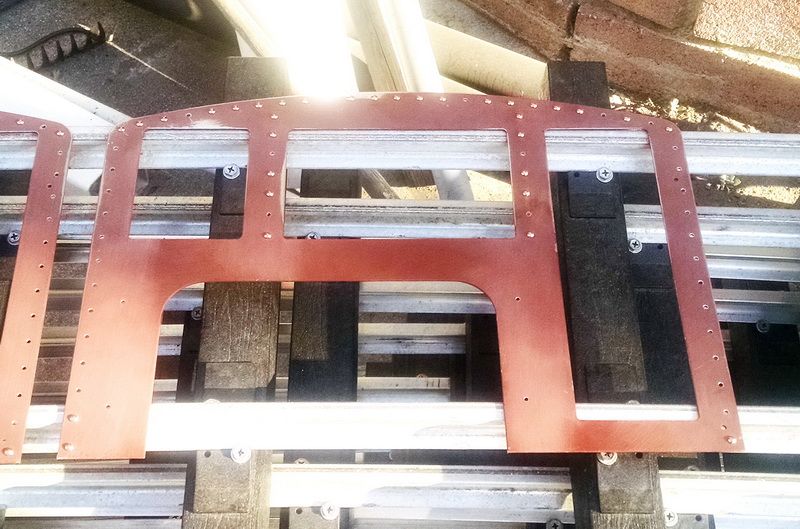
Finish riveted cab side.
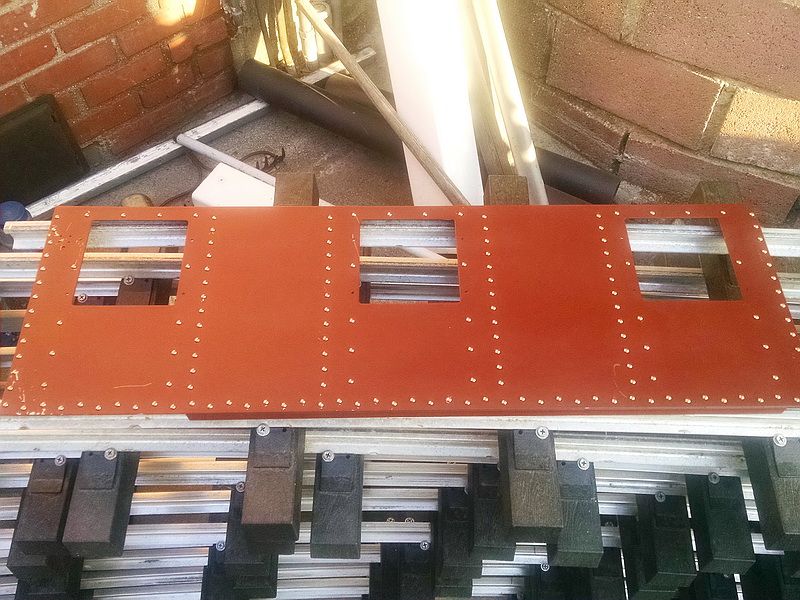
Cab sides and ends assembled to verify all the rivet holes line up. The entire cab was assembled and held with clecos to make sure the rivet holes all lined up. Take note that the holes on the sides and ends are not symmetrical. Left and right hand corner pieces. Had to be careful in these corner areas.
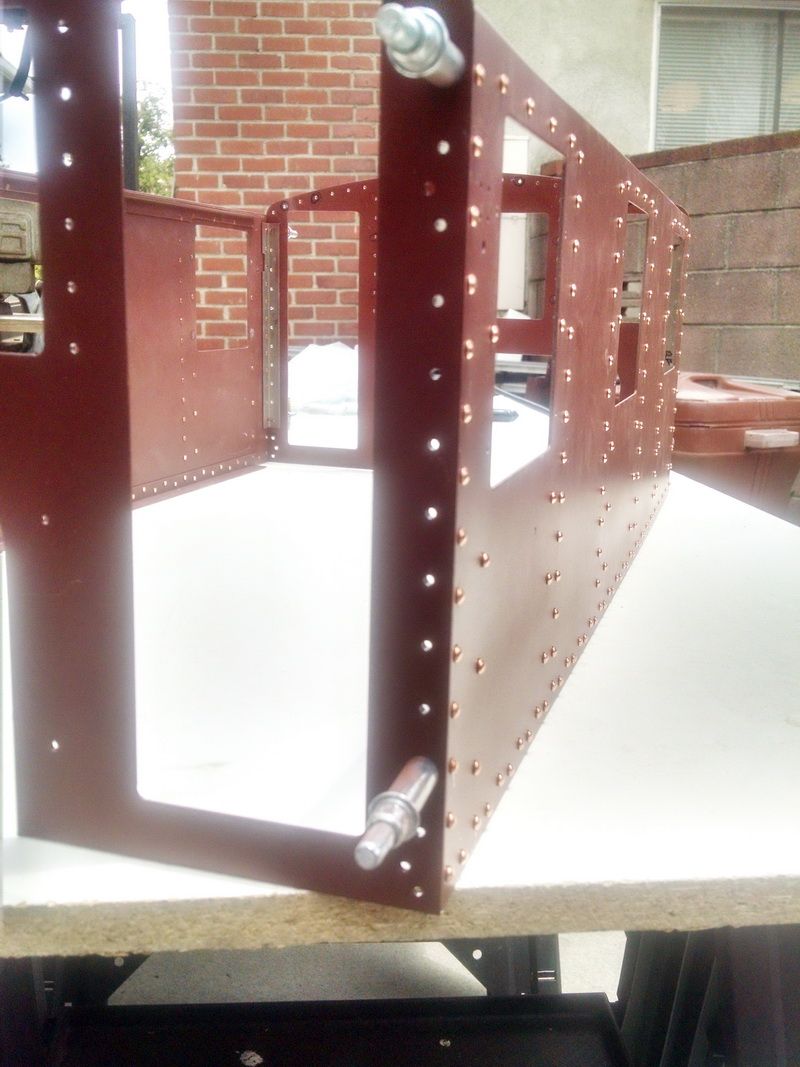
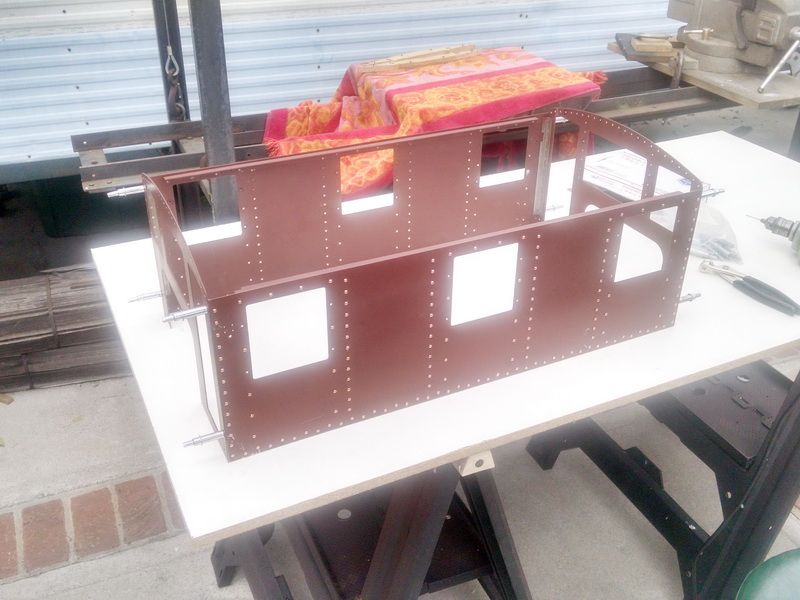
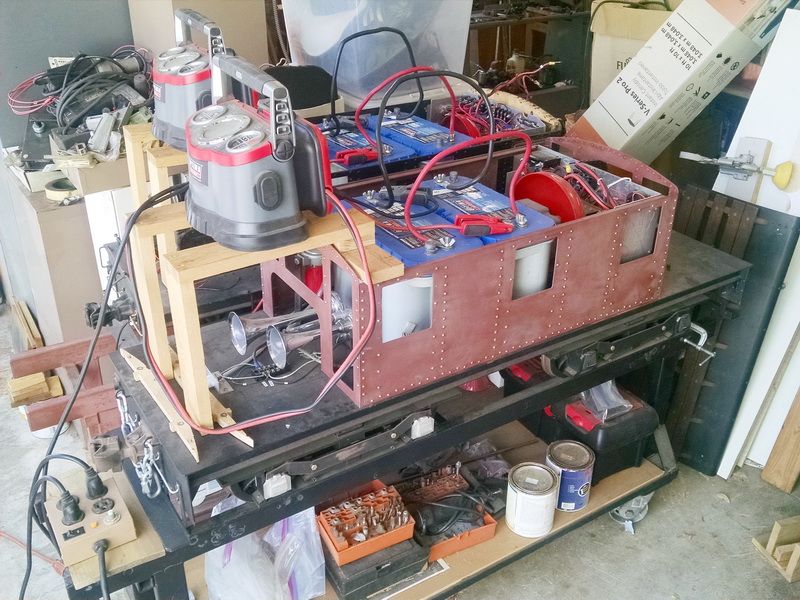
Riveting the roof of this engine had its own “issues”. The arm on the riveting device wasn’t long enough to reach the center rivets of the roof! We HAD to come from the side. Because the roof has the typical “Baldwin Locomotive” curve, we had to tip the roof at various angles to get a nice flat “mash” on each rivet.
So back to the “drawing board”.
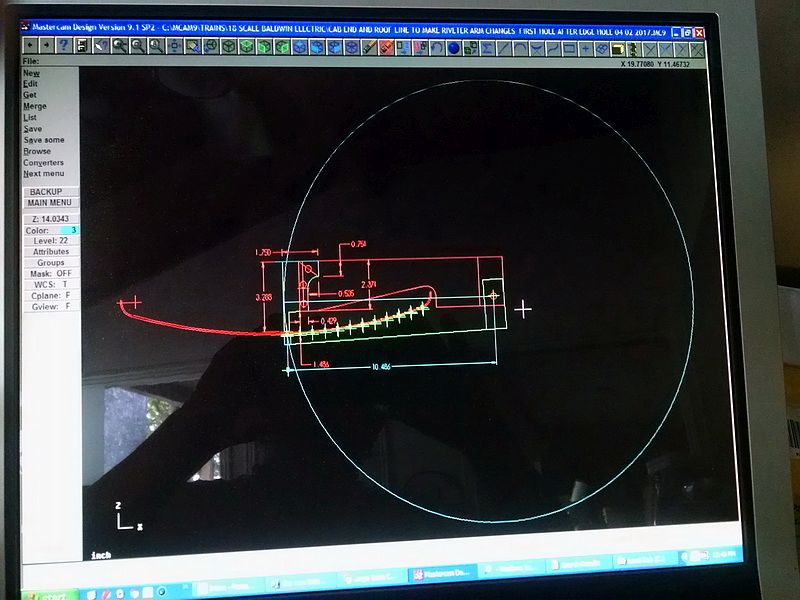
I machined a new arm for the riveter for the roof only.
The new arm is in front of the vice in this photo. We just remove the original arm and replace it with this new one. Note the clearance cut into this arm to clear the roof as it is tipped.
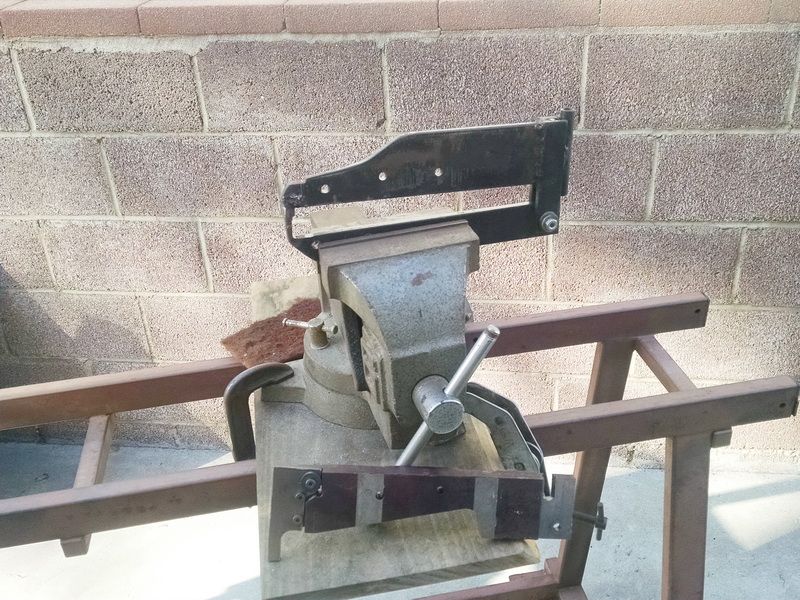
When these metal roof were rolled back in the middle nineties, they were done by CNC control rollers. But these machines were very crude in those days and left marks in the metal as it was rolled. I did a little “bench work” on these anf smoothed things out quite a bit.
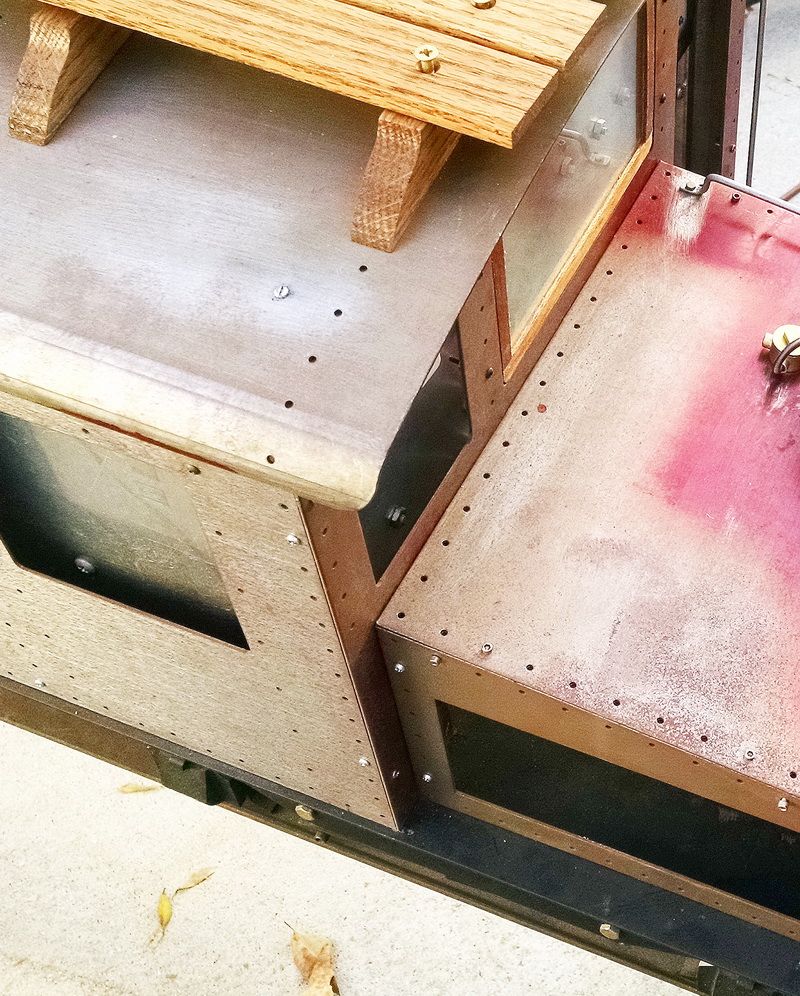
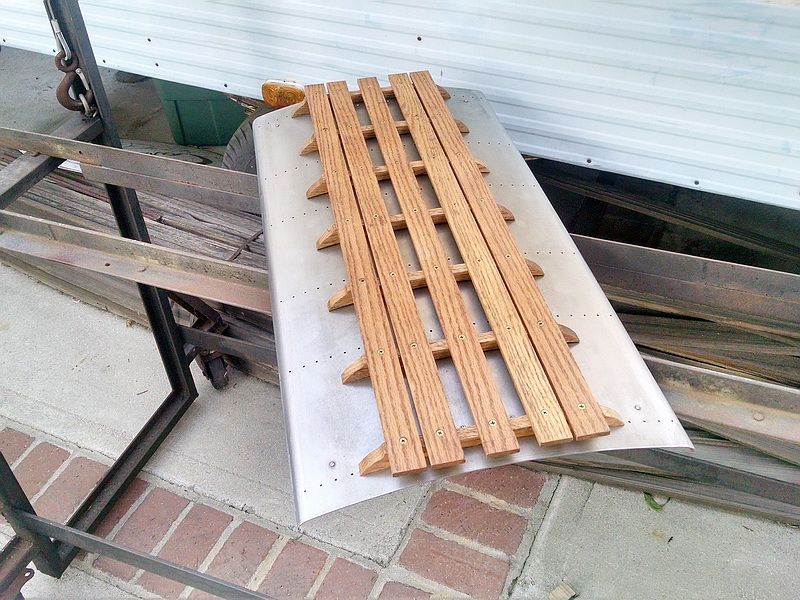
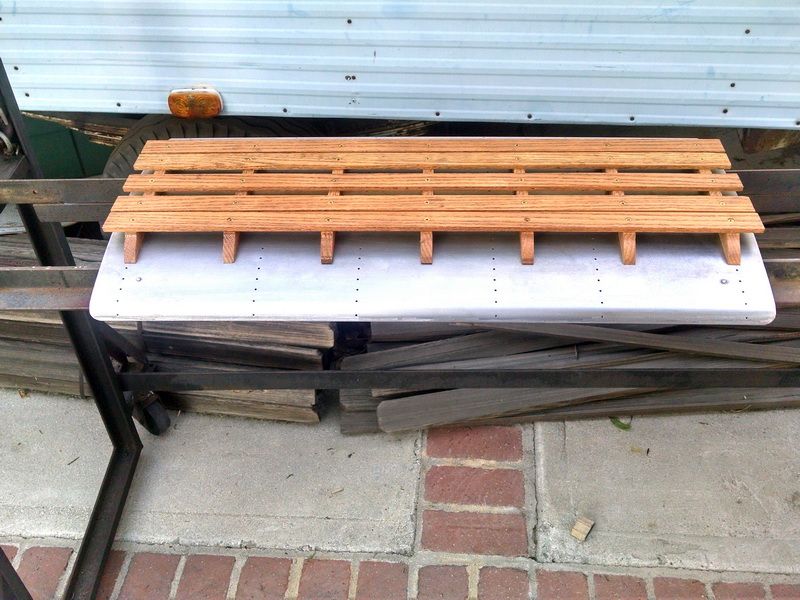
The so-called “marks” along the edge of this finished sanded roof is actually the reflection of our house in the background!
Finish riveted roof and in the process of final sanding for primer and finish coat.
.jpg)