Here’s some on the design & build plan.
Because of the quantity involved, in both linear feet of facade, and also doors & windows, I wanted a method where all the detail could be lasered in and just painted.
Acrylic can be fragile, if left unsupported (as with a facade). Lightly engraved details are possible, but not with depth (like mortar lines). Engraved lines also act as nice score lines for breaking in the wind.
So I’ve wanted to use foam board for the flats. Ain’t cheap; but tolerable, over time. I experimented a bit, and discussed with Dennis, to come up with a good set of numbers for cutting and engraving the material, and that thread can be found here.
Something I was hung up on in that thread’s beginning was wanting to use the laser to make larger depressed areas, say, for door and window jambs, to give some depth. Turned out that though this is certainly possible (say, 1/8" deep), it caused two problems. First, it took a long time (and the results were rough). Second, with only 1 layer of material, I was concerned about structural integrity. All that was solved by going with 2 layers of material, which gives a needed strength improvement, but also opportunity for recessing (by just removing the first foam layer).
The other things I cared about were:
- Remove individual buildings for repair
- Some (but not all) window details & lighting
- Ability to add in stages
- Some balcony & sign details
- Paintability, and avoiding the pretty huge costs of colored engravable acrylic for big areas
- Layering sheets to give some depth
The experimenting led me to the material decision of SignFoam 15 lb, 1/2", in 2 layers. A third layer could be used for smaller details, but the 2 base layers were the basis of area calcs and ordering.
About the foam board: though it looks like insulation board, it’s not; this is far higher density, and designed to be left outdoors indefinitely as a sign product. Cheaper brands are out there (e.g., Dura/Corafoam) which are less expensive, but flammable (I tested samples with a lighter, and they don’t want to go out). Only two brands are self-extinguishing and laserable, and don’t torch up during the lasering: Precision Board and SignFoam. I went with the latter, purely based on shipping & delivery (free, vs. ~ $250, with no local delivery).
I did almost all of the design work in 2D CAD, because of all those details of brick / boards / signs / etc. I’ve been pecking away on that for maybe 2 months here and there, for just this set of buildings… After the outlines were firmed up, I brought those into 3D CAD to design the more 3D-ish things.
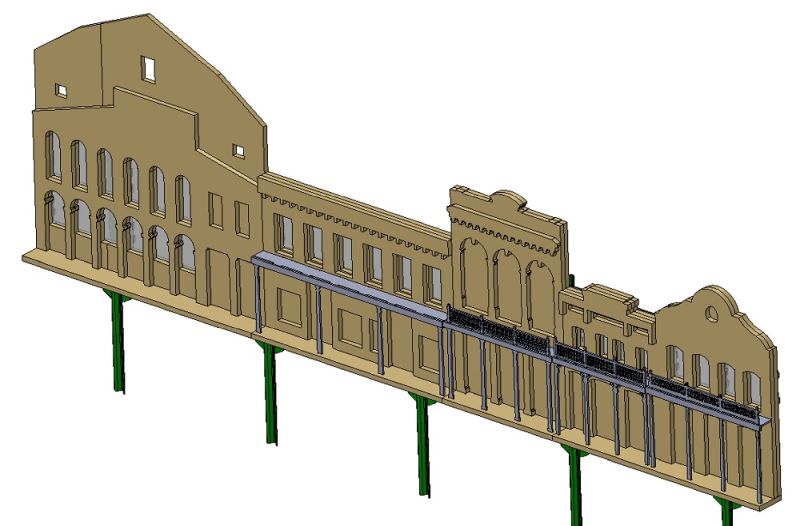
The gray areas are acrylic, and all the tan is foam.
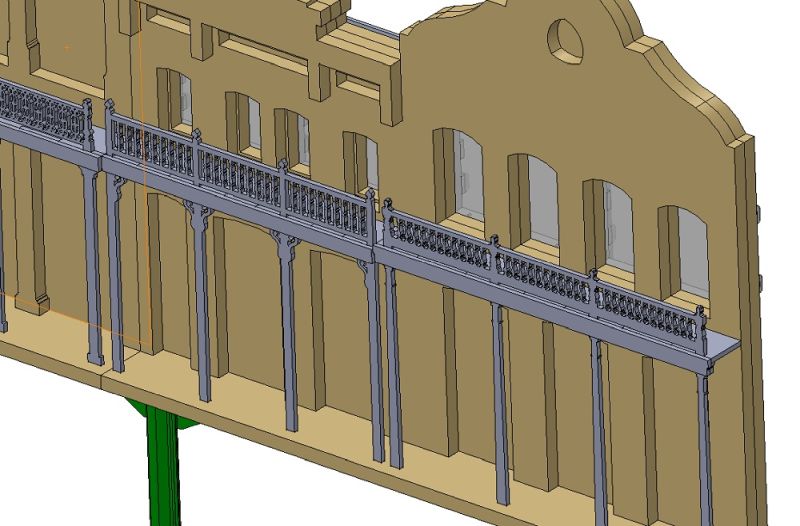
Balconies will mainly be white, so I’ll use the acrylic that Hollywood was kind enough to give me (which originally came from Jon, I believe). So thanks again to both of you guys!
The individual building panels will have z-clips bonded to them, which will clip onto a 3/4" aluminum Z-bar. Clip stock and Z bar all came from Orange Aluminum, with is in CA. I bought all I’d need for the entire project. They gave me a great price, no sales tax and free shipping.
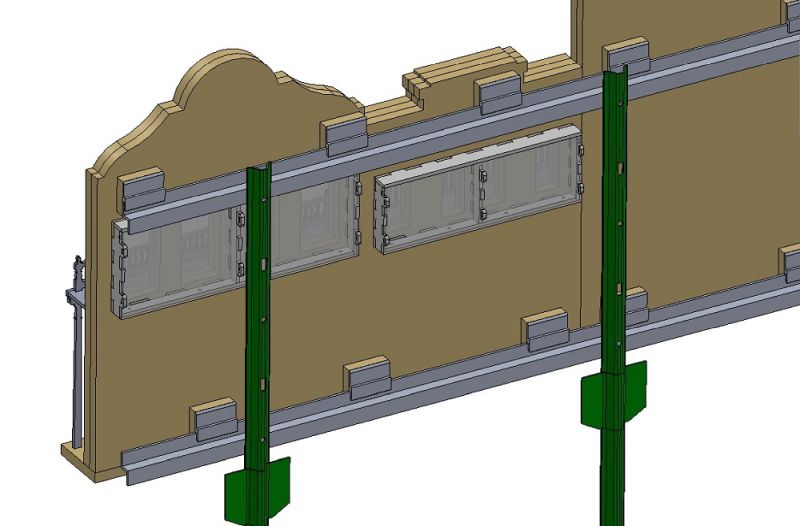
I received the foam (from Harbor Sales) within 18 hours of ordering. Free delivery! And they also sell acrylic. I had them cut 5 4x8 sheets into 20" and 28" widths, all 8’ long. Given my panel dimensions, this gave me flexibility in nesting the parts to reduce waste.
Fabrication officially began yesterday, with cutting the raw stock into blanks for each building. I was really relieved and please that I didn’t have to use a circular saw for this (would be pretty dusty). I made 4 or 5 passes with a box cutter on the cut line, which went about 1/4" deep. The panel then snapped cleanly on that line.
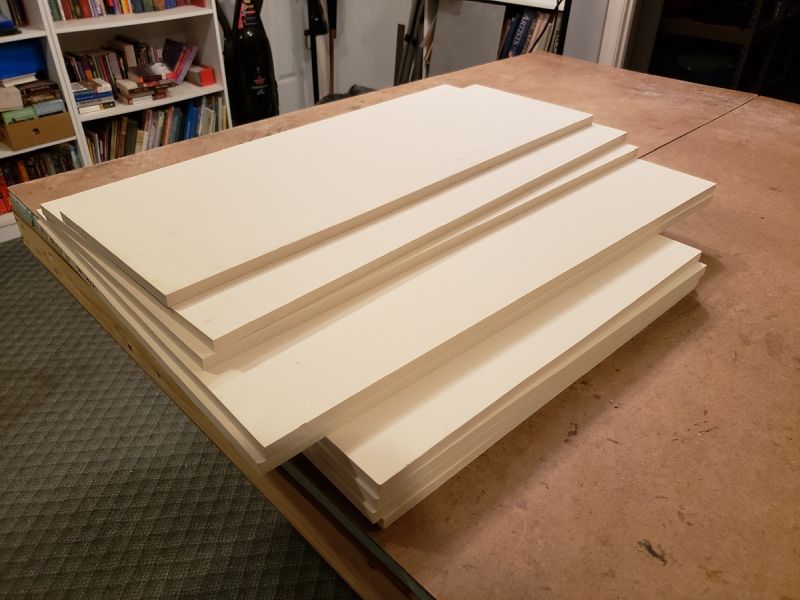
I did a couple hours of foam lasering yesterday, and am finishing it now. It’ll be maybe 8 hours total for this row. Here’s the first building:
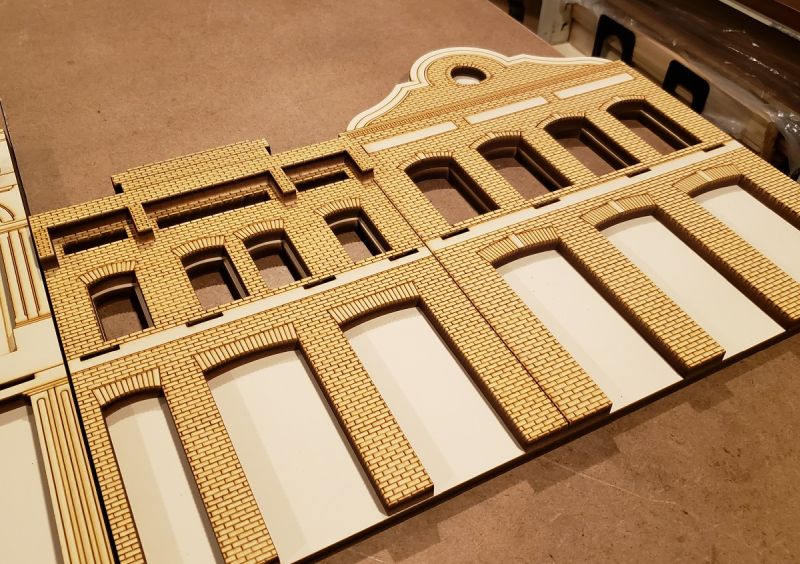
Unlike the acrylic cutting, where my vacuum system doesn’t handle 100 of the the fumes, I’m not detecting any fumes at all from this, nor is my wife, so that’s a big relief!
BTW, this is one of the el cheapo Chinese lasers (~$2k) I bought a few years back. My software is RD works, and I import dxf files from Autocad (actually, it’s a cheaper version of that called BricsCad). If you ever find yourself in the same circumstances, the settings I found to work best are as follows:
- Nozzle height above material: ~.45"
- Cutting speed: 6mm /sec
- Cutting power: 70%
- Engraving speed: 50mm / sec
- Engraving power: 70%
===:>Cliffy