Pete -
I know you’ve seen my loco carriers many times before, but I thought the other guys on this thread would like to have a look at 'em, too.
Loco carriers??
No, I’m not talking about crazy mailmen…
You asked about transporting model engines. Here are some photos of a couple of things I built that allow me to do just that.
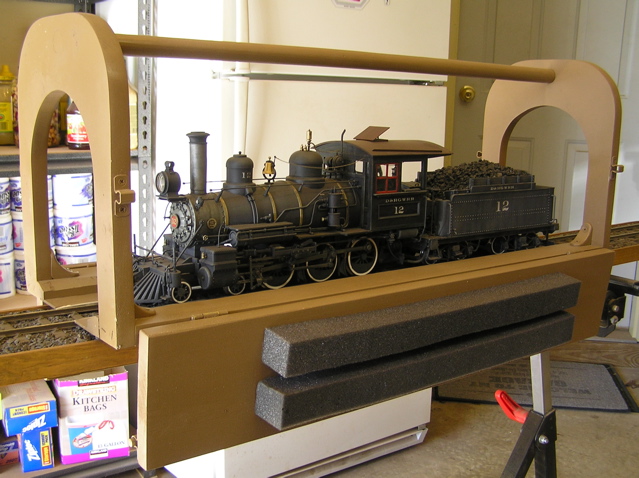
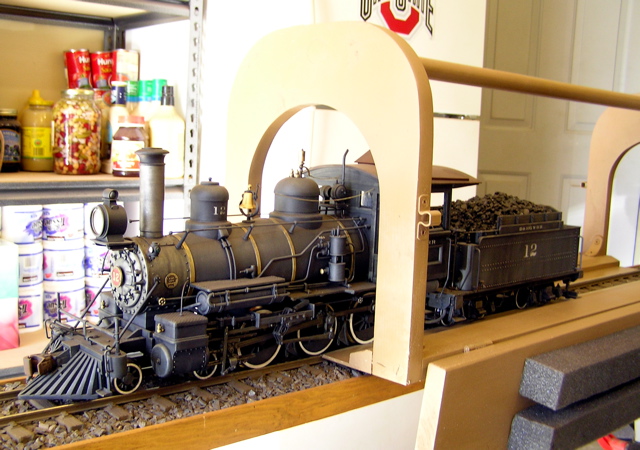
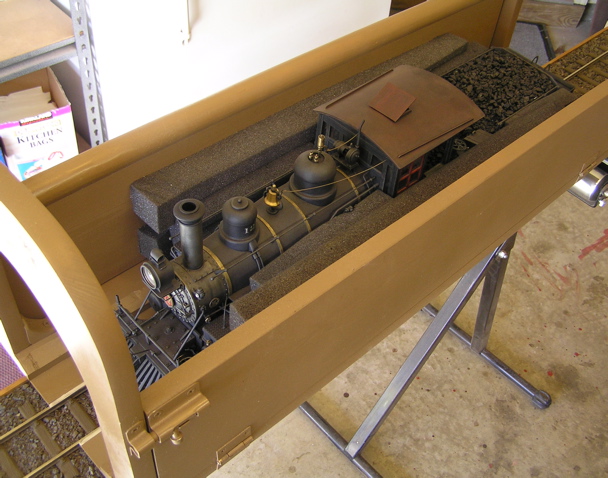
Pieces of foam rubber keep the locos snug and in place when the sides are raised and secured with barrel bolts.
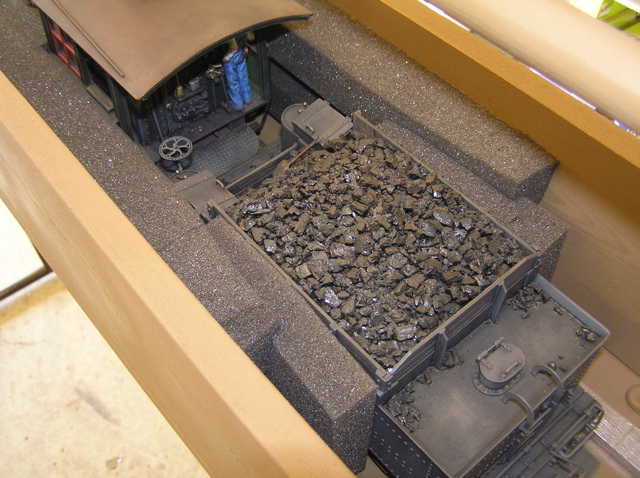
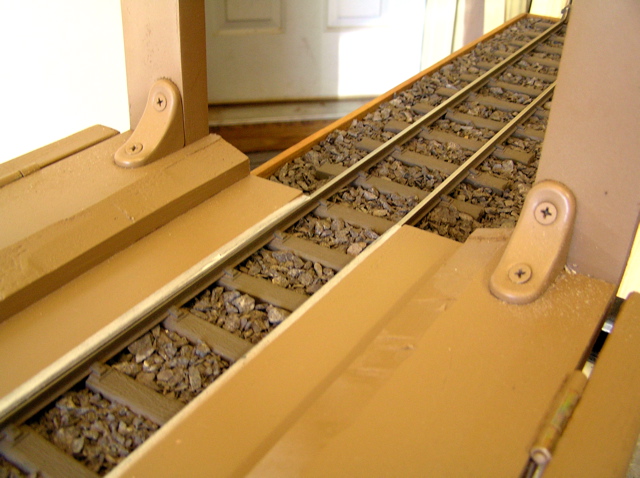
The base is built up with two aluminum contractor’s rules (big 2"-wide yardsticks) from Home Depot. The inside dimension between the two base plates is exactly 45mm. I used a router table with a fence to make shallow rabbet cuts along the inside bottom edges, about as wide as the top of a rail. This allows me to set the carrier down on a straight section and drive the loco on and off under its own power. By the way, the aluminum cuts easily and does not dull or harm the router bits.
I filed the tops down on each end to create little ramps. (More detail on how I did that later.) The loco gets its power through the aluminum base plates that are in direct contact and aligned with the track on the layout. Since I’ve gone to battery-power exclusively, it doesn’t really matter any more, but now it works for just about any engine.
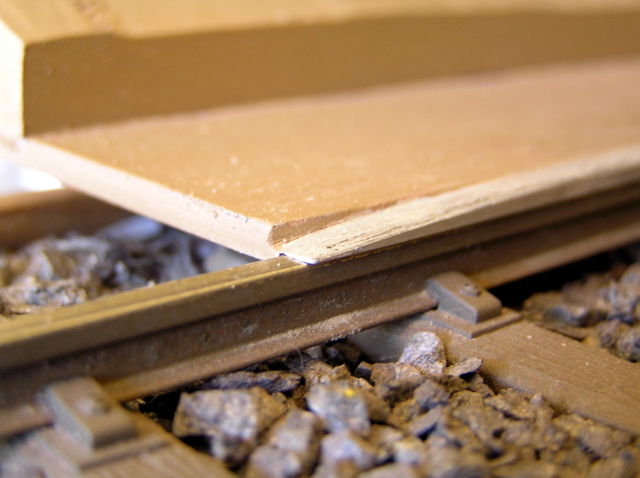
Here are some close-ups of the edge of the base plates. The carrier is aligned with the track by the rabbeted notches on the underside of the plates.
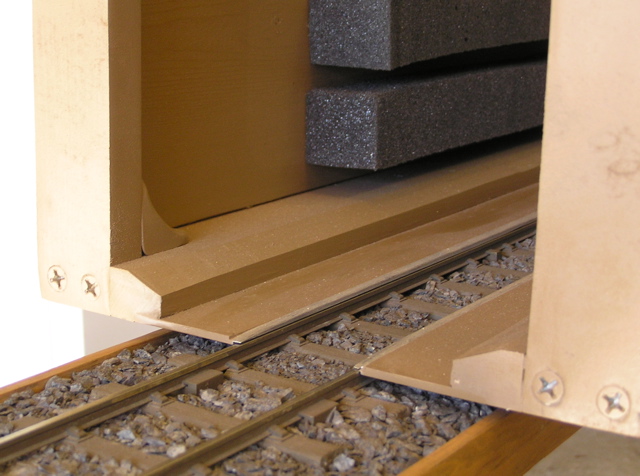
I cut another rabbet in the long wooden rail to which the metal base plate is attached. It’s about a half-inch wide and exactly as deep as the thickness of the metal stock. The plates are glued ‘n’ screwed into the rabbet from the underside. I countersunk the holes – set about an inch and a half apart along the rail – and used short flathead woodscrews so that the bottom of the carrier is completely flat. I had to bevel the inside top edges of the wood in order to clear the cylinders, valve gear and other overhanging parts of the loco as it runs on and off the carrier.
If you can find aluminum bar stock wider than two inches to use, then that last step probably won’t be necessary. BTW, I wouldn’t try using anything less than two inches wide, either – at least not for 1:20.3 scale steam locos.
After I cut the rabbet on the underside of the plate, I filed a ramp on the top side about a half-inch long to smooth the transition between track and carrier.
As you can see, it’s about the same width as the rabbet notch underneath. (When I painted it with a rattle-can, I masked off the top, side and bottom of the plate to assure good electrical contact.)
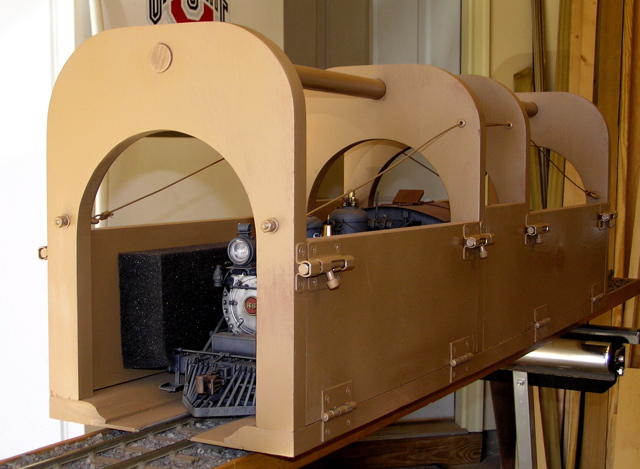
Since brass and steel Accucraft models are much heavier, I built this heavy-duty version to carry my C-21. I used the same techniques, just adding a center support and two sets of side panels instead of one.
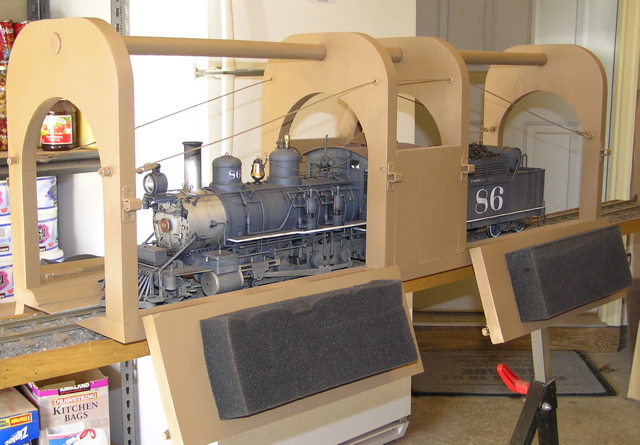
The wire cables on the Accucraft carrier were added to prevent the carrier from buckling under the greater weight. However, I find that I can’t tighten them fully without bowing the whole thing up at the ends (making it impossible for the loco to drive onto the carrier from the tracks) so I’ve got them set just this side of “taut” in order to pick up any unexpected strain. I suppose I could have gotten away without them, but they seemed like good insurance at the time.
Again, you can see here how I put all the parts together.
I haven’t drawn up any plans for this – I tend to do things “by guess and by golly” – so don’t ask me to send you any, but don’t hesitate to ask me any questions you may have.
I do hope this inspires you to try to build carriers of your own. Good luck