I’m using DCC, and DCC-controlled switch machines from Train Li. As a winter project a few years back, I went whole hog in making up a wireless panel system to control them.
There are three of these boxes. They’re laid out on the philosophy of pressing a button and lining up turnouts for a loco in that position.
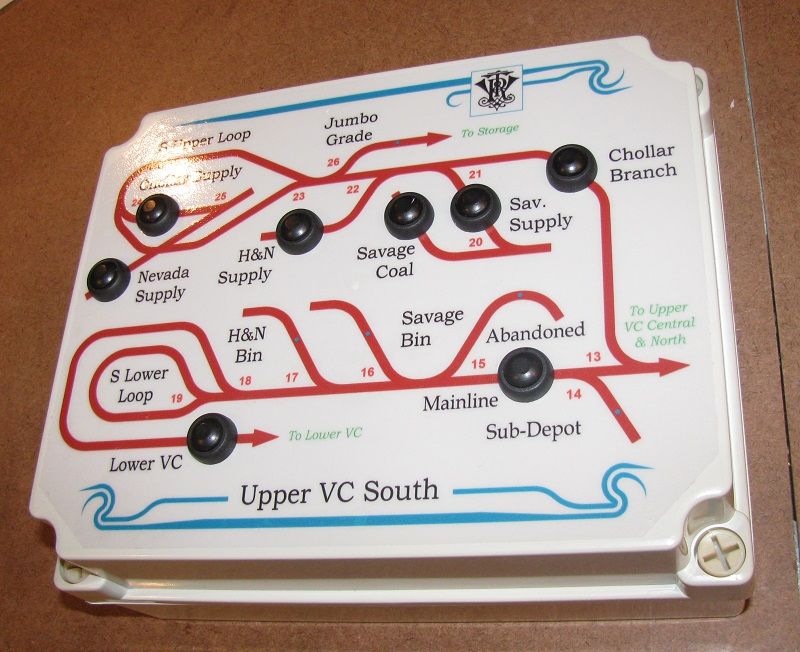
The buttons pigtail into an old parallel printer cable…
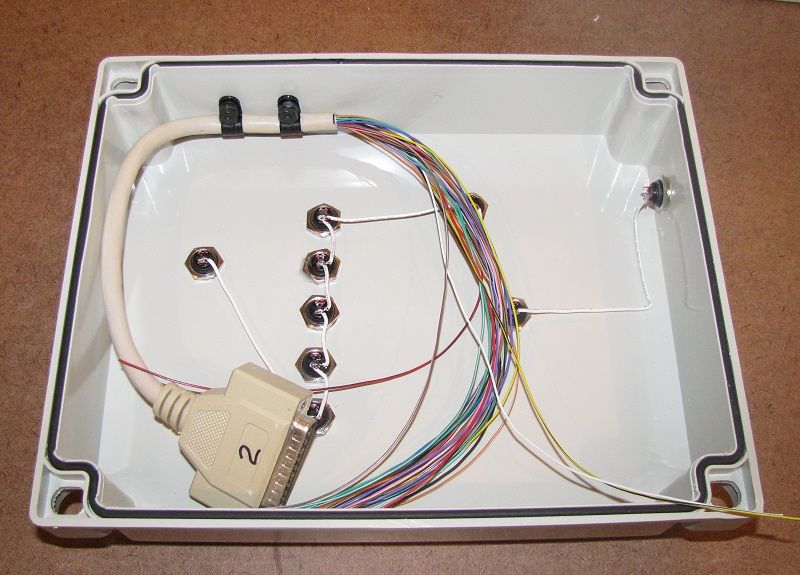
Which plugs into a transmitter for a radio-controlled relay.
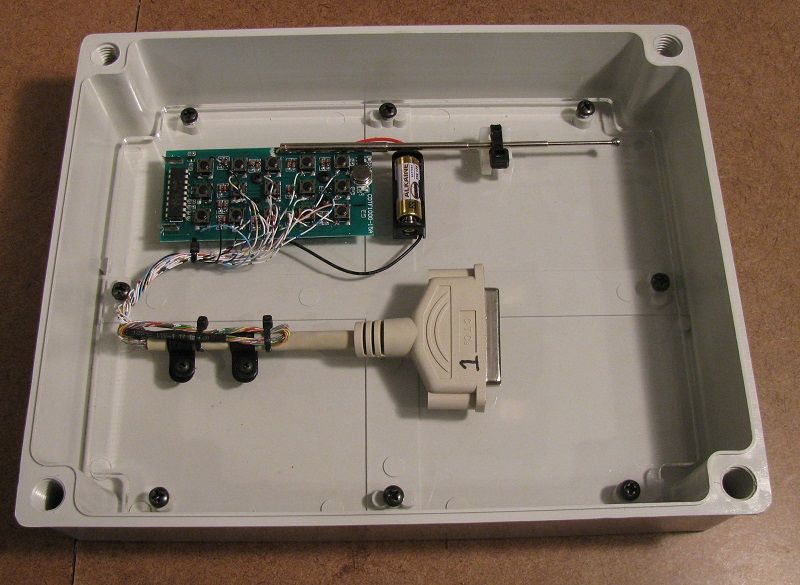
The relay board can be used for whatever. Mine are mounted on a panel, wired into an NCE Mini-Panel to run scripts that thrown sets of turnouts according to which button is pressed.
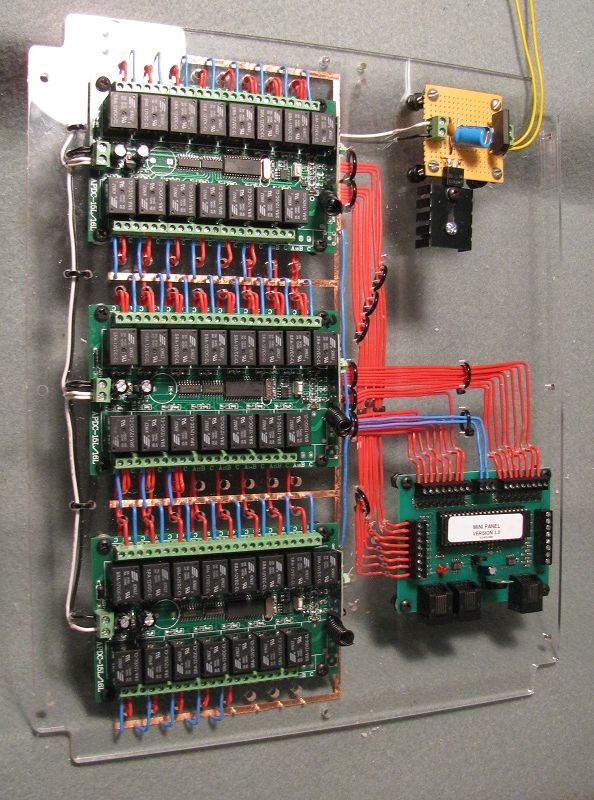
This panel is in another watertight box.
OK, there are drawbacks to this approach. The script-writing involved a fairly puzzling spreadsheet, and it wasn’t easy to get everything right. If I had to reprogram everything, it wouldn’t be easy. Main problem though is that I’ve had consistent issues with the Train Li switch motors. Sometimes they decide to work in the opposite direction, and when you’re using a script for a route, the whole route brakes down, and you have to override individual switch machines via their DCC address. I have my own switch drive design, and am planning on building those as replacements.
Anyway, to control solenoid valves, you can route the relays directly to them and use the buttons to toggle the relays (and therefore the sv’s) on or off. Or you could use a DCC solenoid valve controller, Greg uses something from Digitrax as I recall.
Cliff