So hear again is one of the reasons I have come to appreciate virtual modeling and virtual assembly. Not only do you have to tackle real world problems it can actually teach you something that was not intuitive to you from the start.
One of the things, if you have been following this thread, that has bugged me is the âflywheel crank shaftâ. I canât see it. Well now I am thinking there is none at all. I canât see how there can be a single shaft to which both drivers are attached and here is why. Maybe someone can offer some insight.
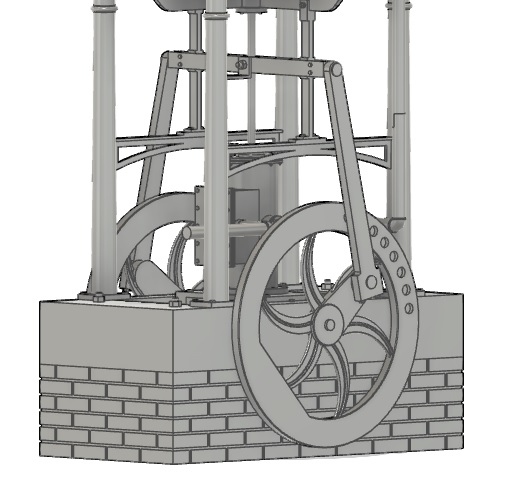
So I went to design the drive rods to connect the guide rod (my name for it) that is being driven up and down by the steam cylinder to the flywheels. First minor problem was that I did not have the wheels properly quartered they were off by 7.5 degrees. I discovered this by first making one side and then making a mirrored part in two planes (left and right/ front and back). This produces a part that is exactly quartered to its counterpart. When I looked at the opposite side of the model the holes didnât line up. Easy fix you just rotate the driver on its center line axis until they do. in this case I needed to rotate it 7.5 degrees.
Now with that all done and me being very proud of myself, a giant glaring problem arose. It wouldnât work!!! If you look at the above picture when the guide rod thing goes up it will be pulling the flywheel pins up. When it goes down it would drive the flywheel pins down. If you havenât figured this out yet it will be trying to drive the fly wheels in opposite directions which would make for some serious ugly if they were rigidly attached to the same shaft.
On a steam locomotive we drive opposite drivers which are attached to the same shaft with separate cylinders and separate drive rods. They are independent of one another. So they themselves are quartered (for the lack of a better term) from one another. So they can drive their respective driver in the same direction while installed on the same axle.
This canât happen here. So What I am thinking unless someone can point me to the folly in my thinking is that there is NO single central shaft connecting the flywheels. They have their own shafts attached to their own bearings and everything works independently and if I am not mistaken, this means when this thing is humming along the flywheels are doing so in opposite directions.
If this is the case and they are independent it brings up another observation. Do the flywheels even need to be quartered or would it be indifferent? Or would it even be say better for them to be 180 out instead of 90 degrees out? Should they be 0 degrees out?
This is your fault Rooster. And this is why my other projects get Devoned.