And now Something Completely different;
A Stone Assay Office.
On my layout wood buildings dissolve …
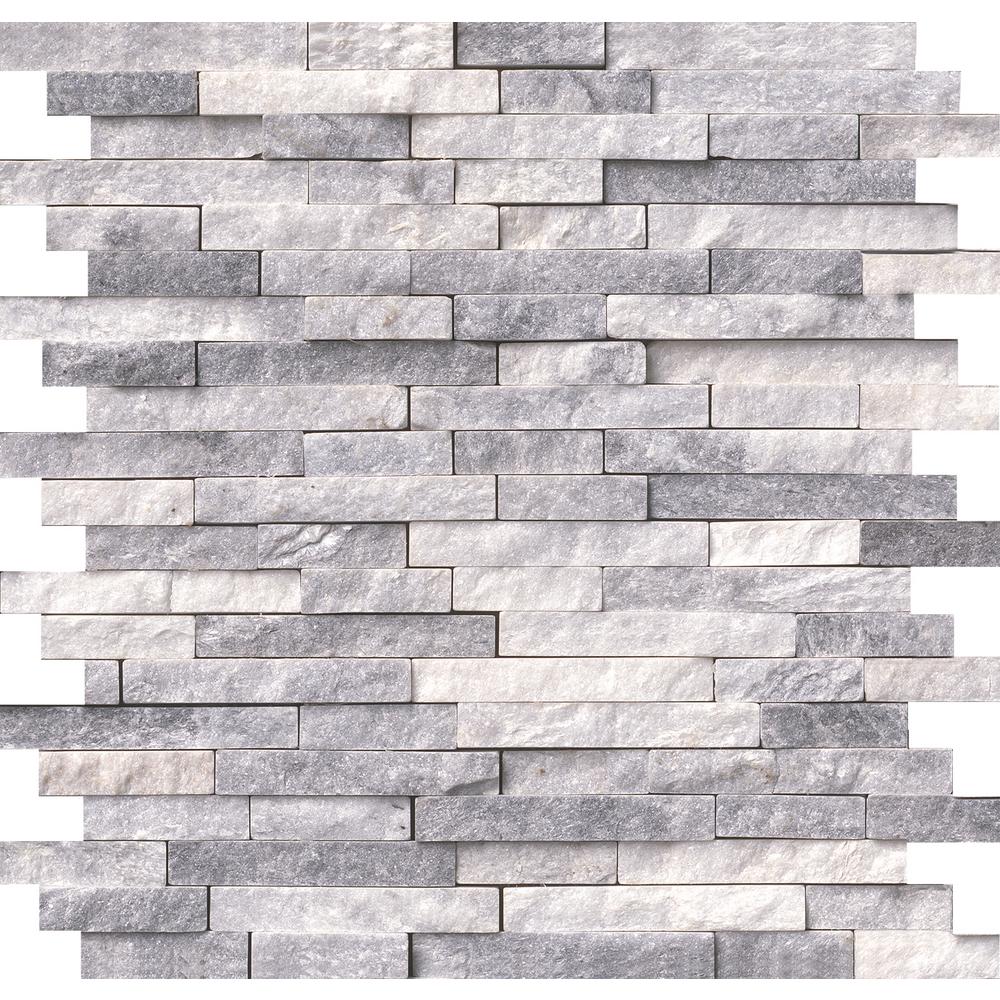
Stones should survive … it took 3 sheets of these to build my Assay Office, the first I bought for my junk box gamble. This year it paid off. Contest cost = $26.00
Unfortunately they are glued to a backing for application as a unit and I needed individual stones. Half my build time was liberating the rock. Luckily for me I have a lapidary shop and could sand the glue off, but tedious was the rule of the weeks.
Overlooked were the polished stones included, but they became a floor and counter. First sheet …
(https://www.largescalecentral.com/FileSharing/user_2288/2020Mik/rock01.JPG)
Also since the blocks were all 3/8 x 1 1/8" I cut some into 3rds and 2/3rds as seen on left. Overlapping seams is a must for strength.
The longer white stones were foundation and lintels over doors and windows.
I have a plan! (subject to changes)
(https://www.largescalecentral.com/FileSharing/user_2288/2020Mik/DeluxFloorplan.JPG)
Since I have polished tiles I changed the showroom floor to tiles and for the contest compromised an a dirt floor for the shop portion, but if I have the tiles…
I used a caulking gun and a tube of sanded Ceramic Tile Caulk for my mortar. The tin is my layout’s footprint for the building.
(https://www.largescalecentral.com/FileSharing/user_2288/2020Mik/wallsUpish.JPG)
I tried using the box to keep the outside surface semi- flat, but oozing caulk made a bond with the cardboard that was a tough peel away, but the box did contain my mess somewhat so it’s good.
(https://www.largescalecentral.com/FileSharing/user_2288/2020Mik/IMG_0576.JPG)
Spirit of Mik … As a folk artist Mik was great at re purposing trash, my bottles below are from small glass syringes cut on my diamond saw.
(https://www.largescalecentral.com/FileSharing/user_2288/2020Mik/bottles02.JPG)
A little paint via Q-tip went inside to make the glass appear colored …
(https://www.largescalecentral.com/FileSharing/user_2288/2020Mik/IMG_0589.JPG)
(https://www.largescalecentral.com/FileSharing/user_2288/2020Mik/details01.JPG)
I haven’t mentioned the brick oven that gives cause for the Chimney …
I had a sheet of embossed O scale bricks, molded in red, over the years that sheet was splattered with a cream colored paint. I cut a block of wood for the core and JB welded brick panels to it. The corners were covered with Plastruct 1/8" angle strips and brass tubing was cut and spring steel (black) wires became binding rods… The grey barrel came from a glass jar and the melting furnace from plastic mini vinegar bottles…
A black marker denoted the oven’s openings… as seen above.
(https://www.largescalecentral.com/FileSharing/user_2288/2020Mik/details03.JPG)
(https://www.largescalecentral.com/FileSharing/user_2288/2020Mik/details04.JPG)
Above are my Mik recycled details.
Since the interior makes this model, I decided to go with a Ruins look to be seen on my Scenic Railroad … only a partial roof around the chimney
(https://www.largescalecentral.com/FileSharing/user_2288/2020Mik/details07.JPG)
(https://www.largescalecentral.com/FileSharing/user_2288/2020Mik/001.JPG)
When planted, dirt will hide the shadows and cover the lower half of the foundation and the track will be ballasted too.
(https://www.largescalecentral.com/FileSharing/user_2288/2020Mik/005.JPG)
(https://www.largescalecentral.com/FileSharing/user_2288/2020Mik/01.JPG)
(https://www.largescalecentral.com/FileSharing/user_2288/2020Mik/006.JPG)
Thanks to Benevolent Bob our underappreciated Host and to Dave Taylor as our acting Trail boss, keeping us headed in the right direction: To Have Fun and beyond!
I look forward to this event every year, it’s fun to rub shoulders with truly great modelers, mebbe some will rub off on me!
For more details; https://www.largescalecentral.com/forums/topic/30146/2020mik-chimineyastoldto-john-c