I have been actively testing Martin’s system in a couple of different scenarios during my vacation this past week. My first “bench only” test was to use Martin’s system to replace the two-stick radio driving a Railboss Hobby system. I was able to make it work, and Martin is making some modifications to his RC app to have a Railboss specific version, however his present system will probably never be a replacement for the 2.4Ghz radio simply due to channel limitations. Railboss really needs 4 channels and adds a feature with 5 channels. Martin’s system has 3 servo channels, so it’s control of Railboss is limited to Throttle, Direction and Sound Triggers. Momentum selection and two locomotive selection can’t be supported with the current hardware from Martin.
I never planned on using his system with Railboss anyway, but wanted to try it. Where I really want to go is standard R/C using a phone or tablet to control a locomotive. I wanted to experiment with the inexpensive electronic speed controls from China. I picked up a Powerday RC 10 Amp ESC for brushed motors of Amazon for $10. I begain by connecting it up on my workbench with Martin’s controller and an old RC Car motor being powered by a 12V bench supply. I’m glad I did because I learned some quirks of this ESC and how to get around them.
Today I took it to the next level and temporarily attached it all to a Bachmann Saddle Tank Porter so I could get a feel for how this will work in an actual locomotive and try some switching operations. I took a bunch of pictures which I will share with you now. This photo of the fireman’s side shows my very temporary set up. 11.8V LiIon battery on top, the blue ESC is on the running board and a voltage converter is taped to the firewall. All that excess wire is left over from bench testing. I was just too lazy to reconfigure everything…
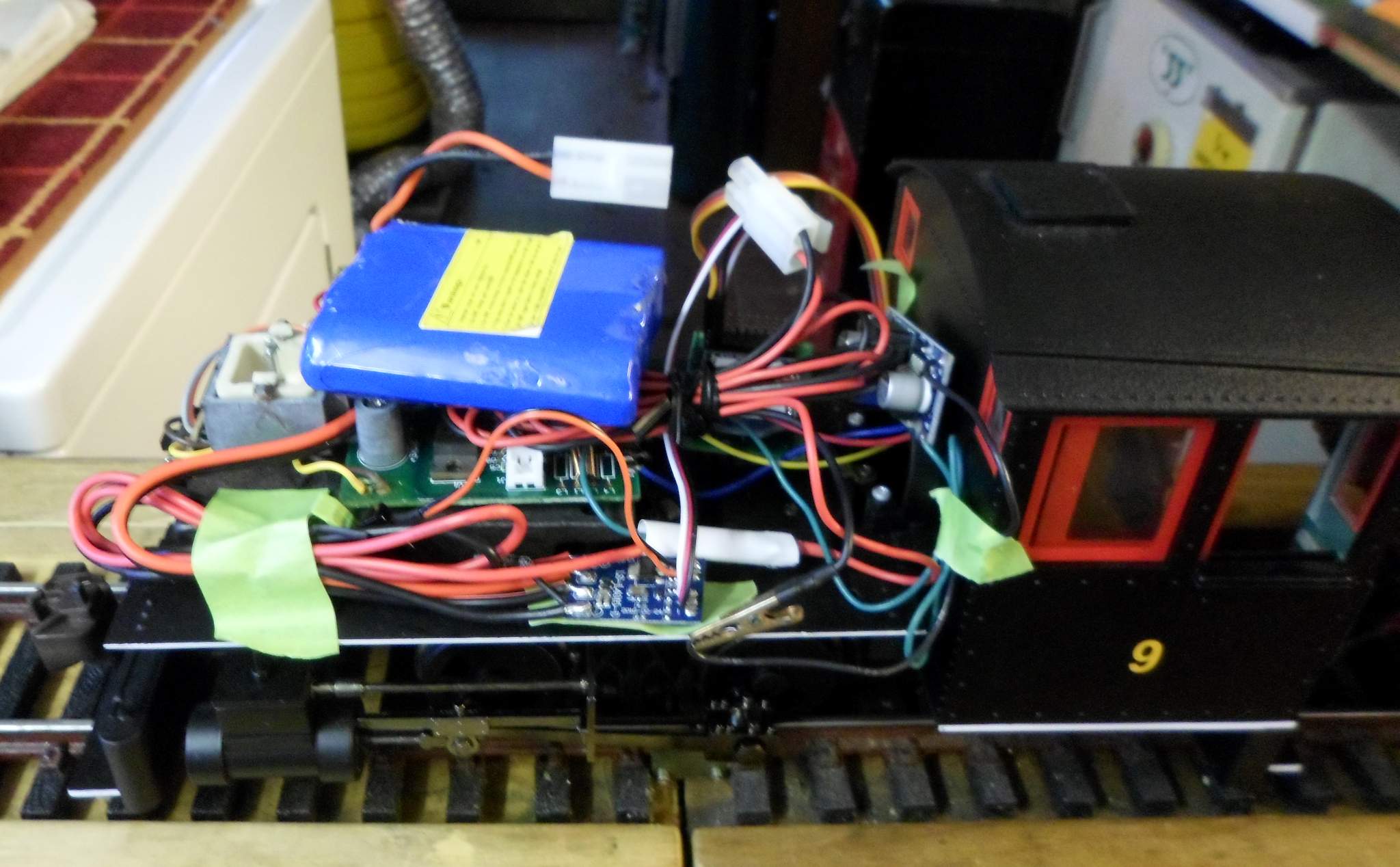
I left the Bachmann circuit board in place (for now) but only the motor circuits are being used…
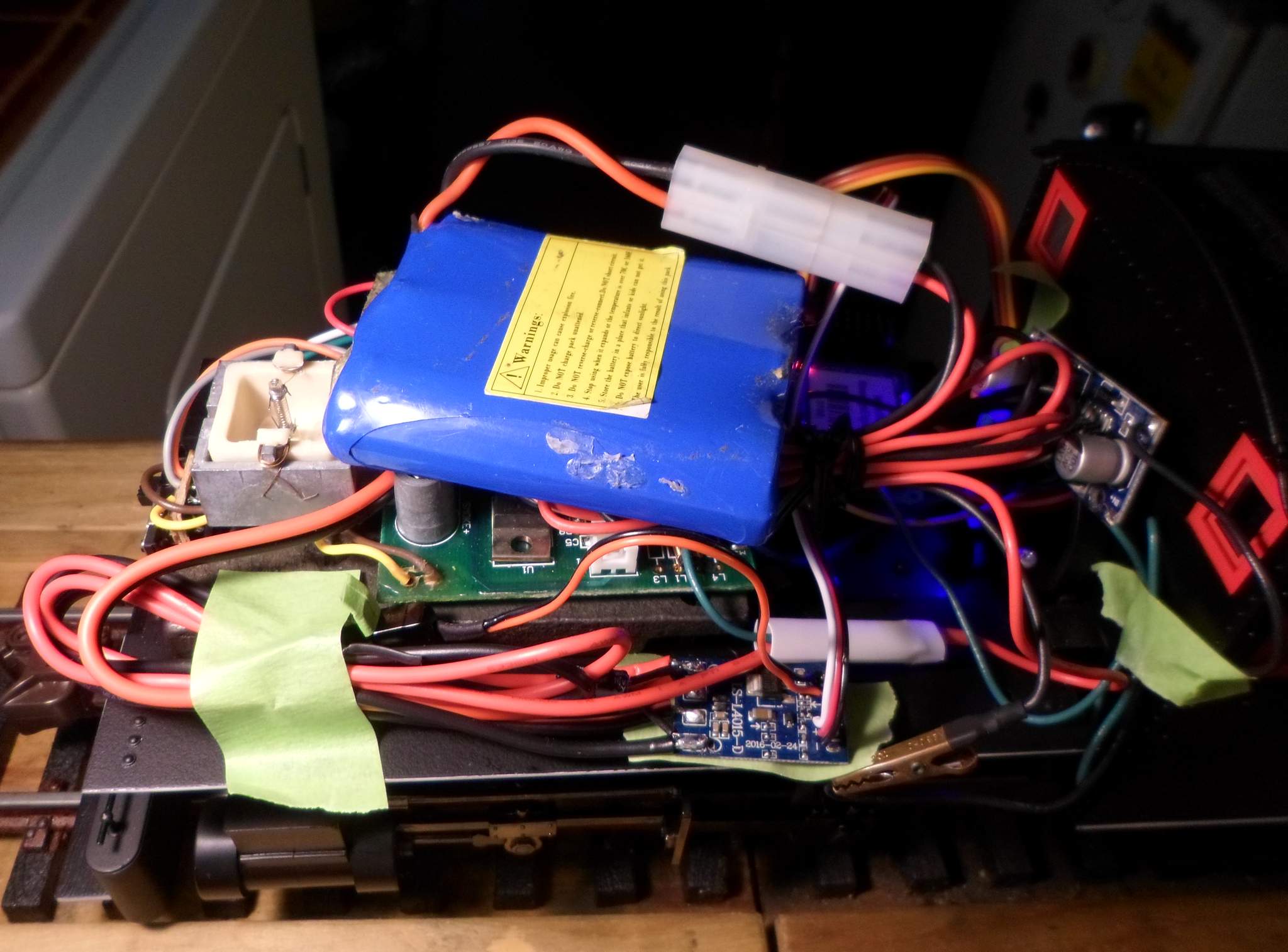
This is the Powerday ESC. I cut off the heat shrink and added my own leads for Battery and Motor since I didn’t have any of the mating JST connectors the board came with. This model is Center Off with no brake…
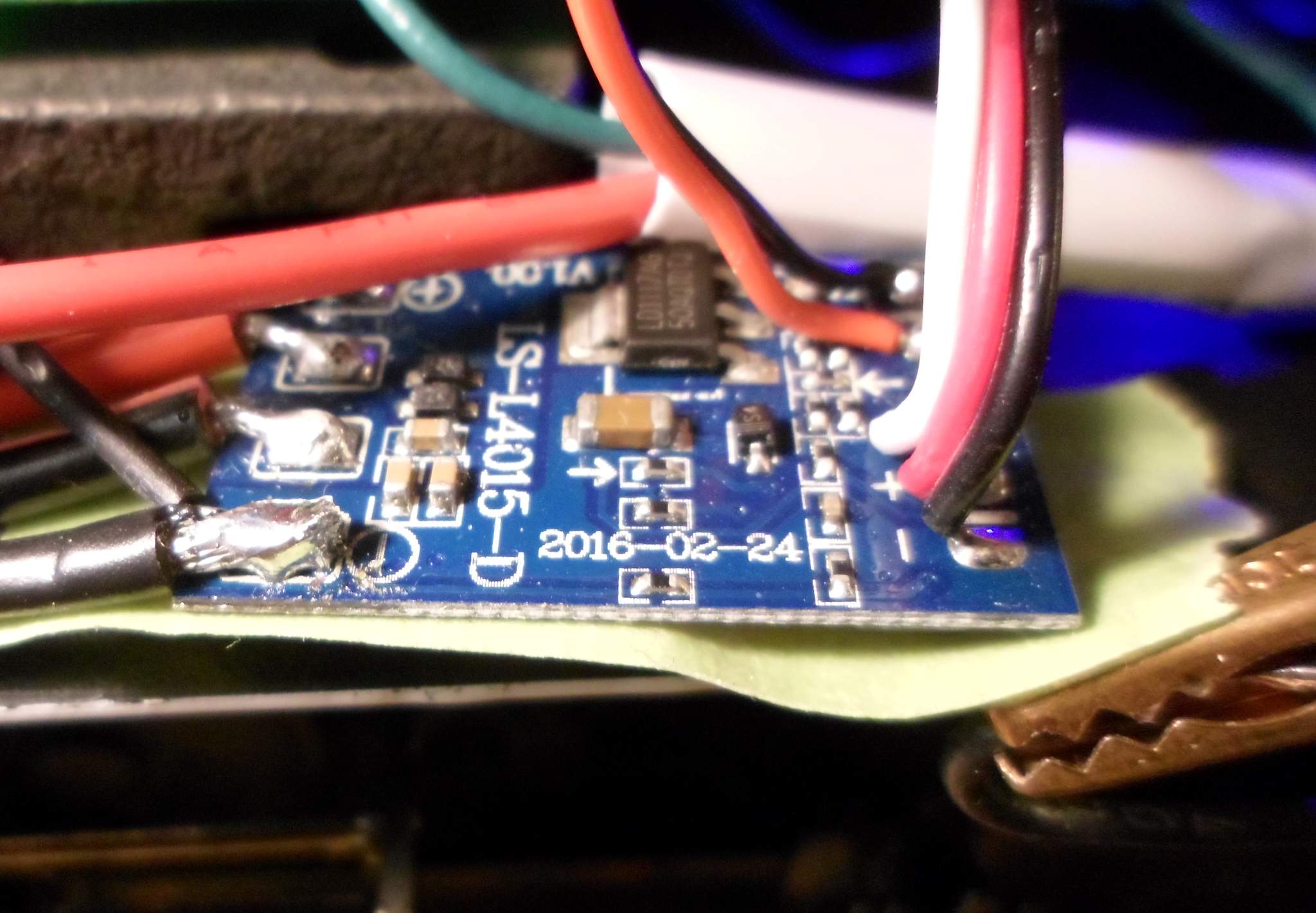
This is a close-up of the eBoot DC-DC voltage converter. It also came from Amazon in a 6 pack for $12. I am using it to derive 5VDC from the battery. It works very well and holds the output voltage to within .002 volts so long as battery voltage exceeds 6.5V. I use the output to drive Martin’s board and will also use it as a voltage source for LED lighting…
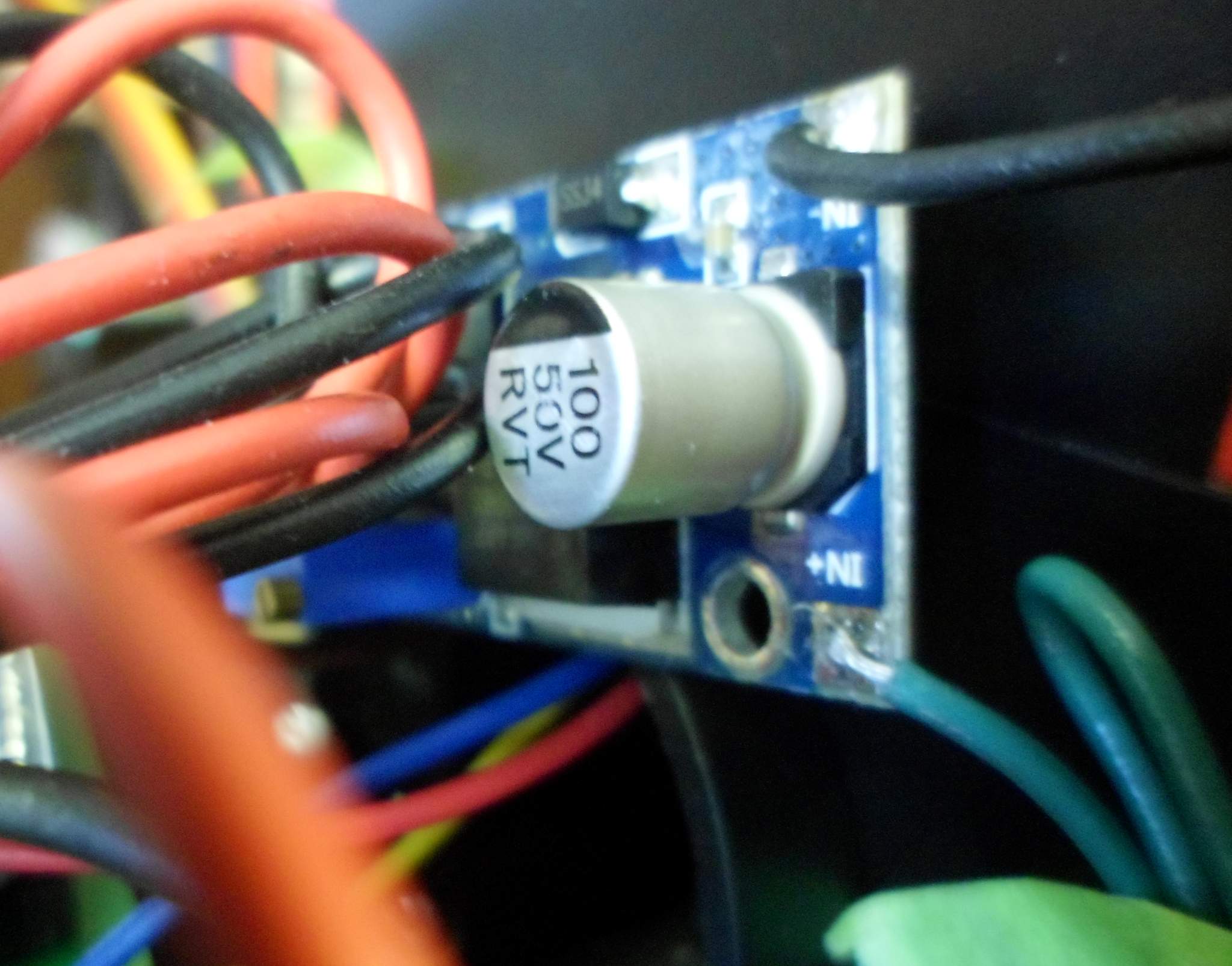
Over on the Engineer’s side you can see the other side of the DC converter and Martin’s board on the running board…
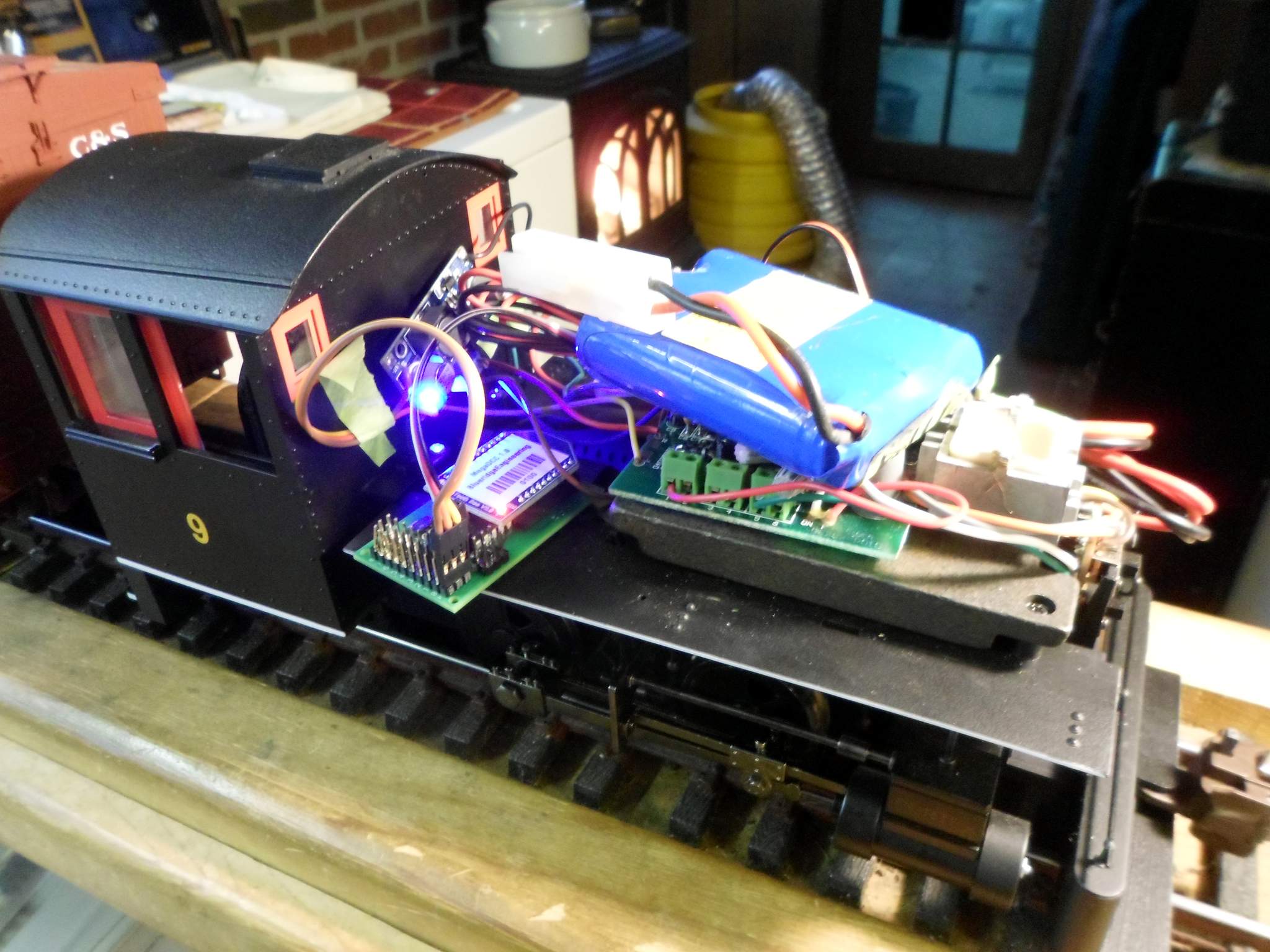
Close up of the other side of the SC Converter…
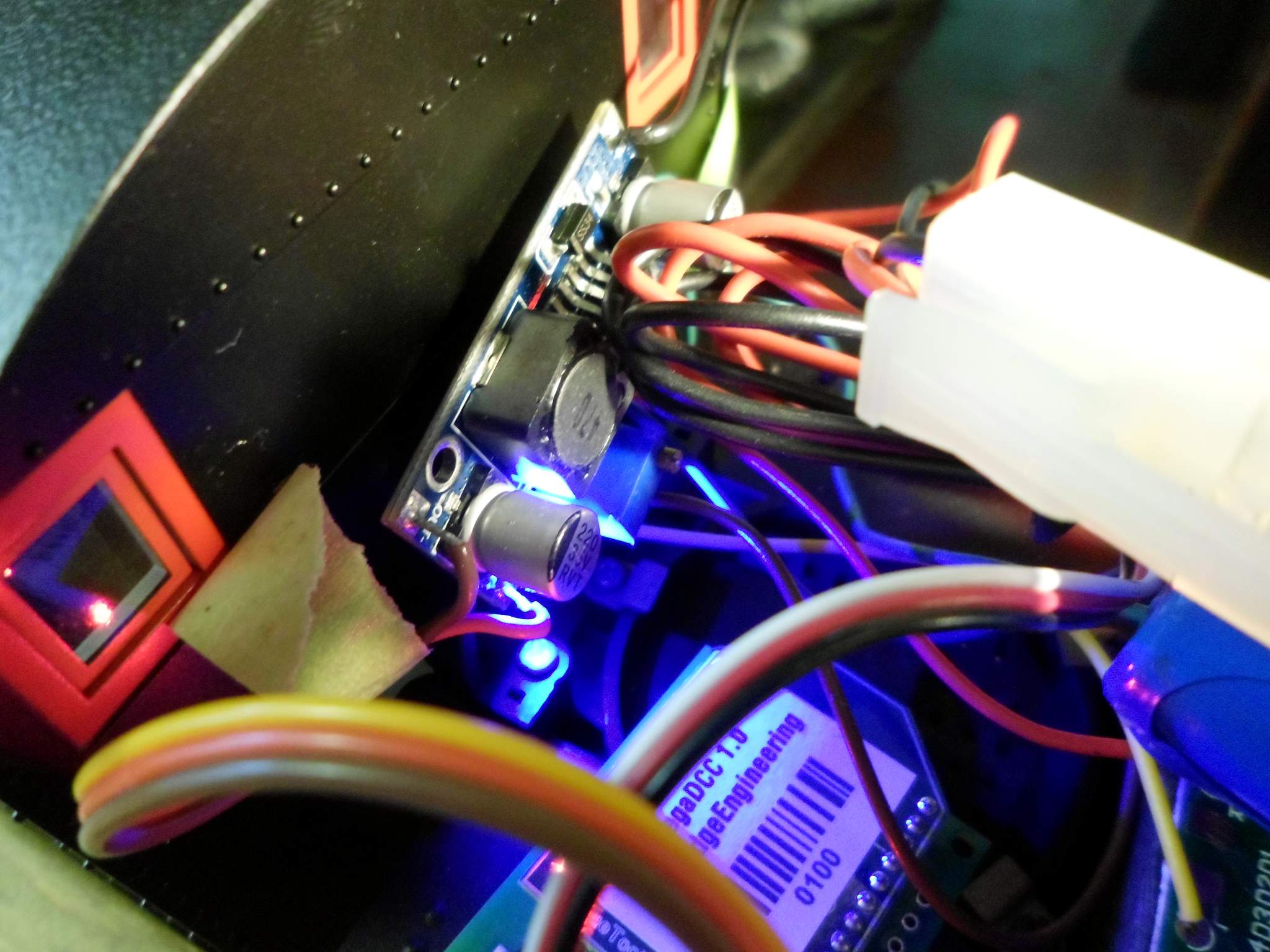
And a close up of Martin’s board. The yellow wire of the cable connected to P is not connected to anything. The Red and Brown wires power Martin’s board with the 5V output of the DC Converter. Only the data line feeding the ESC is connected to servo output 0. I found that if I used the BEC output of the ESC to power Martin’s board, the ESC would power up in full throttle regardless of the position of the on/off switch on the ESC. Wired in this way the on/off switch works to keep the ESC off line until the Bluetooth system is powered up and linked to the app. When the app is linked, powering on the ESC last keeps the motor at zero throttle as the ESC comes op…
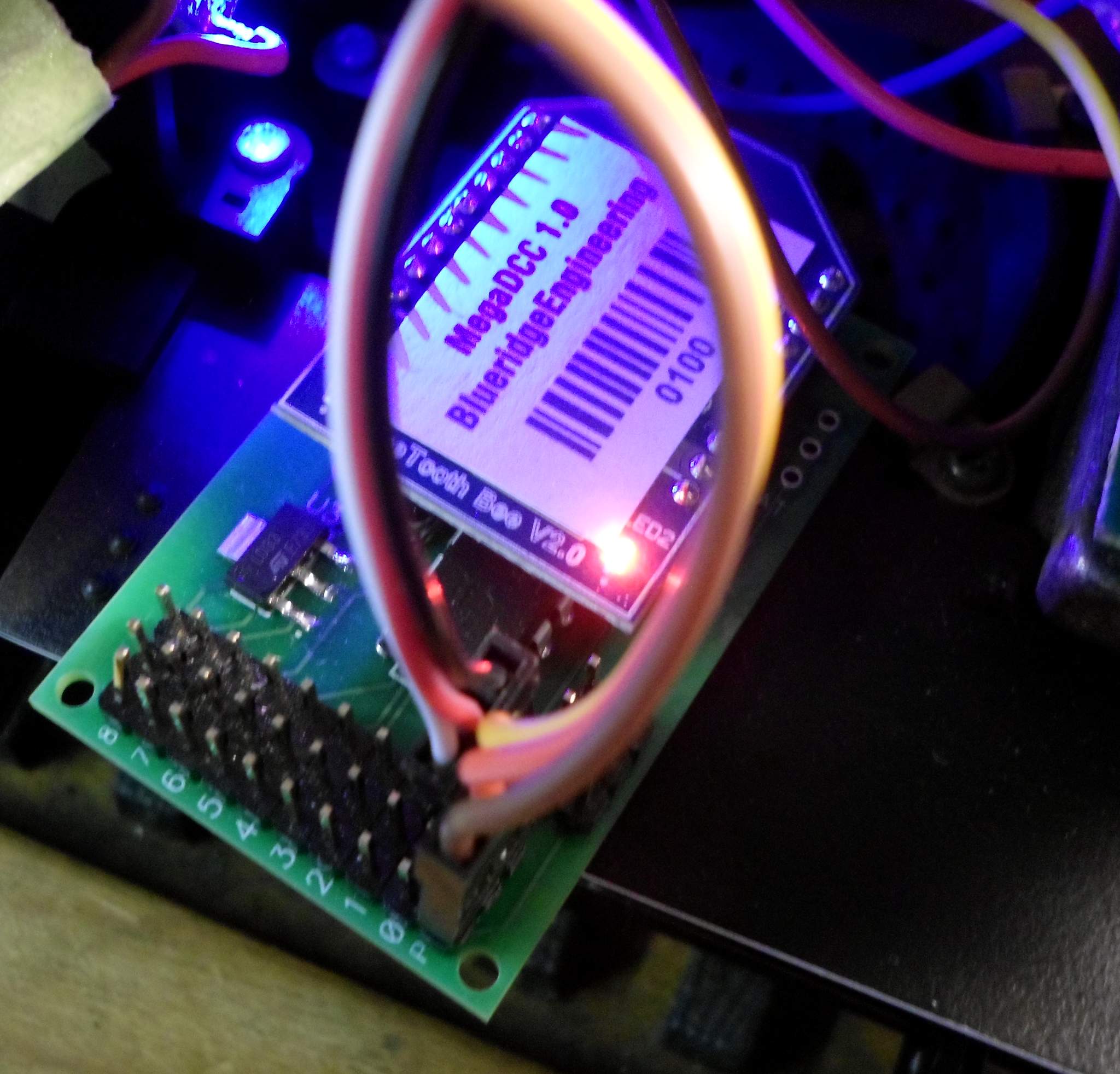
Front view of the test set up. The Orange and Grey wires from the switch are tied to the Motor Output of the ESC. This came directly from Bachmann’s documentation as the motor connections for a DCC decoder…
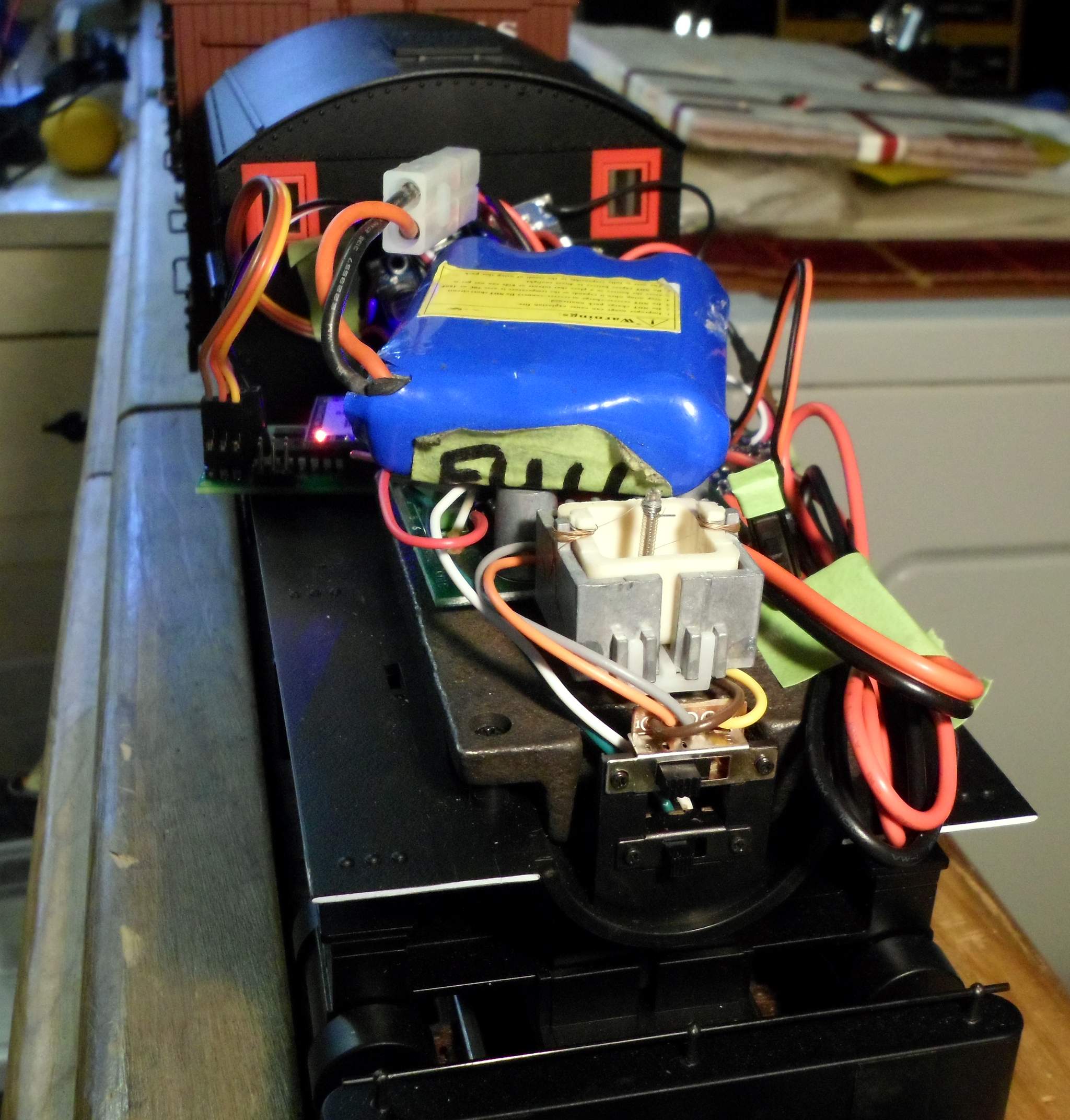
I did some running and switching with this single boxcar. I was quite happy with the throttle response although the top-end speed with 11.8V was a little slow. I tried later with a 14.8V pack with much more pleasing results…
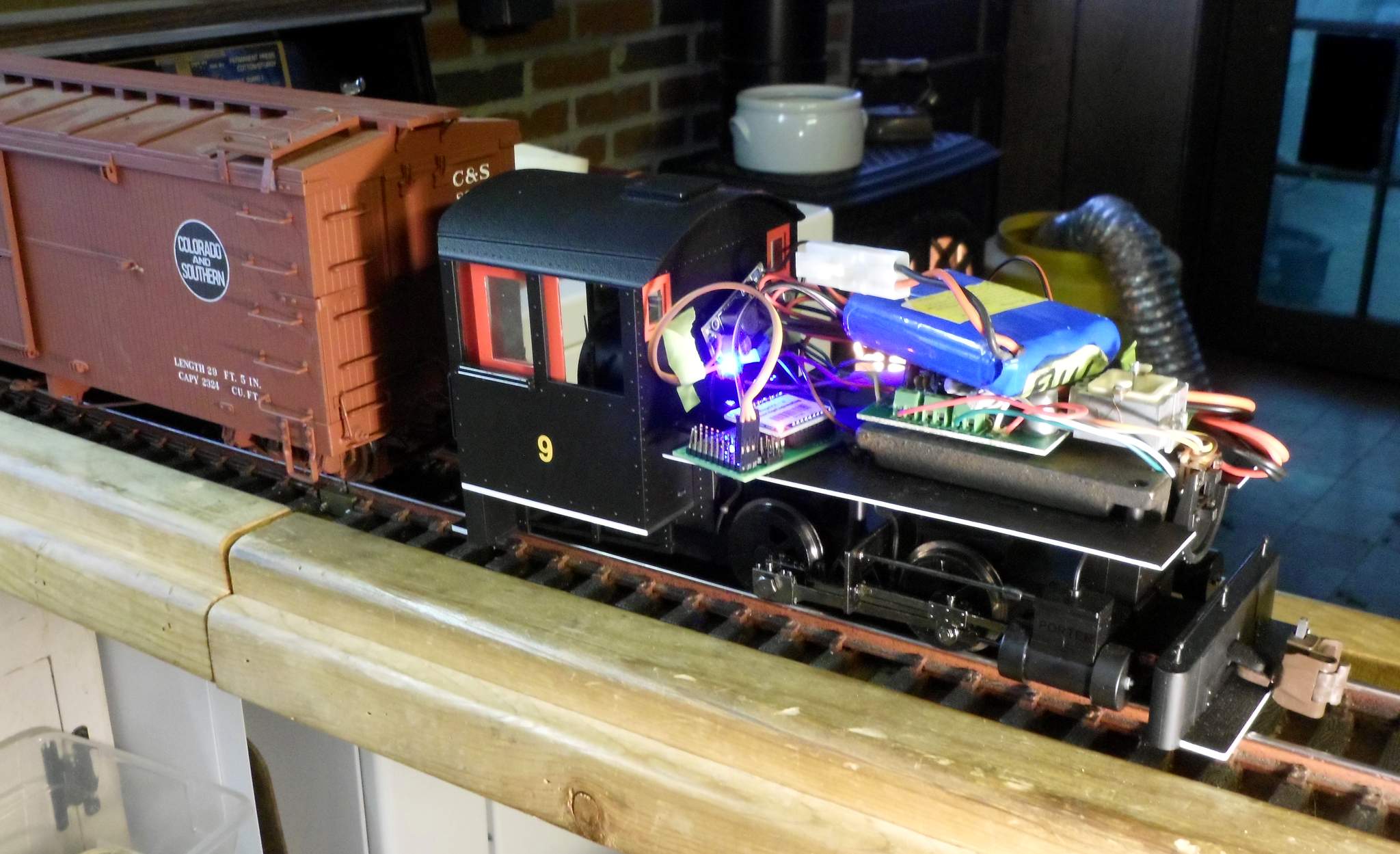
I am using an Amazon Fire 7 tablet ($35 Christmas 2015, $39 Christmas 2017, Regular $49) to run the Android Bluetooth app. The screen shown is Martin’s Generic R/C app - Three servos and two digital logic (5V on/off) buttons. The board’s DCC Throttle output tracks the throttle servo output for hybrid setups using a DCC decoder for sound and lights…
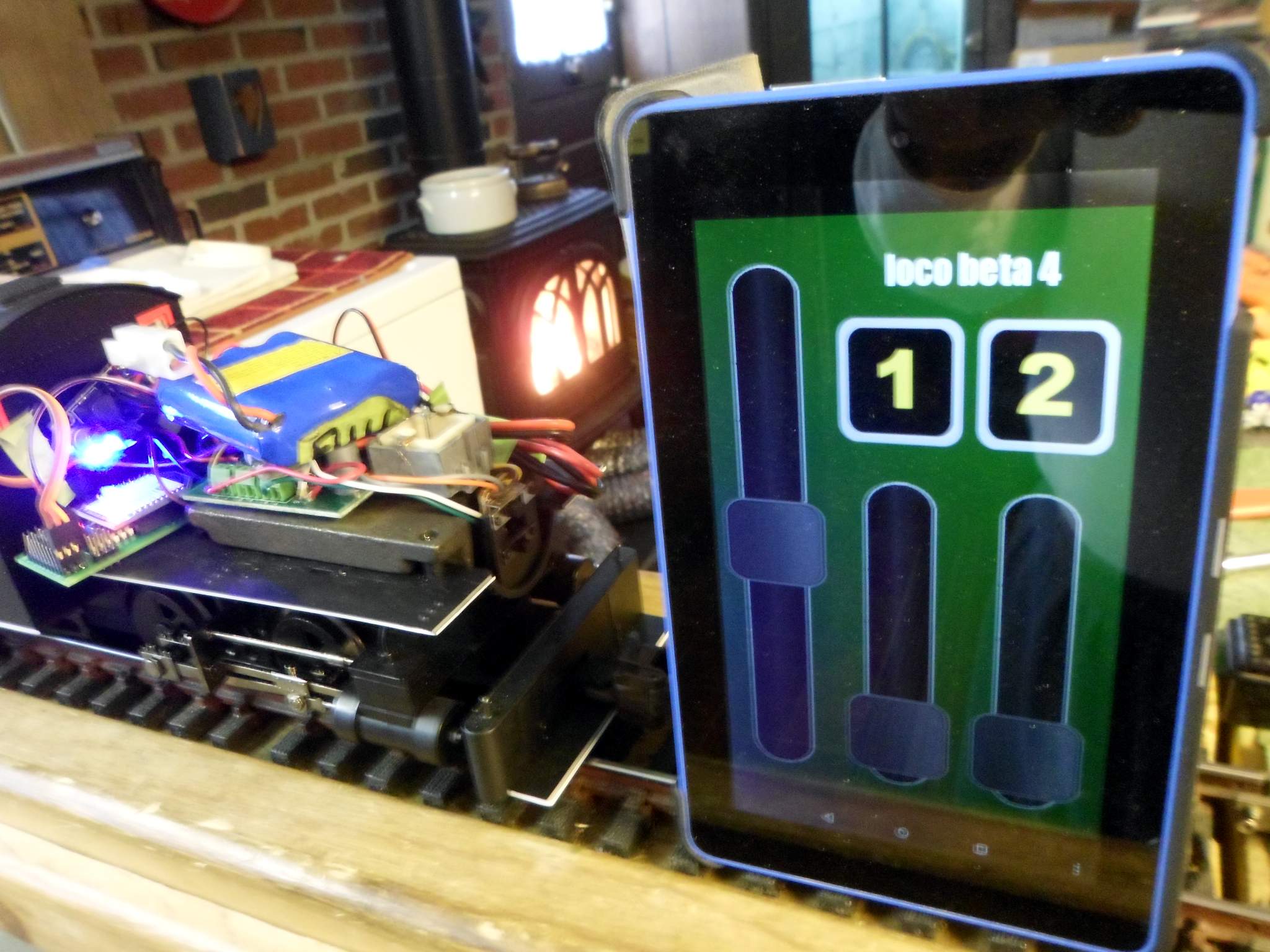
I think I am just about ready to commit to installing this system in this Porter for use as a captive switcher at one of my indoor yards. There is one minor issue that I need to sort out. I think it is the fault of cheap the ESC and I’m hoping I can smooth it’s output: When at low throttle positions (forward or back) the motor in the Porter squeals quite a bit as the ESC sends widely spaced pulses. As the throttle is raised the frequency of the squeal increases until it goes away at about half throttle. Any electronics gurus that care to give some advice on how to eliminate that, please speak up (https://www.largescalecentral.com/externals/tinymce/plugins/emoticons/img/smiley-wink.gif)The ESC has a 100Mfd electrolytic filter cap on the battery input, but nothing on the output. ESC gets all it’s power direct from the battery.