Thanks for all the comments and encouragement guys.
Pete, I have looked at the Llags creek frogs but at $16 a piece for my 12 switches it ads up quick. I won’t put this much money into my furnace or wax and plaster. Then once I’m successful I’ll be able to cast the other 100 or so for the rest of the rail road when we move. Another big motivation is that I’m saving a bit of space from an #8. Nobody makes odd number frogs that I know of. Plus I’ve wanted to start casting for a really long time
Shawn, I understand. You’re going to look at the track a lot. So it has to look how you think it should. Follow your bliss!
Yep Ric, That’s the plan. Switches first. Then put the track down in the middle. Next will be the return loops. One is easy on flat ground the other on the trestle wont be to hard. I’m already playing with some designs for that It will be more like fancy bench work. The buildings will go last. I have an order in with the local supplier for some 1:20.3 textured concrete block! (http://www.largescalecentral.com/externals/tinymce/plugins/emoticons/img/smiley-wink.gif)
I got antsy last night and pulled all the equipment together. Wow now I have more motivation. Actually I wanted to see how the Mikado would do running through a #4 switch. Well, actually I was just pushing it but it seemed to go through ok. Very tight and the wheels were almost off the track if not, but it went through. Fun.
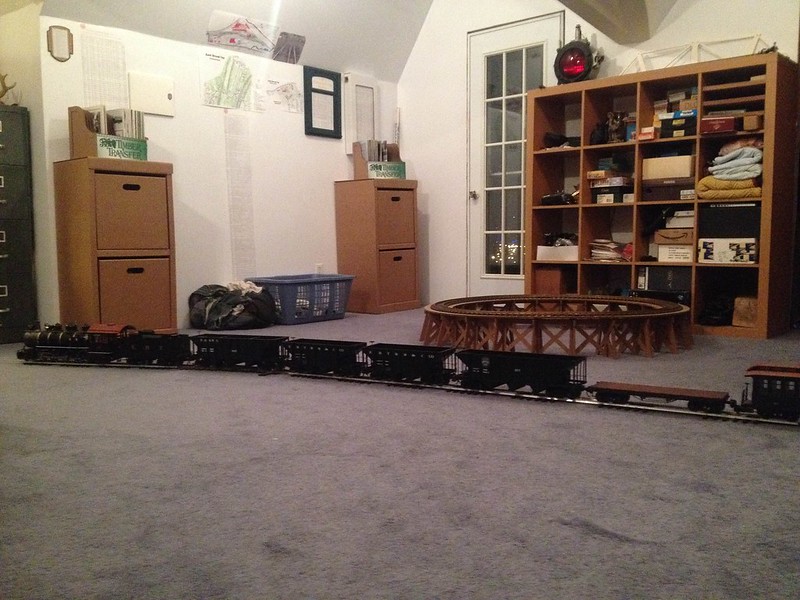
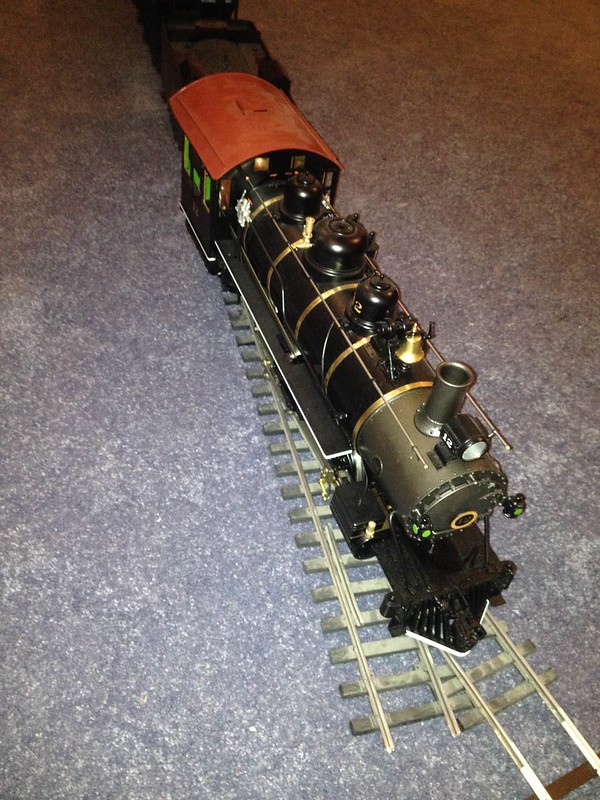