Haha! Y’all crack me up!!
Yeah, it’s way too big & complicated, but I’ve painted myself into a corner, and need to get moving on one of these mines. My wife wants me to get buildings in, and I’ve put it off for too long. So I figure if I spill the beans on the project and interact with you guys, I’ll feel more motivated to do something about it. At least that’s how it’s been so far.
So, herewith, beans will be spilled.
Of the (eight) mines in the layout plan, the H&N is medium-size, and the one I’ve put the most work into so far. Four years ago I worked up the puter model, based on a 1" structural foam core and a vague plan for sheating. Here’s a couple of shots from back then.
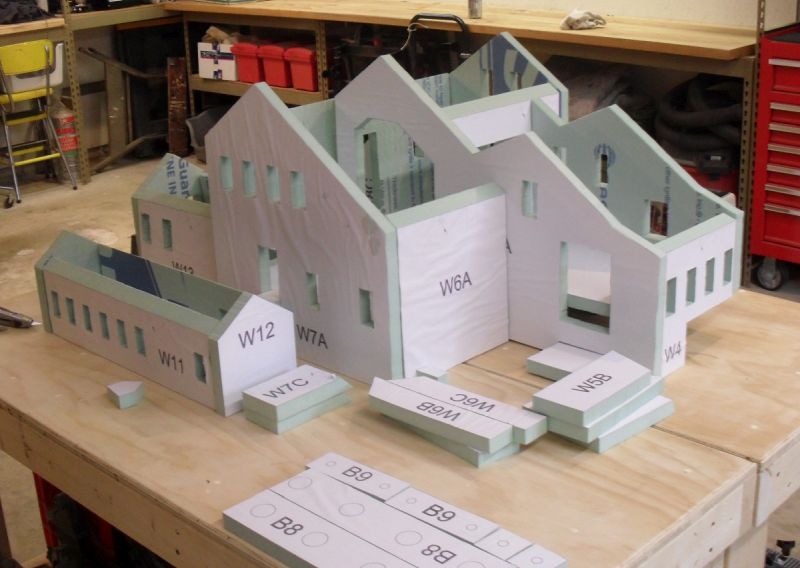

Putting that foam together was a blast! I also cast the doors and windows (in resin) for this.
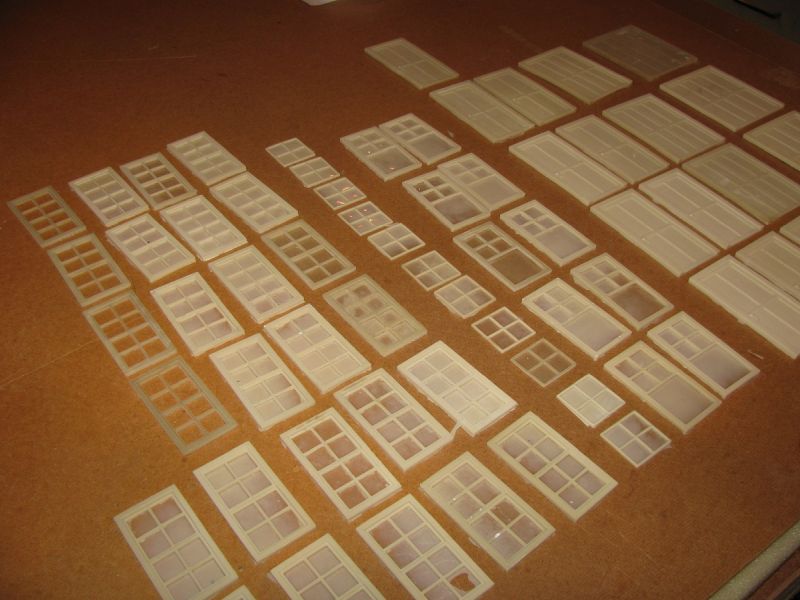
I worked hard on developing a means of making pre-weathered planks from styrene, and blew all kinds of time experimenting (with load testing) on how to glue styrene to this foam. John, and maybe Chris, you remember that.
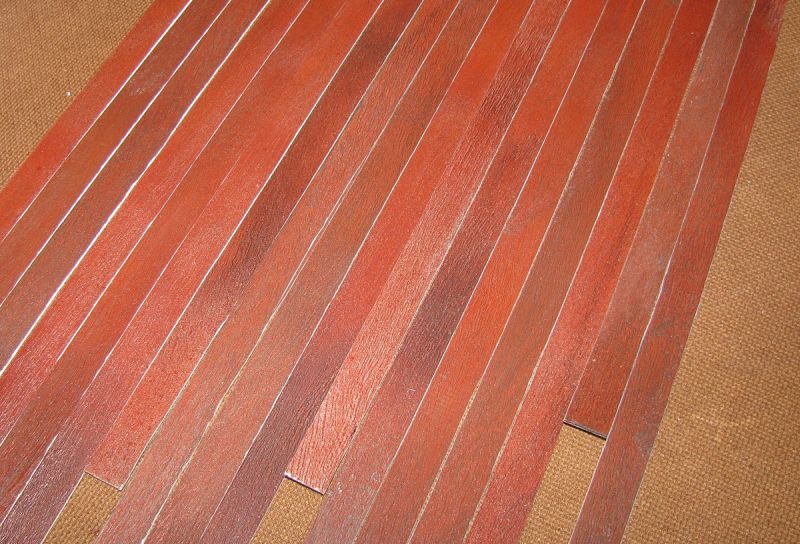
At this time I also made the plywood forms for the foundation and poured the concrete. The near one is the H&N, the further one is the Savage Mine.
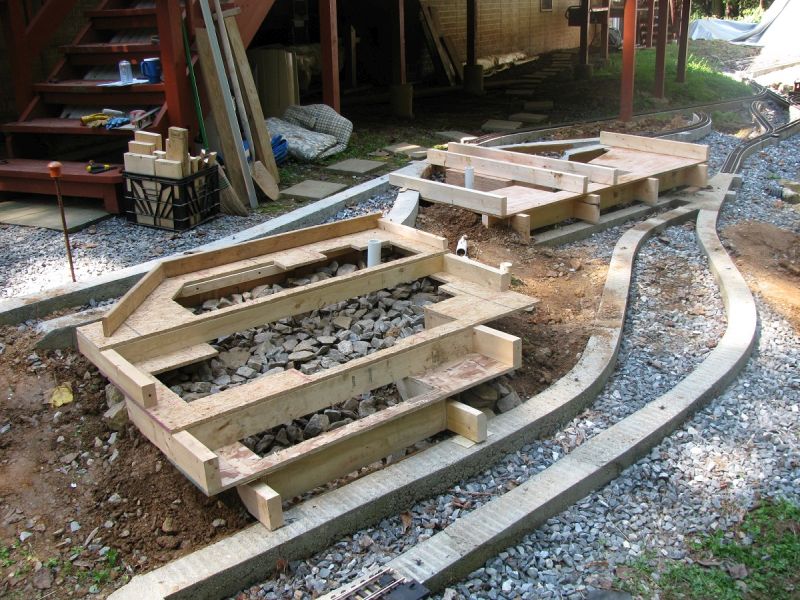
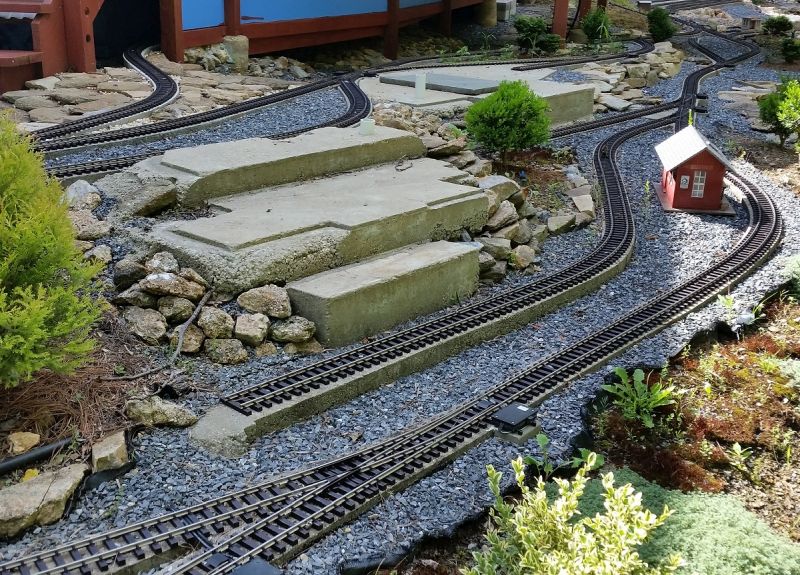

Again, this was four years ago and nothing’s been done since then. And besides needing to get a lot more infrastructural work done, I’ve had a problem with motivation. Mainly, I saw serious drawbacks to the foam method, at least how I was approaching it. Cutting holes for windows was sloppy; cutting it is very messy; cutting required warm enough weather to work in the unheated garage; walls are thick for lighting purposes; the full-size plotting of patterns was neither cheap nor easy to use. And it’s not straightforward on what adhesives will work with various materials.
So, fast forward to last December when I got a kit 3D printer working, and January where it began to seem possible to get a laser cutter. To me, as long as the ventilation could be worked out, that cutter would be the answer. Especially in permitting precise cutting of acrylic, and fitting them with 3d printed parts.
The “first laser building” was a test run on methods, and thanks to everyone who participated with me on that. I sure appreciated it, especially when things got bogged down.
So now, I’m starting with a foundation, doors and windows, and a computer model that nowhere reflects the needed design approach. Here’s some model pics.
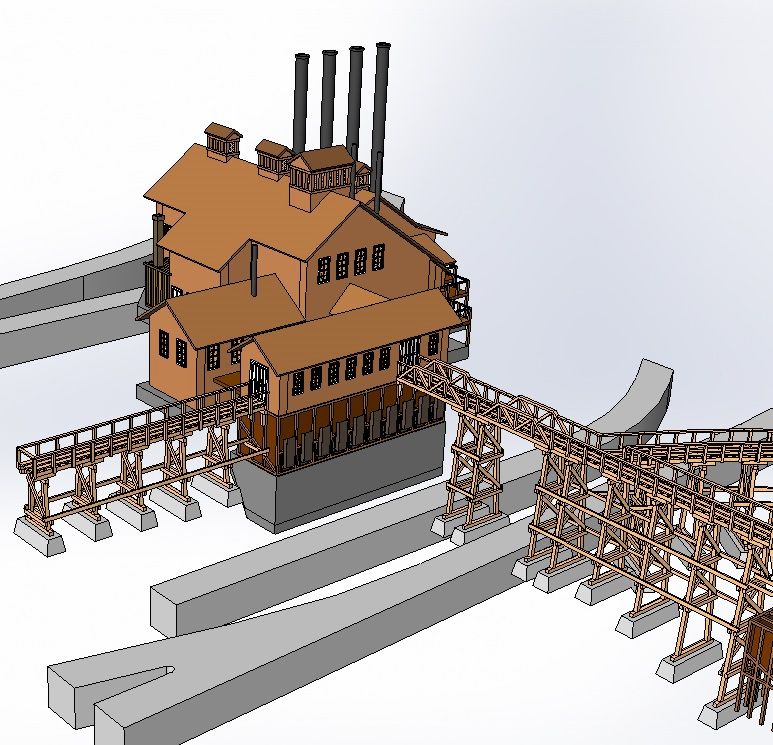
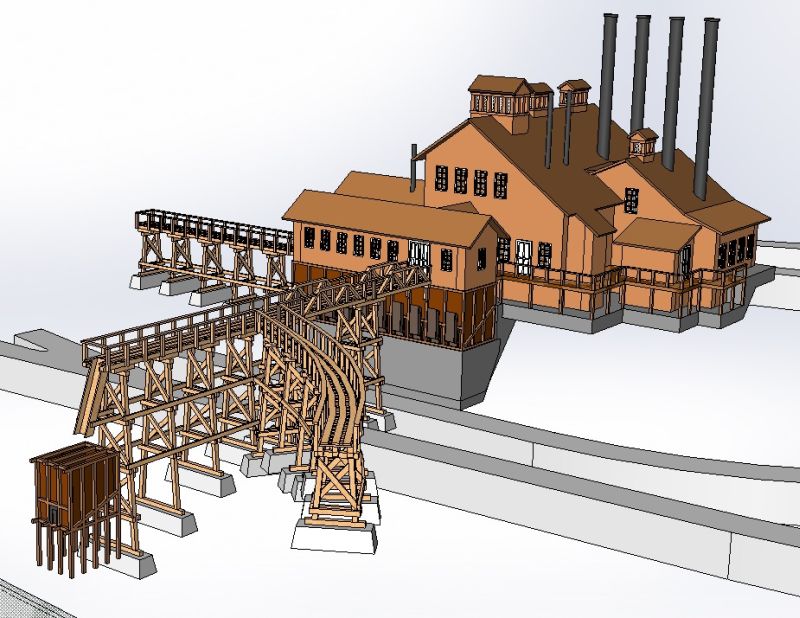


As you can see, the core model is woefully inadequate for an acrylic-based build. Furthermore, it needs to be divided into separable modules just so I can handle it (acrylic being much heavier).
In short, this will be a long-term thread; it might take me two years to build this thing, who knows. The model will have been laterally squished (50%) and vertically shrunk (~75%), so it won’t look anywhere near like an exact replica. Details will be lacking, mistakes will be plentiful. And all manner of interruptions will happen. But, spilling these beans is helpful to me, in regards to getting off my butt on the project. And if you’re intrigued or entertained along the way, that’s great.
Thanks for viewing,
===>Cliffy